近期某公司新產品樣機加工中, 某些工件是由不銹鋼和其他難以通過CNC加工材料製成的, 例如3CR13, 3CR13MO, 40讓我們黑色, 9鉻鉬釩, ETC. 過去也已經處理過這種類型的工件. 雖然生產效率較低, 批次很小, 數量很小, 生產週期很短. 大規模生產後, 問題暴露了, 這些工具嚴重磨損了, 磨刀的數量增加了, 停機時間和機床調整時間增加了. 工件的表面粗糙度很差, 切屑不易捲曲和斷裂, 並且工件的處理表面被刮擦, 直接影響工件的質量.
工件的材料為3Cr13mo, 並且過程要求由CNC車床處理,除了RA0.8µM的每個外圈的打磨. 力量, 伸長, 減少面積, 3CR13MO鋼的影響性能高於 40 鋼鐵和 45 鋼. 是一種強度高、塑性好的中碳馬氏體不銹鋼. 在工件的試用期間, 根據轉動普通碳鋼的技術方法進行了3CR13MO鋼的轉彎測試. 結果是切割過程中嚴重的工作硬化, 高切割電阻, 高切割溫度, 並容易粘貼工具, 導致建立優勢. 導致工件的大小改變並影響工件的形狀和位置公差和表面粗糙度.
針對以上問題, 已經從多個方面採取了措施,以使工件的處理表面達到圖案所需的大小和表面粗糙度, 並確保高生產效率.
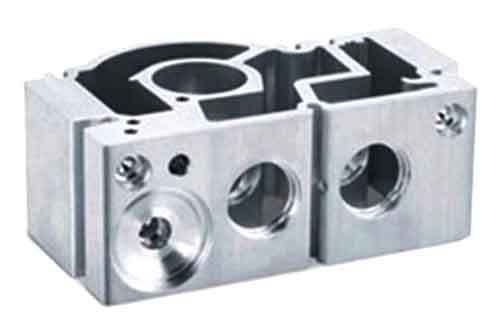
不銹鋼零件加工品質控制
1. 熱處理改變了材料的硬度
熱處理後,馬氏體不銹鋼的不同硬度對轉動處理有很大影響. 桌子 1 顯示YW2材料轉彎工具在轉動和熱處理3Cr13m材料工件後使用不同硬度的工具. 可以從桌子看 1 儘管退火的馬氏體不銹鋼具有低硬度, 其轉彎性能較差. 這是因為該材料具有較大的塑性和韌性, 結構不均勻, 附著力強、熔合力強, 並且在切割過程中很容易產生刀口, 並且要獲得良好的表面品質並不容易. 調質後, 硬度在30HRC以下的3Cr13Mo材質工件具有較好的切削加工性,容易獲得較好的表面品質. 雖然硬度大於30HRC的工件表面品質較好, 車刀容易磨損. 所以, 機械加工前進行調質處理, 硬度達25-30HRC, 然後進行切割.
2. 用於加工馬氏體不銹鋼的切削刀具材料
工具材料的切割性能與工具的耐用性和生產力有關. 工具材料的製造性會影響工具本身的製造和銳化質量.
為工具切割部分選擇材料的原理是具有較高的磨損性並保持其切割性能在較高的溫度下.
目前常用的轉彎工具材料是: 高速鋼和水泥碳化物. 因為高速鋼只能在600°C以下保持其切割性能, 不銹鋼切割過程中產生的高溫通常高於600°C. 和碳化物的碳化物比高速鋼具有更好的耐熱性和耐磨性, 因此,用碳化物材料製成的工具更適合切割不銹鋼. 在相同切割參數的條件下, 對幾種合金材料的工具進行了轉彎比較測試.
帶有TIC-TICN-TIN複合塗層刀片的外部轉彎工具具有很高的耐用性, 良好的表面質量和高生產率. 這是因為塗有膠結碳化物材料的葉片具有更好的強度和韌性. 而且由於其表面具有更高的硬度和耐磨性, 較小的摩擦因子和較高的耐熱性, 它已成為轉動不銹鋼的好工具材料. 僅限於沒有這種材料的切割刀片, 表中的比較測試 2 表明YW2水泥碳化物的切割性能也更好, 因此,您可以選擇YW2材料刀片作為切割刀片.