什麼是高壓鑄造? 大量生產壓鑄件的產品成本及價格
高壓壓鑄 (高壓DC) 是用於系列或大量生產的鑄造工藝. 低熔點鑄造合金通常用於此目的.
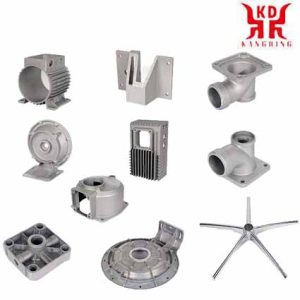
中國壓鑄
在壓鑄中, 將液態熔體壓入壓鑄模具中 (鑄造模具, 空腔) 在約高壓下. 10 到 200 MPa 且模具填充速度高達 12 米 / s, 然後它凝固的地方. 壓鑄製程的特殊之處在於採用永久模具, IE. H. 沒有模型. 因此, 對於一系列相同的部件,模具只需生產一次, 但生產工作量顯著提高. 這樣, 實現高產量, 特別是在熱室壓鑄機中,其中鑄造容器和鑄造活塞始終處於熔體中. 對於熔點較高的合金, 採用冷室壓力鑄造工藝; 鑄造裝置位於金屬熔體之外.
高壓鑄造過程是如何進行的?
在高壓鑄造過程中, 熔融金屬或金屬合金以高速、高壓注入模具中.
臥式高壓鑄機確保模俱全封閉. 它們根據可以施加的夾緊力大小進行分類,範圍包括 550 到 5700 噸.
取決於所使用的金屬, 填充模具的注射裝置可以是熱室或冷室. 熱室壓鑄, 金屬被固定在壓鑄機本身內, 然後它被吸入腔室,注射活塞的作用將其引入模具中. 機器的這些部件始終與熔融金屬接觸.
在冷室過程中, 金屬首先在單獨的熔爐中熔化,然後轉移到保溫爐中; 然後將其倒入填充室並注入模具中. 提供各種冷室高壓鑄造機.
壓鑄與塑膠射出成型競爭. 金屬材料在個別情況下具有優勢,可確保壓鑄製品的市場.
最常用的材料是
鋁 (壓鑄鋁)
鋅 (壓鑄鋅)
鎂 (鎂壓鑄件)
矽煙草
![]() 馬達外殼壓鑄件 |
![]() 路燈壓鑄件 |
![]() 配電箱壓鑄件 |
壓鑄件特性
壓鑄件具有光滑, 清潔表面和邊緣. 另外, 這種方法可以使壁厚比其他方法更薄. 含鋅, 例如, 該零件的壁厚可以為 1 毫米和鋁 1.4 毫米, 特殊情況甚至小於 1 毫米.
可實現的公差為± 0.05 至 ± 0.15 毫米, 因此人們談論的是精確的或成品的鑄件. 適用於大型鑄件, 然而, 需要稍大的公差.
可以使用其他材料製成的零件, 例如. 乙. 插座, 要澆注的螺紋螺栓或銷釘. 內螺紋直接用可旋轉鋼芯生產, 稍後可以再次刪除. 與其他工藝相比, 鑄造在這裡被稱為“鏡頭”. 最多可以執行 1000 每小時拍攝次數 (取決於機器的尺寸). 取決於鑄造材料, 模具壽命可達 2,000,000 鏡頭 (鋅合金).
帶鋁, 使用壽命約. 80,000 到 200,000 鏡頭實現. 許久, 壓鑄鋁被認為不適合熔焊和熱處理. 同時, 廣泛的研究使得製造適合熔焊和熱處理的壓鑄鋁成為可能. 翹曲度特別低的光束焊接工藝 (電子束和雷射光束焊接) 這裡應該強調 – 以獲得最佳的強度特性. 然而, 為了獲得最佳結果,有必要且建議在設計時考慮流程的要求. 另外, 然而, 壓鑄鋁也可以使用摩擦焊接工藝(例如攪拌摩擦焊)來很好地焊接.
壓鑄機
壓鑄機通常包含一個合模裝置,用於打開和關閉壓鑄模具. 鎖模裝置的組成 (也稱為結束部分) 是:
固定機板 (也稱為固定板) 固定固定鑄模的一半並, 在冷室製程中, 鑄件組
可移動的機器板 (還有手機板) 容納液壓頂出器和可動半模
移動機台板在其上進行引導的四個導柱
肘桿系統 (由汽缸板組成 (也稱為十字頭), 短槓桿和長槓桿以及十字頭)
鎖心
用鑄造活塞將液態金屬從鑄造室壓入模具中. 取決於所使用的機器類型, 溫室製程和冷室製程之間有區別. 鑄造活塞由鑄造裝置的驅動裝置驅動. 驅動活塞通常由液壓蓄能器作用. 在某些情況下,柱塞是由電力驅動.
壓鑄機週邊設備
外圍設備在壓鑄機附近工作. 這些是自動流程運作所必需的流程工程設備.
用於模具噴射或固定噴嘴的模具噴射機或機械手
加熱和冷卻裝置
提取裝置
計量爐或鋼包
真空輔助壓鑄工藝
具有強制通風功能的真空輔助壓鑄製程可使工件幾乎不含或不含氣體夾雜物. 鑄造開始時將型腔和填充室抽真空, 以便在鑄造過程中吸出其中所含的空氣和產生的氣體,從而在熔體中形成較少或不形成空氣夾雜物.
壓鑄再壓縮
透過在工件最終凝固之前的階段進行高壓縮,可以達到類似的效果. 毛孔和氣穴顯著減少.
正如熔體凝固過程中. h 在從液體到固體的轉變過程中,體積發生躍變, 厚壁部件內部不可避免地會出現體積不足.
為了補償液體收縮的影響, 所謂的擠壓製程可用於壓縮正在凝固的熔體. 為此目的, 漿狀熔體透過壓鑄模具中預期體積不足的區域中的「擠壓銷」進行壓縮.
壓鑄模具及工具
壓鑄製程所需的壓鑄工具是在工具車間或模具車間製造的. 符合 DIN EN ISO 的特殊材質或高強度熱作鋼 4957 通常用作鑄造模具的材料. 下表顯示了一個選擇.
材料簡稱 | 物料編號 |
32鉻鉬釩 12-28 | 1.2365 |
X37CrMoV 5-1 | 1.2343 |
X40CrMoV 5-1 | 1.2344 |
壓鑄相序
在壓鑄中, 預調質的 (100 到 300 攝氏度) 永久模具 (兩個或更多零件) 在壓力下高速充滿熔融金屬. 實際鑄造過程可分為三個階段.
預填充階段用於將鑄造室中的熔體輸送至澆口. 由於活塞速度相對較低,第一階段在澆道系統中壓縮的空氣可以透過通風通道和成型平面逸出 (0.05–0.7 m / s).
在模具填充階段, 鑄造活塞以極高的速度將熔體壓入模具中 (0.4–6 m / s). 模具填充時間極短,為 5–60 ms. 因此實際上不可能對模具進行排氣.
在模具填充結束時的保壓階段, 建立非常高的靜態最終壓力. 填充模具時截留的空氣被壓縮,並補充鑄件.
鑄造壓力
不同的鑄造材料需要不同的鑄造壓力. 鋁和鎂合金在 300–1200 bar 下鑄造, 鋅為 130–250 bar,黃銅為 300–1000 bar. 高鑄造壓力下工件的強度較大.
![]() 壓鑄件的表面處理 |
![]() 散熱器外殼壓鑄件 |
![]() 絞肉機外殼壓鑄 |
鋁矽熔體的收縮行為
如果你在大約 700 ° C 進入模具型腔,使模具完全充滿, 那麼金屬的體積總共減少到室溫約 1.3% 由於它的收縮. 在這個總數中, 0.05% 是由於液體收縮造成的, 0.75% 到凝固和 0.5% 到固體收縮.
這一數量缺口為 1.3%, 鋁合金比純金屬小不了多少, 在凝固鑄件中以體積缺陷的形式變得明顯. 除了正常的收縮外, 這些缺陷部分以縮痕的形式出現, 部分為大孔或縮孔.
壓鑄模具中的收縮不能像砂鑄模具中那樣不受阻礙地發生, 例如. 在鑄造技術方面, 期限 “收縮” 方法, 除了一個過程, 一項措施, 即冷卻鑄件與工作溫度下模具尺寸的百分比尺寸偏差. 收縮是否可以自由發生或有阻礙地發生幾乎完全取決於鑄件的幾何形狀. 因此,收縮率可能為 0.5% 當今普遍使用的一種方法可以在同一個鑄件上用於多種尺寸, 儘管 0.4% 對於其他地區可能仍然太多. 模具尺寸應考慮相關壓鑄合金的收縮圖來決定.
壓鑄收縮率
壓鑄合金 | 收縮率% |
鋁合金 | 0,5–0,7 |
鎂合金 | 0,5–0,8 |
鋅合金 | 0,4–0,6 |
合金元素對鋁合金鑄造合金的影響
矽
結構
和 12.5% 矽, 鋁形成共晶1,熔化溫度為 577 °C. 在二元系統中,鋁和矽之間沒有聯繫. 矽在固體鋁中的溶解度為 1.65% 處於平衡狀態 577 °C。, 下降到 0.22% 在 300 °C. 在更低的溫度下甚至更進一步. 如果合金的矽含量多於對應的溶解度, 該結構不僅含有鋁混晶,還含有矽晶體. 如果冷卻速度不是特別快, 矽在共晶混合物中以角晶體的形式凝固, 針和板. 這些形式的訓練是透過 z 的少量混合來實現的. 乙. 鈉, 鍶, 受銻或磷影響. 由於快速凝固,壓鑄會產生類似的效果.
共晶1是合金元素的混合物, 所有可能的成分中哪一種熔點最低. 共晶點, 例如. 例如 .: 鋁矽合金, 是 12.5% 和 577 °C.
鑄造性能
Si含量越高, 對流動性和充模能力越有優勢. 隨著Si含量的降低,流動性變差.
矽對攝食行為的影響
隨著Si含量的增加, 超過 11%, 宏觀空隙體積急劇增大. 入射體積與巨觀空隙體積的方向相反. 小於 9% 和, 厚壁零件往往有抽吸腔. 壓鑄中大型氣孔的補給選項受到限制 (澆口處的厚壁鑄件會導致一些問題, 因為注射過程中累積的材料最後被填充然後固化). 在亞共晶合金中, 由於吸入點過熱,粗顆粒變得明顯.
近共晶熔體 (大約 11% 和) 導致更強的宏觀空隙. 共晶和近共晶鋁矽熔體, 這導致“顆粒狀”或“細化”結構, 凝固並形成外圍殼 (外源凝固), 使這些熔體不易出現吸孔.
鐵
較高的鐵含量對壓鑄件有正面影響 (例如, 合金 EN AC-AlSi9Cu3 (鐵) 最大限度. 1.2%), 因為它減少了金屬黏附到模具表面的傾向. 在公差範圍內, 鐵通常對鑄造性能沒有影響. 由於鑄造廠熔化或加工方法不當而導致的意外增加可能會導致鑄件脆化並形成不想要的空腔, 熱裂紋或縮痕. 保持溫度和澆注溫度較低, 經常發生重力偏析, 聚集在爐底上. 分離產物由鐵組成, 錳和矽. 偏析產品硬度為500-1000維氏.
銅
銅添加劑減少凝固收縮. 因此, 含銅鋁合金更容易實現壓力密封鑄件. Cu 添加劑對強度和切削加工性有正面影響. 銅會降低耐腐蝕性.
錳
添加百分之零點幾的錳可減少鐵對伸長率和抗衝擊性的負面影響. 然而, 如果鐵和錳的含量較高, 它們可以在不利的熔化條件下, 例如. 乙. 透過低保持溫度, 導致硬隔離.
鎂
同時存在矽, 銅或鋅, 鎂由於硬度增加而改善切削加工性. 鎂對腐蝕行為沒有負面影響. 鎂在汽車產業也變得越來越有趣, 特別是因為它的重量較輕.
鎳
添加鎳最重要的優點是耐熱性的增加. 尤其是活塞和汽缸蓋是含鎳鋁合金的主要應用領域.
鋅
不同的鋅含量在允許範圍內一般沒有任何影響. 在壓鑄中, 在容易產生熱裂紋的零件中,鋅和鎂的含量有時會降低.
鈦
鈦主要作為晶粒細化劑添加到鋁合金中,最多可達 0.15%. 對於砂型和金屬型鑄造合金, 它是一種細化晶粒的合金成分.
帶領
在固態, 鉛以細小液滴的形式不溶解. 在公差範圍內 (<0.1%), Pb 對合金性能沒有顯著影響.
錫
含量超過 0.02%, 錫沿著晶界分離,如果超過正常公差,會對熱裂行為產生非常負面的影響 – 尤其是在壓鑄領域.
壓鑄與注塑的比較
鑄造機的投資成本與模具的高額製造成本大致相當. 在兩個過程中, 大量的零件必須證明這些高投資成本是合理的. 在那之後, 原料成本優先.
壓鑄金屬部件具有明顯更高的彎曲強度 (剛性) 比注塑成型的; 它可以達到 20 高出幾倍. 壓鑄生產的工件在較高溫度下仍能承受負荷 (鋁高達約. 450 °C). 對於注塑材料, 在較高溫度下強度和剛度急劇下降 (從 100 °C); 唯一的例外是昂貴的特種塑料. 另一個優點是當組件 (除鋅外) 有壓力, 沒有蠕動, 與許多注塑工件的情況一樣. 壓鑄件具有更好的結構穩定性, IE. 經過機械加工的表面仍然是表面, 由此塑膠部件的表面更容易變形. 另外, 有些注塑塑膠在氣候條件下會改變形狀. 壓鑄材料具有電磁屏蔽性且耐有機溶液. 另外, 可以在不損失品質的情況下進行回收.
如果使用標準材料,注塑組件會更便宜. 另外, 顏色可用於注塑. 另一個優點是與壓鑄工件相比重量更輕. 後者的腐蝕性能也較差. 另外, 壓鑄金屬零件的生產更加複雜 “複雜的” 幾何形狀有時是不可能的.