Processing method of CNC turning stainless steel thread
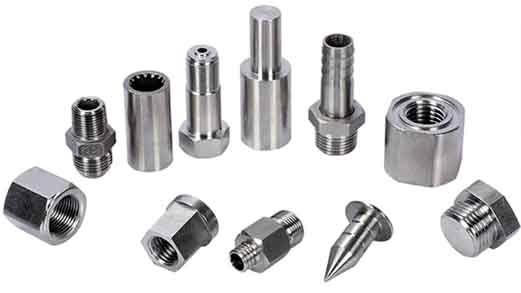
Problems of CNC turning stainless steel thread and countermeasures
The surface roughness of CNC turning thread is too poor. The most common phenomenon encountered in CNC turning stainless steel threads is: scale-like ripples and knife-biting phenomenon. The reasons for these phenomena are:
(1) The clearance angles of the two sides of the thread turning tool are too small, and the friction between the two sides of the cutting tool and the rear thread surface will deteriorate the machined surface. The influence of the thread rotation angle on the actual clearance angle of both edges must be considered during processing.
(2) The rake angle of the thread turning tool is too small and the cutting edge is not sharp enough. The chips cannot be cut smoothly, but are partially squeezed or torn off, which must cause the thread surface to be very rough. When the front angle is too large, the strength of the blade is weakened and it is easy to wear, chip, and pierce the knife, which is more likely to cause vibration and cause ripples on the thread surface. Therefore, the appropriate rake angle should be selected according to the different materials of stainless steel. When turning concentrated sulfuric acid resistant stainless steel threads, a smaller rake angle should be used than turning 2Cr13 stainless steel threads. The cutting edges on both sides of the turning tool should have very narrow cutting edges to avoid rapid wear of the cutting edges. When cutting 2Cr13, 1Cr17, 4Cr13, the cutting edge should be as sharp as possible, otherwise it will not be easy to achieve the required good surface roughness.
(3) thread cutter blade is dull, in fact, the rake angle, relief angle from large to small, the chips squeezed in the severe forming process, so that the cutting force increases during increased cutting vibration, serious deterioration of the machined surface. Therefore, when turning stainless steel threads, the blade must be kept sharp at all times and the cutter head must be replaced in time.
(4) Insufficient fixation of threaded turning tools, excessively extended tool heads, insufficient tool arbor rigidity, poor machine tool accuracy, loose spindles, loose tool holders and other factors can cause vibration and cause ripples on the threaded surface. Therefore, you must pay attention to the operation of the machine tool, cutting tool and workpiece during operation to make the system sufficiently rigid. When installing the turning tool, in addition to ensuring a firm installation and no looseness, the tip of the turning tool should be slightly higher than the center of the workpiece by 0.2-0.5mm, and never lower than the center to avoid cutting the tool.
(5) Avoid using the straight forward method when turning stainless steel threads. Due to the long chip contact length on the left and right sides, it is prone to vibration, which increases the load on the tool tip, causes vibration and increases the resistance during chip removal, and scratches the surface of the workpiece. Therefore, for the processing of stainless steel threads, it is best to choose the method of cross-turning threads. This method adopts the alternate lateral feed method, especially for the cutting of large-pitch threads and viscous materials. It is the most effective measure to solve the vibration problem. Since the cutting edges are used crosswise, the wear is even and the tool life can be prolonged.
(6) The matching degree of the cutting amount in the process of CNC cutting stainless steel threads directly affects the processing efficiency. If the cutting amount is too small, the tool wear will be aggravated, and if it is too large, the tool will collapse. Therefore, the number of cuts and the feed per cut will have a decisive influence on the thread turning. In order to obtain the best tool life, the workpiece diameter should not be larger than the major thread diameter 0.14mm, and the feed per tool less than 0.05mm should be avoided. The total cutting amount for machining should be set at about 0.1mm, the first cut depth should be 150-200% of the nose radius (R), and the maximum should not exceed 0.5mm. For austenitic stainless steel, a feed per cut of less than 0.08mm should be avoided. Common edge inserts with a small nose radius for internal threads may increase the number of cuts as the depth of the tool decreases. Thread size is unstable after CNC turning stainless steel. After thread processing. Use a thread ring gauge to measure that the "through end" of the external thread cannot be entered, or there are phenomena such as inconsistencies in the front and rear tightness and partial passage of the "stop end".
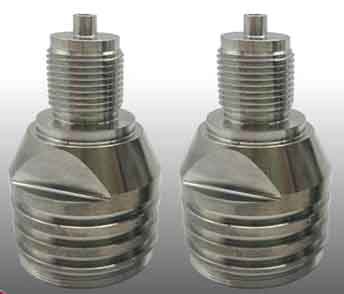
Reasons for these ills of thread:
(1) The thread profile is wrong. Even if the pitch diameter of the thread has reached the specified size, the thread ring gauge and plug gauge may still not be screwed.
(2) The thread is inverted. When measuring with a thread gauge, there is often a phenomenon that is restricted by the directionality. That is to say, it is tightened from one end and loosened from the other end, and even the phenomenon that the "through end" cannot pass but the "stop end" passes instead.
(3) If the bottom diameter of the internal thread is too small, or the bottom diameter of the external thread is too large, the thread gauge will not be screwed in. This is because the turning tool wears and becomes dull, and there is extrusion during the cutting process, which makes the outer diameter or inner diameter of the thread squeeze out of burrs.
(4) When turning internal threads with a small diameter, the rigidity of the turning tool bar is limited by the size. During the turning process, it is easy to produce "give a knife", and even the local size is large, which causes the local tolerance to be out of tolerance.
(5) When turning the stainless steel slender screw, due to the poor rigidity of the workpiece, deformation occurs during the turning process, resulting in dimensional errors on the thread.
(6) When turning the internal and external threads of stainless steel thin-walled workpieces, the workpiece will be locally deformed due to the force and cutting temperature, and the thread will also be locally out of tolerance. Therefore, in order to solve the problem of "the thread gauge cannot enter", corresponding measures must be taken for the above reasons, mainly from the aspects of correct installation and proper clamping of the workpiece.
The subtle role of cooling lubricating fluid in CNC thread cutting
Reasonable use of lubricating fluid can improve cutting conditions and achieve a multiplier effect. Attention should be paid when CNC cutting stainless steel threads:
Special requirements for cooling lubricants:
(1) Due to the toughness of stainless steel and the difficulty of being separated by cutting, the coolant is required to have higher cooling performance to take away a lot of heat.
(2) Due to the high viscosity and high fusion property, it is easy to produce built-up edge during thread cutting, so the coolant should have high lubricating performance.
(3) The coolant is required to have good permeability, which can penetrate into the fine gap lines of the metal area during cutting, so that the chips are easily broken.
(4) It must have a certain washing function.
Use several suitable coolants
(1) Vulcanized oil has good cooling performance and lubricating performance, and can be divided into direct and indirect according to different preparation methods. The formula of direct fluidized oil is 98% mineral oil and 2% sulfur. The indirect sulfurized oil formula is: mineral oil 78%-80%, black engine oil, vegetable oil 18%-20%, and sulfur 1.7%.
(2) F43 oil is suitable for cooling and lubricating stainless steel cutting, and has the best effect on stainless steel threads. The formula is: No. 5 high-speed motor oil 83.5%, calcium petroleum sulfonate 4%, barium petroleum phosphate 4%, oxidized petroleum fat barium soap 4%, zinc dialkylthiophosphate 4%, and disulfide 0.5%.
(3) Vegetable oil, such as soybean oil, helps to obtain better thread surface roughness and prolong tool life when turning threads.
In summary, whether it is martensitic stainless steel, ferritic stainless steel or austenitic stainless steel, or even austenitic + ferritic stainless steel, corresponding thread processing methods should be developed according to different metallographic structures . In order to achieve the ideal processing effect, create more economic and social benefits.