Die Entwicklung der Mikro Drehen und Fraesbearbeitung
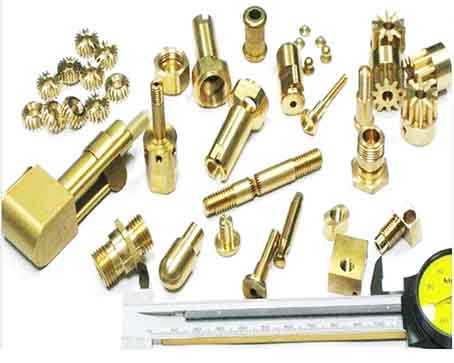
In den letzten Jahren hat die Nachfrage nach verschiedenen Mikro-Miniaturisierung Produkten für die CNC-Bearbeitung im Zivil- und Verteidigungsbereich zugenommen, und die Anforderungen an die Funktionen, die strukturelle Komplexität und die Zuverlässigkeit von Mikrogeräten sind ebenfalls immer höher geworden. Daher ist es von großer Bedeutung, Mikro bearbeitung technologien zu erforschen und zu entwickeln, die wirtschaftlich machbar sind, dreidimensionale geometrische Formen und verschiedene Materialien verarbeiten können und Strukturgrößen von Mikrometern bis Millimetern aufweisen. Gegenwärtig ist das Mikroschneiden eine wichtige Technologie geworden, um die Einschränkungen der MEMS-Technologie zu überwinden. Die Mikro Drehen- und Frästechnologie hat sich aufgrund ihrer hohen Effizienz, hohen Flexibilität und der Fähigkeit, komplexe dreidimensionale Formen und eine Vielzahl von Materialien zu verarbeiten, zu einem sehr aktiven Forschungsschwerpunkt entwickelt.
1959 schlug Richard P. Feynman (1965 Nobelpreisträger für Physik) die Idee von Mikro maschinen vor. Der erste Silizium-Miniatur drucksensor kam 1962 auf den Markt, und das Klima entwickelte Mikro maschinen wie Zahnräder, Zahnradpumpen, pneumatische Turbinen und Kupplungen mit einer Größe von 50-500 μm. 1965 entwickelte die Stanford University eine Silizium-Gehirn elektroden sonde und gelang es später, Tunnel Mikroskop und Miniature Sensoren abzutasten. 1987 entwickelte die University of California in Berkeley eine mikro elektrostatische Maschine aus Silizium mit einem Rotordurchmesser von 60-12 μm. Es zeigt das Potenzial der Verwendung der Silizium-Mikro bearbeitungs technologie zur Herstellung kleiner beweglicher Strukturen und kompatibel mit integrierten Schaltkreisen zur Herstellung winziger Systeme.
Die Forschung und Anwendung des traditionellen Mikro-Fräs- und Drehtechnik ist vor allem: Mikro-Schaftfräser mit einem Durchmesser von zehn Mikrometern bis 1 mm verwendet werden, für Mikro-Finish auf herkömmlichen Ultra präzisions-Werkzeugmaschinen. Da diese Werkzeugmaschinen hauptsächlich zur Bearbeitung nicht kleiner geometrischer Teile mit hoher Präzision verwendet werden, erfordern sie normalerweise teure Konstruktions- und Herstellungsprozesse, um die gewünschte Zielgenauigkeit zu erreichen. Für die Bearbeitung winziger Teile fehlt die notwendige Flexibilität, die Verarbeitungskosten sind hoch und die Effizienz gering. Miniaturisierte Verarbeitungsgeräte haben den Vorteil, Platz zu sparen, Energie zu sparen, einfach zu reorganisieren und kostengünstig zu sein. In den letzten Jahren auf die Verwendung von Mikro bearbeitungs maschinen zu erreichen Mikro-Fräs- und Drehbearbeitung hat große Aufmerksamkeit auf sich gezogen, und die Verwendung von Mikro-Tools auf Mikro-Werkzeugmaschinen umgesetzt wurde. In der Erforschung von Mikro-Fräs- und Dreh bearbeitungstechnik konzentriert sich die Forschung hauptsächlich auf der Oberflächenqualität, Schnittkraft, Werkzeugverschleiß und Leben, Chip-Zustand, und die Verarbeitungsfähigkeit von Kleinteilen.
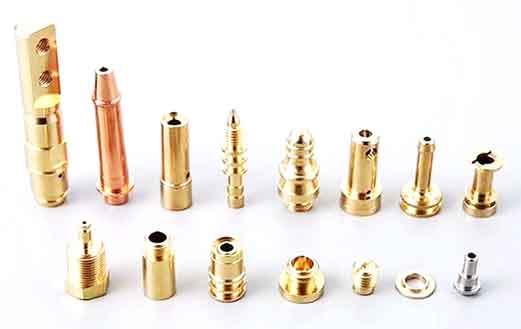
Beim Fräsen und Drehen ist der Belastungszustand des Werkzeugs äußerst kompliziert und es ist ständig mechanischen und thermischen Stoßbelastungen unterschiedlicher Größe und Position ausgesetzt. Da der Vorschub pro Zahn beim Mikromahlen und Drehen kleiner (oder gleich) dem Radius der Schneidkante des Werkzeugs ist, ändert sich der Schneidvorgang von Scheren zu Reibung, Extrusion oder Pflügen. Darüber hinaus unterscheidet sich die Mikro schneidkraft aufgrund der hohen Schnittgeschwindigkeit und der hohen Stoßbelastung stark von der herkömmlichen Fräskraft.
Bao und Tansel untersuchten die Schnittkraft bei Verwendung von Schaftfräsern mit Mikrodurchmesser zum Mikromahlen und schlugen ein verbessertes Schnittkraft modell vor. Das Modell wird erhalten, indem die Änderungen der Spanstärke berechnet werden, die durch die Flugbahn der Werkzeugnase verursacht werden, wenn sich das Werkzeug dreht und vorwärts bewegt. Darüber hinaus wird der Einfluss des Verhältnisses des Vorschubs pro Zahn Werkzeugradius, Werkzeugauslauf und Werkzeugverschleiß Schnittkraft betrachtet, und Experimente haben bestätigt, dass das Modell genauer als das herkömmliche Schaftfräser-Modell ist.
Vogler et al. Schlugen ein mechanisches Modell für das Mikroendfräsen vor, das unterschiedliche Phasen in heterogenen Materialien berücksichtigt. Es zeigt sich, dass die Mehrphasen im Metallmaterial die hochfrequente Änderung der Schneidkraft verursacht, was das Hochfrequenzsignal erklärt, das in der Schneidkraft auftritt, wenn das mehrphasige Material mikrogefräst wird.
Gegenwärtig gibt es nicht viel Forschung über die Mikrofräskraft, und es ist notwendig, die Eigenschaften der Mikrofräskraft besser zu verstehen. Es kann auch in Betracht gezogen werden, die Schneidmenge durch Echtzeitüberwachung der Schneidkraft dynamisch anzupassen, um die Schneidkraft zu steuern, die Qualität der bearbeiteten Oberfläche zu verbessern und die Lebensdauer des Werkzeugs zu verlängern.
Bei Verwendung eines Schaftfräsers mit kleinem Durchmesser für die Mikrobearbeitung ist es sehr schwierig, die bearbeitete Oberfläche nach dem Schneiden zu trimmen, so dass gehofft wird, dass der endgültige Bearbeitungsprozess mit einem Fräser abgeschlossen werden kann. Darüber hinaus beträgt die Schnittzeit für die hochpräzise Formbearbeitung häufig mehrere Stunden, sodass höhere Anforderungen an die Standzeit und die Schneidleistung gestellt werden.
Rahman et al. Führten Mikromahlversuche an reinem Kupfer mit einem Schaftfräser mit einem Durchmesser von 1 mm durch. Unter Verwendung der Antwort oberflächenmethode in der Statistik wurde ein quadratisches Modell der Werkzeuglebensdauer beim Mikromahlen von reinem Kupfer erstellt. Es wird der Schluss gezogen, dass die Schnittgeschwindigkeit und das Ausmaß des Rückgreifens einen signifikanten Einfluss auf die Werkzeuglebensdauer haben, während die Vorschubgeschwindigkeit keinen signifikanten Einfluss hat. Die Schneide zeigt nach dem Abstumpfen eine Zunahme der Schneidkraft. Gleichzeitig sollten der Durchmesser und die Schneidkantengröße des Mikrowerkzeugs berücksichtigt werden. Zhou et al. Verwendeten einen Schaftfräser mit einem Durchmesser von 2 mm, um Graphitelektroden mit hoher Geschwindigkeit zu fräsen. Es wird darauf hingewiesen, dass der Werkzeugverschleiß von abrasivem Verschleiß dominiert wird und die Verschleißformen Flankenverschleiß, Spanflächenverschleiß, Mikrorisse und Bruch sind. Die Spanformen sind klumpig, säulenförmig, kugelförmig und flockig. Die Lebensdauer des beschichteten Werkzeugs beträgt das 1,5-fache der Lebensdauer des unbeschichteten Werkzeugs. Es wird vorgeschlagen, dass die Verwendung einer Luftstrahldüse und eines Staubsaugers den Verschleiß und die Beschädigung des Werkzeugs wirksam verringern kann. Miyaguchi et al. Wiesen darauf hin, dass die Werkzeuglebensdauer durch Verringerung der Werkzeugsteifigkeit verlängert werden kann. Aufgrund der geringen Steifigkeit des Werkzeugs gleicht das Biegen des Werkzeugs die Schnittkraft aus und passt den Einfluss des Rundlaufs an, was zu einem gleichmäßigen Verschleiß der beiden Schneidkanten führt.
Beim Mikromahlprozess von Mikrowerkzeugen ist der Spanzustand ein wichtiger Faktor, um eine Präzisions bearbeitung zu realisieren, den Bearbeitungsprozess zu steuern und die Bearbeitungs fähigkeit zu beurteilen. Kim et al. Führten eine experimentelle Studie zur Spanbildung beim Mikromahlen durch. Fräsen von Rillen an Messing werkstücken mit unterschiedlichen Vorschubgeschwindigkeiten, Messen durch Sammeln von Spänen und Beobachten des REM-Bildes der Bodenfläche der Rille. Wenn der Vorschub pro Zahn kleiner als der stumpfe Radius der Schneidkante ist, beträgt das tatsächliche CNC-Spanvolumen ein Mehrfaches des nominalen Spanvolumens, und das Intervall der Vorschubmarkierungen ist auch größer als der Vorschub pro Zahn. Mit zunehmendem Vorschub pro Zahn nähert sich das tatsächliche Spanvolumen allmählich dem nominalen Spanvolumen. Es ist ersichtlich, dass beim Mikromahlen während des Vorschubs nicht immer Späne mit einem kleinen Vorschub pro Zahn gebildet werden, dh die Bildung von CNC-Spänen ist intermittierend und intermittierend.
Um die Qualität der Mikro-Fräsbearbeitung, der Verschleiß und die Lebensdauer des Werkzeugs zu verbessern, muss untersucht werden. Es kann in Betracht gezogen werden, den Verschleiß und Bruch des Werkzeugs durch Schnittkraft, Oberflächenrauheit und Werkzeug vibration zu untersuchen.