Paslanmaz çeliğin frezelenmesi için yüksek hız çeliği freze takımının kesme miktarını ve freze takımı seçimini ayarlayın
Öncelikle, soğutma sıvısı talaşları çok çabuk soğutacak ve bıçağın içine karışacaktır, takım ömrünün azalmasına neden olur;
Çok yüksek bir ilerleme hızı malzeme birikmesine neden olur, çok düşük ilerleme hızı takım ile iş parçası arasında sürtünmeye neden olur, ve ayrıca aşırı ısınmaya neden olur.
Aslında, bıçağın keskin kenarını önlemek için, CNC işleme paslanmaz çelik kesme ısısı gereklidir. Paslanmaz çelik frezeleme takımları için, talaşların açık kahverengi bir renge sahip olması için uygun frezeleme hızı seçilmelidir.
If the chips turn dark brown, it indicates that the cutting speed has reached the maximum limit. It is necessary to pay attention to the cutting speed when selecting the milling cutter when CNC machining stainless steel.
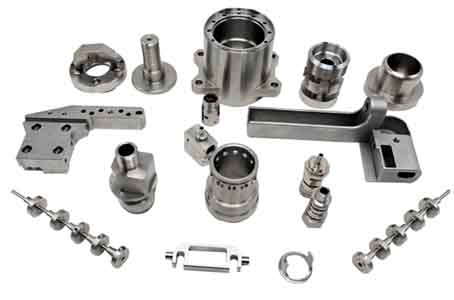
Yüksek hızlı frezeleme paslanmaz çelik parçaların parametreleri
Cutting tools should be rigid, advanced, and have the highest possible overload capacity. It is best to mill stainless steel below 75% of the machine’s load calibration capacity.
Both the workpiece and the tool should be clamped firmly, and the extension of the tool should be as short as possible. Additional supports can be used if necessary. Whether it is a high-speed steel tool or a cemented carbide tool, it should be sharp at all times. It’s best to sharpen regularly, and don’t sharpen it when you have to.
Should use good performance lubricating fluid, such as chlorinated petroleum grease. This lubricant is particularly effective for powerful cutting where the feed rate is relatively slow.
For high-speed finishing cutting, it is recommended to use kerosene to dilute this lubricant. This mixed cutting fluid can keep the workpiece and tool at a lower temperature. Special attention should be paid to the cutting of Cr-Ni austenitic stainless steel. When cutting this stainless steel, you should be as careful as possible. It is possible to perform forced cutting to avoid pauses, so as not to cause work hardening and material slippage.
Paslanmaz çeliğin frezelenmesinin özellikleri şunlardır:: The adhesion and melting of stainless steel are strong, ve talaşların freze bıçağının dişlerine yapışması kolaydır, which deteriorates the cutting conditions; Yukarı frezeleme yaparken, kesici dişler önce sertleştirilmiş yüzey üzerinde kayar, bu da işin sertleşme eğilimini artırır; Frezeleme yaparken, Darbe ve titreşim büyük, bu da freze bıçağının kesici dişlerinin talaşlanmasını ve aşınmasını kolaylaştırır.
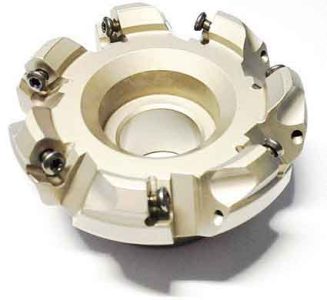
Milling tool for milling stainless steel parts
For milling stainless steel, except for end mills and some end mills, which can use cemented carbide as the material of the milling cutter teeth, the other types of milling cutters all use high-speed steel. In particular, tungsten-molybdenum series and high-vanadium high-speed steel have good effects, and the tool durability can be increased by 1 ile 2 times compared with W18Cr4V. Cemented carbide grades suitable for making stainless steel milling cutters are YG8, YW2, 813, 798, YS2T, YS30, YS25, vesaire.
When milling stainless steel, the cutting edge must be sharp and able to withstand impact, and the chip pocket must be large. Large helix angle milling cutters (cylindrical milling cutters, end milling cutters) can be used, the helix angle b is increased from 20° to 45° (n=5°), and the tool durability can be increased by more than 2 zamanlar. , Because at this time the working rake angle g0e of the milling cutter increases from 11° to over 27°, the milling is brisk. But the value of b should not be too large, especially for end mills with b≤35°, so as not to weaken the teeth.
Use wave-edge end mills to process stainless steel pipes or thin-walled parts. The cutting is brisk, the vibration is small, the chips are fragile, and the workpiece is not deformed. High-speed milling with cemented carbide end mills and stainless steel with indexable end mills can achieve good results.
Milling 1Cr18Ni9Ti with a silver-white chip (SWC) end mill, its geometric parameters are gf=5°, gp=15°, af=15°, ap=5°, kr=55°, k′r=35°, g01= -30°, bg=0.4mm, re=6mm. When Vc=50~90 m/min, Vf=630~750mm/min, and a’pb can reach 20=2~6mm, the milling power is reduced by 44% and the efficiency is greatly improved. The principle is to grind a negative chamfer on the main cutting edge, and artificially generate a built-up edge during milling, so that it can replace the cutting edge for cutting, and the rake angle of the built-up edge is ~~302. Due to the effect of the entering angle, the built-up edge is subjected to a thrust parallel to the cutting edge generated on a rake face and becomes a secondary chip flowing out, thereby taking away the cutting heat and reducing the cutting temperature.
When milling stainless steel, down milling should be used as much as possible. The asymmetric down milling method can ensure that the cutting edge is smoothly cut away from the metal, and the contact area of the chip bonding blade is small. Under the action of high-speed centrifugal force, the chips are easily thrown away, so that when the cutter teeth re-cut into the workpiece, the chips impact the rake face and cause the phenomenon of blade spalling and chipping.
The spray cooling method has the most significant effect, which can increase the durability of the milling cutter by more than double; If a general 10% emulsion is used for cooling, the cutting fluid flow rate should be ensured to achieve sufficient cooling. When the carbide milling cutter mills stainless steel, take Vc=70~150 m/min and Vf=37.5~150 mm/min. Aynı zamanda, appropriate adjustments should be made according to the alloy grades and workpiece materials.
share to:
Type of milling cutter | Milling cutter diameter D (mm) |
Rotating speed N (r/min) |
Feed rate f (mm/dak) |
Notlar |
End mill | 3-4 5-6 8-10 12-14 16-18 20-25 32-36 40-50 |
1180-750 750-475 600-375 375-235 300-235 235-190 190-150 150-118 |
Manual Manual Manual 30-37.5 37.5-47.5 47.5-60 47.5-60 47.5-75 |
1) When the milling width and cutting depth are small, the feed amount is larger; Otherwise, take the small value 2) For milling cutters with three-sided edges, please refer to the same diameter disc milling cutter to select the cutting speed and feed 3) When the milling cutter is 2Cr13, the cutting amount can be adjusted according to the actual hardness of the material 4) When milling and cutting concentrated nitric acid resistant stainless steel, both n and f should be appropriately lowered. |
Disc milling cutter | 75 110 150 200 |
235-150 150-75 90-60 75-37.5 |
23.5 or manual 23.5 or manual 23.5 or manual 23.5 or manual |
– |