加工中心執行多工序 (轉動, 銑削, 鑽孔, 無聊的, 竊聽, ETC。) 透過自動換刀和工作台分度對棱柱形零件進行多面複合加工. 實務證明複合加工中心確實有利於解決交貨期長的缺點, 資源利用率低, 中小型機械製造業在製品較多,資金周轉緩慢. 車銑複合加工因而在工業生產上得到越來越普遍的應用.
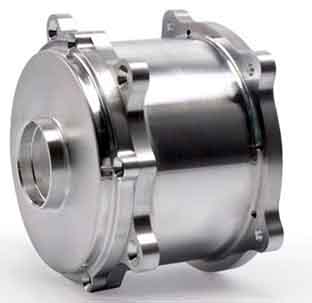
棱柱形零件的CNC加工
在那之後, CNC加工中心的主軸頭自動旋轉 90 轉換垂直和水平模式的學位. CNC加工中心不僅可以處理 4 盒子的側面, 但也處理第五表面 - 頂表面. 因此, 已經引入了所謂的5面加工中心, 這也可以被視為加工中心的複合處理功能的改進. 最近幾年, 隨著5軸連接CNC設備和編程軟件的價格降低和普及, 5-軸連接 (或多面) 加工中心已成為最近的國際機床展覽的新熱點. 最近, 引入了加工中心, 可以研磨並鑽 6 欄杆的面孔一個夾緊. CNC吧台材料加工中心是多面複合加工能力的新開發項目.
在具有不同處理方法的棱柱形零件的複合處理方面, 當前的引人注目的趨勢是銑削處理和激光處理或超聲處理的組合. 這家德國DMG公司幾年前在高速銑床上增加了一個激光處理頭, 並推出了DMU60L (當前模型是DML60HSC) 用於銑削和激光混合處理. 該機器配備了Q開關的YAG激光器,功率為100W, 光束直徑為0.1mm, 以及20mm3/min的處理效率. 工件之後 (主要是模具) 被夾在此機床上, 高速銑頭用於完成大部分工作, 然後使用激光用於層切割. 刪除輪廓的銑削痕跡,然後處理精美的零件, 包括雕刻圖案和圖案.
堅硬而脆弱的材料,例如玻璃, 陶瓷, 硬質合金, ETC。, 傳統技術很難處理. 然而, 如果將高頻振動運動添加到傳統銑削中, 鑽孔, 和研磨過程, 那是, 超聲技術與切割處理技術相結合, 處理效率將得到顯著提高. 德國DMG Company的DMS系列超聲處理機床使用主軸上的轉換器將超聲發電機的電氣高頻信號轉換為20KHz機械振動運動 (縱向運動). 然後由電壓調節器擴大並控制振動幅度, 然後將所有振動傳輸到銑刀, 由鑽石顆粒製成的鑽或研磨輪通過獲得專利的圓錐形工具支架. 機械加工過程中, 該工具連續挖掘在工件的表面上 20,000 每秒以微小顆粒的形式分離零件的表面材料. 不僅提高了其處理效率 5 與傳統方法相比, 但表面粗糙度也可以到達RA<0.2μm. DMS系列超聲處理機床有兩種類型: 3-軸連接控制和5軸連鎖控制. 主軸速度為20 ~6000R/min, 工具雜誌和自動工具更換器也是可選的. 因此,它成為一種機床,不僅具有超聲處理的功能, 但也可以執行多進程化合物處理,例如鑽孔, 銑削, 和研磨.