銑削不銹鋼時高速鋼銑刀切削量的設定及銑刀的選擇
首先, 冷卻液會使切屑冷卻得太快並融入刀片, 導致刀具壽命縮短;
進給速度太高會造成物料堆積, 而進給速度太低會導致刀具與工件之間產生摩擦, 也會導致過熱.
實際上, 為了避免刀刃, CNC加工不銹鋼切削熱是必要的. 適用於不銹鋼銑刀, 應選擇適當的銑削速度,使切屑呈現淺棕色.
If the chips turn dark brown, it indicates that the cutting speed has reached the maximum limit. It is necessary to pay attention to the cutting speed when selecting the milling cutter when CNC machining stainless steel.
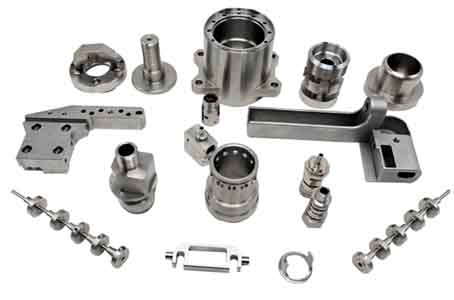
高速銑削不銹鋼零件參數
Cutting tools should be rigid, advanced, and have the highest possible overload capacity. It is best to mill stainless steel below 75% of the machine’s load calibration capacity.
Both the workpiece and the tool should be clamped firmly, and the extension of the tool should be as short as possible. Additional supports can be used if necessary. Whether it is a high-speed steel tool or a cemented carbide tool, it should be sharp at all times. It’s best to sharpen regularly, and don’t sharpen it when you have to.
Should use good performance lubricating fluid, such as chlorinated petroleum grease. This lubricant is particularly effective for powerful cutting where the feed rate is relatively slow.
For high-speed finishing cutting, it is recommended to use kerosene to dilute this lubricant. This mixed cutting fluid can keep the workpiece and tool at a lower temperature. Special attention should be paid to the cutting of Cr-Ni austenitic stainless steel. When cutting this stainless steel, you should be as careful as possible. It is possible to perform forced cutting to avoid pauses, so as not to cause work hardening and material slippage.
銑削不銹鋼的特點是: The adhesion and melting of stainless steel are strong, 而且切屑容易黏附在銑刀的刀齒上, which deteriorates the cutting conditions; 逆銑時, 刀齒首先在硬化表面上滑動, 這增加了加工硬化的趨勢; 銑削時, 衝擊、振動大, 使得銑刀的刀齒容易崩刃和磨損.
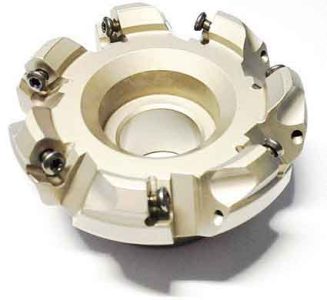
Milling tool for milling stainless steel parts
For milling stainless steel, except for end mills and some end mills, which can use cemented carbide as the material of the milling cutter teeth, the other types of milling cutters all use high-speed steel. In particular, tungsten-molybdenum series and high-vanadium high-speed steel have good effects, and the tool durability can be increased by 1 到 2 times compared with W18Cr4V. Cemented carbide grades suitable for making stainless steel milling cutters are YG8, YW2, 813, 798, YS2T, YS30, YS25, ETC.
When milling stainless steel, the cutting edge must be sharp and able to withstand impact, and the chip pocket must be large. Large helix angle milling cutters (cylindrical milling cutters, end milling cutters) can be used, the helix angle b is increased from 20° to 45° (n=5°), and the tool durability can be increased by more than 2 次. , Because at this time the working rake angle g0e of the milling cutter increases from 11° to over 27°, the milling is brisk. But the value of b should not be too large, especially for end mills with b≤35°, so as not to weaken the teeth.
Use wave-edge end mills to process stainless steel pipes or thin-walled parts. The cutting is brisk, the vibration is small, the chips are fragile, and the workpiece is not deformed. High-speed milling with cemented carbide end mills and stainless steel with indexable end mills can achieve good results.
Milling 1Cr18Ni9Ti with a silver-white chip (SWC) end mill, its geometric parameters are gf=5°, gp=15°, af=15°, ap=5°, kr=55°, k′r=35°, g01= -30°, bg=0.4mm, re=6mm. When Vc=50~90 m/min, Vf=630~750mm/min, and a’pb can reach 20=2~6mm, the milling power is reduced by 44% and the efficiency is greatly improved. 原理是在主切削刃上磨出負倒角, 並在銑削過程中人為地產生積屑瘤, 從而可以代替切削刃進行切削, and the rake angle of the built-up edge is ~~302. 由於主偏角的影響, 積屑瘤受到前刀面上產生的平行於切割刃的推力,成為流出的二次切屑, 從而帶走切削熱,降低切削溫度.
When milling stainless steel, 應盡可能採用順銑. 非對稱順銑方法可確保切削刃順利地切離金屬, and the contact area of the chip bonding blade is small. Under the action of high-speed centrifugal force, the chips are easily thrown away, so that when the cutter teeth re-cut into the workpiece, the chips impact the rake face and cause the phenomenon of blade spalling and chipping.
The spray cooling method has the most significant effect, 可使銑刀的耐用度提高一倍以上; 如果一個將軍 10% 乳化液用於冷卻, 應確保切削液流量以達到充分冷卻. 當硬質合金銑刀銑削不銹鋼時, take Vc=70~150 m/min and Vf=37.5~150 mm/min. 同時, appropriate adjustments should be made according to the alloy grades and workpiece materials.
share to:
銑刀類型 | Milling cutter diameter d (毫米) |
Rotating speed n (轉速) |
進給速度 F (毫米/分鐘) |
評論 |
立銑刀 | 3-4 5-6 8-10 12-14 16-18 20-25 32-36 40-50 |
1180-750 750-475 600-375 375-235 300-235 235-190 190-150 150-118 |
手動的 手動的 手動的 30-37.5 37.5-47.5 47.5-60 47.5-60 47.5-75 |
1) When the milling width and cutting depth are small, the feed amount is larger; 否則, take the small value 2) For milling cutters with three-sided edges, please refer to the same diameter disc milling cutter to select the cutting speed and feed 3) When the milling cutter is 2Cr13, the cutting amount can be adjusted according to the actual hardness of the material 4) When milling and cutting concentrated nitric acid resistant stainless steel, both n and f should be appropriately lowered. |
Disc milling cutter | 75 110 150 200 |
235-150 150-75 90-60 75-37.5 |
23.5 or manual 23.5 or manual 23.5 or manual 23.5 or manual |
– |