設定車銑鈦刀具幾何參數,提高鈦合金零件的產品質量. 產品快速準時交付.
(1) 刀具前角γ0: 鈦合金切屑與前刀面接觸長度短. 當前角較小時, 可以增加晶片的接觸面積, 使切削熱和切削力不會過度集中在切割刃附近. 改善散熱條件, 並能強化切割刃並減少崩刃的可能性. 車削鈦一般取γ0=5°~15°.
(2) 工具的間隙角α0: 鈦合金的加工表面具有較大的彈性恢復和嚴重的冷強化. 使用大量浮雕角度可以減少摩擦, 粘附, 粘附, 撕裂和側面造成的其他現象, 為了減少側面表面的磨損. 各種切割鈦合金工具的浮雕角度基本上大於或等於15°.
(3) 銑削工具的領先撓度角κR和二次撓度角κ´R: 銑削鈦合金, 切割溫度很高,彈性變形往往很大. 當過程系統的剛度允許, 應盡可能減少輸入角度,以增加切割零件的散熱面積並降低尖端的單位長度的負載. 一般來說, κR= 30°, κR= 45°. 減少次級撓度角可以增強工具尖端, 這有助於熱量耗散並降低加工表面的表面粗糙度值. 通常服用κ´R = 10°~15°.
(4) 工具λs的刀片傾斜角: 由於毛坯的粗糙表面和不平坦的表面結構, 尖端很容易在粗糙的轉彎時碎裂. 為了增加尖端的強度和清晰度, 應提高芯片的滑動速度. 一般來說, λs= -3°〜-5°用於粗糙轉彎, 和λs= o°以進行罰款.
(5) 工具Rε的鼻子弧的半徑: 車削鈦合金時, 工具提示是最弱的部分, 這很容易芯片和穿著, 因此,它需要磨碎工具尖端. 通常Rε= 0.5〜1.5mm.
負倒角 (Bγ= 0.03 ~0.05 mm, C01 = -10°~0°) 在轉彎期間使用, 芯片長笛底部的弧形半徑為rn = 6 ~8 mm.
另外, 工具銳化的質量對於提高其耐用性也非常重要. 碳化物切割工具應用鑽石磨牙磨刀. 切割時尖端必須很鋒利, 前後切割面的表面粗糙度RA值應小於0.4UM, 而且不允許尖端有微小的間隙. 工具銳化並接地之後, 它的耐用性可以提高 30%.
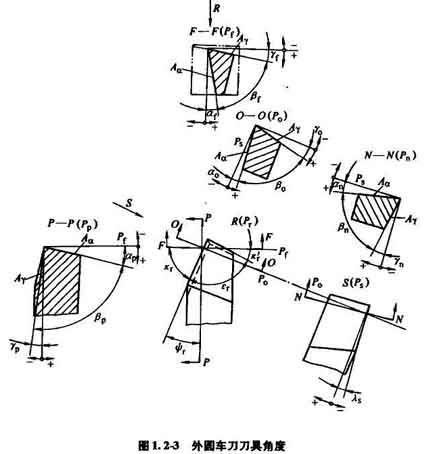
轉彎和銑削鈦的尖端角度的設計