本文分析車削淬火鋼的製程設置, 高溫合金, 鈦合金, 冷硬鑄鐵, 及熱噴塗材料零件. 以及這些難切削材料的特點, 切割數量, 車削液, 和車削刀具.
淬火鋼車削技術
1. 變硬的鋼:
①硬化鋼的切割特性:
1) 高硬度: HRC45-70.
2) 高脆弱.
3) 高強度: σb= 2100 ~2600 MPa, 這是關於 4 時代 45 鋼.
4) 大型切割力: 單位切割力KC為4500MPA, 就是 2.5 時代 45 鋼.
5) 高切割溫度: 它的導熱率是 1/7 的 45 鋼.

淬火鋼車削技術
②轉動工具和切割硬化鋼的量:
1) 工具材料: 立方氮化硼, 陶瓷, 硬質合金 (600, 610, 渴望的, YT05, 758, 813), ETC.
2) 工具幾何參數: C0 = 0〜-10°, 工件硬度和連續切割γ0= -10〜-30°, A0 = 8 ~10°, κR= 30〜60°, λs= 0〜-3° .
3) 切割量: 水泥碳化物VC = 30 ~50m/min; 陶瓷工具VC = 60 ~120m/min; PCBN工具VC = 100〜200 m/min, VC是 1/2 間歇性轉彎期間的上述, αp和f是 1/2 一般鋼.
筆記: 一般來說, 淬火鋼的耐熱性為200 ~400℃, 它的硬度隨溫度升高而降低. 工具材料的耐熱性 (硬合金, 陶瓷, 立方氮化硼) 分別為800 ~1000℃, 1200℃, 1400~1500℃, 使用此功能, 連續切割, VC不能太低選擇; 鑽孔時, VC應該是合理的, 該工具應撤回; 在連續切割過程中, F應該很小, κR應適當減少, γε增加, λs應該為負.
超級合金的轉向技術
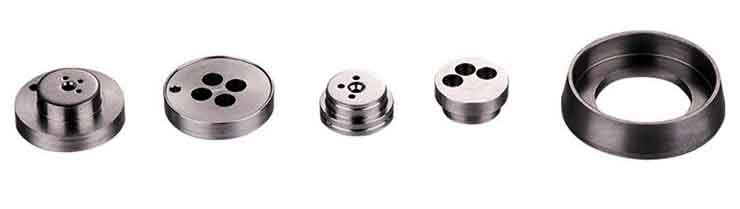
超級合金的轉向技術
2. 轉向超級合金
因為高溫合金包含許多高熔點合金元素Fe, 的, 鉻, 在, V, w, 莫等. 該元素和其他合金元素形成具有高純度和緻密結構的奧氏體合金. 包含的元素和非金屬元素c, 乙, n, ETC. 形成高硬度的金屬和非金屬化合物, 低比重, 和高熔點. 使其他可加工性非常差. 它相對轉向的可加工性只是 5-20% 的 45 鋼.
①超合金的轉彎特徵:
1) 大型切割力: 2 到 3 比切割一般鋼大的倍.
2) 高切割溫度: 50% 高於切割 45 鋼.
3) 嚴重的工作硬化: 切割表面和加工表面的硬度為 50-100% 高於矩陣.
4) 工具很容易穿: 粘附, 擴散, 氧化, 和凹槽磨損很容易發生.
tosing高溫合金工具的材料:
1) 高速鋼: 含高釩的高速鋼, 應使用高碳和鋁.
2) 水泥碳化物: 應使用YG的細和超細顆粒
③高溫合金轉動工具的幾何參數:
變形超合金: C0 = 10°, 鑄造超級合金: C0 = 0°, 通常不接受負面的倒角. A0 = 10 ~15°, 粗糙轉動λs= -10°, 細扭轉λs= 0 ~3°, κR= 45〜75°.
④扭轉超級合金數量:
1) 高速鋼切刀: VC = 3 ~8m/min.
2) 碳化物工具: VC = 10 ~60 m/min. 變形超合金: VC = 40〜60m/min. 鑄造高溫合金: VC = 7 ~10m/min. αp和f>0.1毫米.
⑤為高溫合金切割液: 與不銹鋼相同.
⑥高溫合金鑽孔: 應盡可能多地使用碳化物鑽或S型和淺孔鑽頭; 例如, 使用高速鋼鑽, 增加的大小 2 電線, 研磨α0和B, VC是 3 M/我, F為0.2 ~0.3mm/r; 鑽頭應該很鋒利, 直鈍的標準是 1/2 到 1/3 一般鋼. 最好使用自動飼料, 不要停在切割表面.
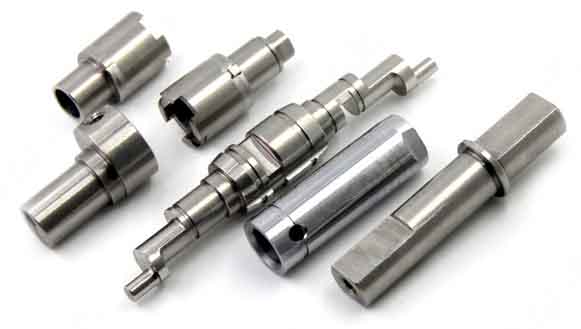
鈦零件車削技術
鈦零件車削技術
3. 鈦合金的轉動:
鈦合金是近幾十年來開發的一種新金屬. 因為它的特異性很高 (SB/P = 1680/4.5 = 373, 4.5 時代 45 鋼), 高熱強度 (長期工作在500℃), 良好的耐腐蝕性, 和出色的低溫性能, 它用於航空航天, 化工 , 醫療, ETC.
①鈦的切割特徵:
1) 鈦的切割溫度很高: 在相同的切割條件下, 它高的高度是切割的兩倍 45 鋼.
2) 鈦具有良好的親和力和認真的聯繫, 這將在高溫下引起粘合.
3) 鈦具有高化學活性: 在高溫切割條件下, 它與O反應, n, H, C在空氣中形成Tio2的硬皮膚層, 錫, tih, ETC。, 這帶來了切割困難.
②轉動鈦的工具材料:
1) 高速鋼: 除了普通的高速鋼, 最好使用高葡萄酒, 高銅, 和含鋁的高速鋼.
2) 水泥碳化物: YG8, YG6X, YG6A, 813, 643, YS27, YD15.3) PCD, PCBN天然鑽石.
③工具幾何參數: C0 = 5 ~15°, α0≥15°.
④轉動鈦的數量:
1) 高速鋼切刀: VC = 8 ~12 m/min.
2) 水泥碳化物工具: VC = 15 ~60 m/min.
3) PCD, PCBN天然鑽石工具: 濕切割VC = 200 m/min
幹切割VC = 100 m/min, AP>0.05毫米, F>0.05毫米/轉.
⑤鈦切割液: 乳液和極端壓力乳液用於一個. 極端壓力切割油用於完成.
⑥註明鈦:
轉動細長的軸 (桿), 現場中心和尼龍應用作工具支架和中心框架的爪子支架; 旋轉時, 使用蓖麻油 60% + 煤油 40% 切割液體; 敲擊時, 適當增加底孔的直徑.
4. 轉彎鑄鐵:
鑄鐵的表面層是白色的, 硬度可能達到HRC60; 單位切割力K C可以到達 3000 百萬帕, 就是 1.5 剪切的時間 45 鋼; 切割力集中在尖端附近, 加工中有毛孔和沙子, 切割時可以輕鬆損壞該工具;
它的脆性很大, 在切割過程中,邊緣碎屑和礦渣的現象將發生.
①用於轉動鑄鐵的工具材料:
1) 水泥碳化物: 應選擇具有高硬度和彎曲強度的膠結碳化物. 例如: ys2, 渴望的, YS10, 600, 610, 726.
2) 陶瓷: SG4, AT6, SM, FT80, FT85.
3) 立方氮化硼: 用於罰款.
②用於轉動鑄鐵的工具的幾何參數: 1) 碳化物: C0 = 0〜-5°, A0 = 5 ~10°, κR≤45°(κR= 45°), λs =-5~一10°, GE = 0.5~1毫米;
③切鑄鐵的量:
1) 碳化物工具: 粗加工VC = 7 ~10m/min, αP= 5 ~10mm, F = 0.5 ~1.5mm/r. 精加工: VC = 15 ~20m/min, αP= 0.5 ~2mm, F = 0.3 ~0.5mm/r.
2) 陶瓷工具: VC = 40 ~50m/min, αP= 0.5 ~2mm, f = 0.3~0.6mm/r.
3) PCBN切刀: VC = 60 ~70m/min, αP= 0.5 ~2mm, F = 0.1 ~0.3mm/r.
5. 熱噴塗的轉動 (焊接) 材料:
熱噴塗材料主要是多組分高強度合金. 高溫並在工件表面噴塗高速後, 硬度, 耐腐蝕性能, 工件表面的耐磨性和耐熱性得到了極大的改善, 它被廣泛使用. 基於銅和鐵的粉末噴塗的硬度更容易切割. 基於鈷和鎳的粉末噴塗的硬度是 >HRC50, 很難切割. 鈷層WC, 穿著鎳的WC, 和粘性的AL2O3噴塗塗料具有硬度> HRC65, 這是最難切割的.
①用於轉動熱噴塗材料的工具材料:
1) 水泥碳化物: 硬度>HRC45, 使用YG, YW膠結碳化物;
硬度, 使用 600, 610, 726, 767, YR05, YC12, ys2, 渴望的;
硬度>HRC65, 使用YG3X, YR05, YC09, YC12, 渴望的, 600, 610.
2) 陶瓷切割器: 3) 立方氮化硼
②轉動熱噴霧材料時工具的幾何參數: C0 = 0〜-5°, A0 = 8 ~12°, κR≤45°.
③切割熱噴塗材料的量: 水泥碳化物VC = 6 ~40m/min;
陶瓷切割器VC = 18 ~80m/min;
PCBN工具: VC = 24〜160m/min. αP= 0.15 ~0.6mm; F = 0.1 ~1mm/r.