Several main features of CNC machine tools in processing precision aircraft parts
- PRODUCT DETAIL
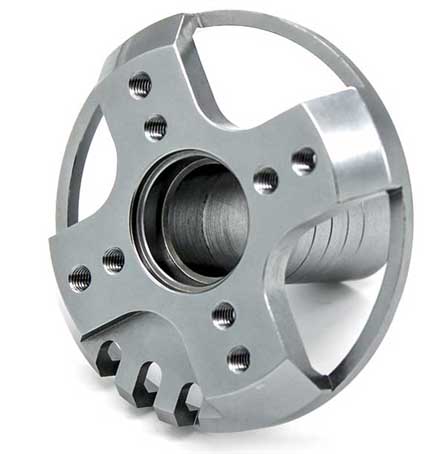
The main processing objects of CNC machine tools are aircraft parts with complex profiles, which solves the key equipment that is difficult to solve by ordinary processing methods. The biggest feature of CNC machining is the use of punched tape (or tape) to control the machine tool for automatic processing. Because airplanes, rockets and engine parts have different characteristics: Aircraft and rockets have large components, large size and complex shapes; Engine zero, small component size and high precision. Therefore, the CNC machine tools selected by the aircraft and rocket manufacturing departments and the engine manufacturing departments are different. Large-scale CNC milling machines with continuous control are mainly used in aircraft and rocket manufacturing. In engine manufacturing, both continuous-control CNC machine tools and point-control CNC machine tools (such as CNC drilling machines, CNC boring machines, machining centers, etc.) are used.
Process concentration
CNC machine tools generally have tool holders and tool magazines that can automatically change tools. The tool change process is automatically controlled by the program, so the process is relatively concentrated. Process concentration brings huge economic benefits:
⑴ Reduce the floor space of the machine tool and save the workshop.
⑵ Reduce or eliminate intermediate links (such as intermediate inspection of semi-finished products, temporary storage and handling, etc.), which saves time and labor.
automation
When machining on a CNC machine tool, manual tool control is not required, and the degree of automation is high. The benefits are obvious.
⑴ Reduced technical requirements for operators:
A senior worker of ordinary machine tools cannot be cultivated in a short time. However, the training time for a CNC employee who does not need programming is very short (for example, a CNC lathe worker only needs one week, and he will write simple processing programs). In addition, the parts processed by CNC workers on CNC machine tools have higher precision than those processed by ordinary workers on traditional machine tools, and it takes less time.
⑵ Reduce the labor intensity of workers: In the machining process, most of the time CNC workers are excluded from the machining process, which is very labor-saving.
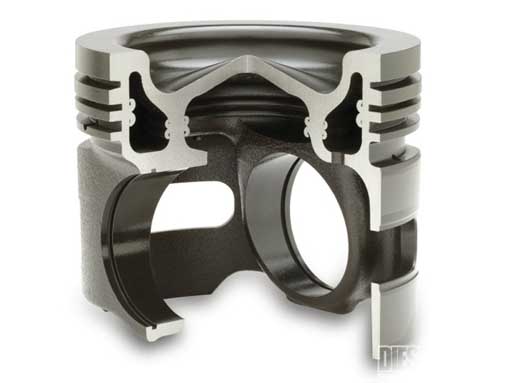
⑶ Stable quality of processed parts:
The processing automation of CNC machine tools eliminates the fatigue and carelessness of workers on ordinary machine tools and improves the consistency of products.
⑷ High processing efficiency:
The automatic tool change of CNC machine tools makes the processing process compact and improves labor productivity.
High flexibility of machined parts
Although the traditional general-purpose machine tool is flexible, its efficiency is low; Although traditional special planes are highly efficient, they have poor adaptability to parts, high rigidity, and poor flexibility, making it difficult to adapt to frequent product modifications brought about by fierce competition in the market economy. As long as the program is changed, new parts can be processed on the CNC machine tool, and it can be automated, with good flexibility and high efficiency. Therefore, the CNC machine tool can adapt to market competition.
Strong ability to process parts
The machine tool can accurately process various contours, and some contours cannot be machined on ordinary machine tools. CNC machine tools are especially suitable for the following occasions:
1. Parts that are not allowed to be scrapped.
2. Development of new products.
3. Processing of urgently needed parts.
Machining principles of precision parts
⑴ The processing of the previous process cannot affect the positioning and clamping of the next process.
⑵ Inside first, then outside, that is, the inner cavity (inner hole) is processed first, and then the shape is processed.
⑶ Processing procedures with the same installation or using the same tool should be carried out continuously to reduce errors caused by repositioning or tool change.
⑷ In the same installation, the process that has little effect on the rigidity of the workpiece should be carried out first.
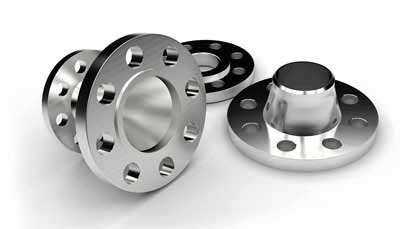
Processing route of precision parts
The feed processing route of CNC lathe refers to the path that the turning tool moves from the tool setting point (or the fixed origin of the machine tool) until it returns to this point and ends the processing program. Including cutting paths and non-cutting idle paths such as cutting in and cutting out of the tool. The feed path of finishing is basically carried out along the part contour sequence. Therefore, the focus of determining the feed route is to determine the feed route for rough machining and idle stroke. In CNC lathe processing, the determination of the processing route generally follows the following principles.
① The accuracy and surface roughness of the processed workpiece should be guaranteed.
② Make the processing route the shortest, reduce the idle travel time, and improve the processing efficiency.
③ Try to simplify the workload of numerical calculation and simplify the processing procedure.
④ For some reusable programs, subroutines should be used.
Making the machining program have the shortest feed route can not only save the execution time of the entire machining process, but also reduce unnecessary tool consumption and wear of the sliding parts of the machine tool's feed mechanism. The type and realization method of the shortest feed path are as follows.
⑴ The shortest cutting feed route. The shortest cutting feed path can effectively improve production efficiency and reduce tool loss. When arranging the shortest cutting feed route, it is also necessary to ensure the rigidity of the workpiece and the requirements of processing technology.
⑵ The shortest NC empty travel route.
① Use the starting point skillfully. An example of the general situation of rough turning using rectangular loop method. The setting of tool setting point A is to take into account the need for convenient tool change during finishing turning and other processing, so it is set at a position far away from the blank, and at the same time, the starting point and the tool setting point are overlapped
② Ingeniously set the tool change point. In order to consider the convenience and safety of tool change, sometimes the tool change point is also set at a position far away from the blank. Then, when the second tool is changed, the idle stroke path during fine turning must be longer; If the tool change point of the second tool is also set at the mother point position in the middle, the idle stroke distance can be shortened.
③ Reasonably arrange the "return to zero" route. In order to simplify the calculation process and facilitate the verification when manually compiling the processing program of the complex contour, the programmer sometimes sets the end point of the tool after each cut. By executing the "return to zero" operation instruction, all of them return to the position of the tool setting point, and then execute the subsequent program. This will increase the distance of the feed path and reduce production efficiency. Therefore, when rationally arranging the "return to zero" route, the distance between the end of the previous cut and the start of the next cut should be as short as possible. Or zero to meet the shortest feed path requirement. In addition, when selecting the command to return to the tool setting point, under the premise of no interference, use the x and z axis bidirectional “zero return” command as much as possible. The function "return to zero" route is the shortest.
⑶ Step cutting feed route of large margin blank. Lists two cutting feed routes for blanks with too much margin. It is a wrong step cutting route, cut in the order of 1→5, and the margin left for each cutting is equal. It is the correct step cutting feed route. Because under the same amount of knife back.
⑷ Continuous cutting feed route for finishing part contour. The finishing of the contour of the part can be arranged with one or several finishing processes. The final contour is completed by the last continuous machining. At this time, the advance and retreat position of the tool should be selected appropriately, and try not to arrange cutting and cutting out or tool change and pause in a continuous contour. So as not to destroy the balance of the process system due to sudden changes in cutting force. Causes scratches, shape changes or retained tool marks on the contour of the part.
⑸ Special feed route. In CNC turning processing, generally. The longitudinal feed of the tool is fed along the negative direction of the coordinate, but sometimes it is unreasonable to arrange the feed route in the normal negative direction. It may even damage the workpiece.
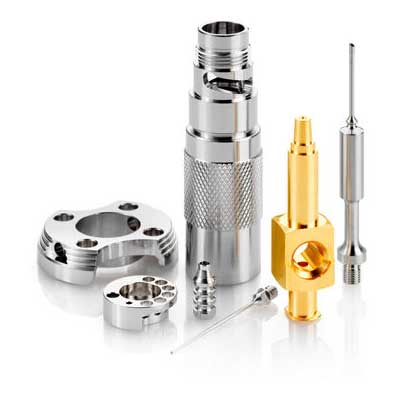
CNC machining has the following advantages:
① The number of tooling is greatly reduced, and complex tooling is not required for processing parts with complex shapes. If you want to change the shape and size of the part, you only need to modify the part processing program, which is suitable for new product development and modification.
② The processing quality is stable, the processing accuracy is high, and the repeat accuracy is high, which is suitable for the processing requirements of aircraft parts.
③ Higher production efficiency in the case of multiple varieties and small batch production. Can reduce production preparation, machine tool adjustment and process inspection time, and reduce the cutting time due to the use of the best cutting amount.
④ It can process complex surfaces that are difficult to process by conventional methods, and even process some unobservable processing parts. The disadvantage of CNC machining is that the cost of machine tool equipment is expensive and requires a high level of maintenance personnel.