Yüksek basınçlı döküm nedir (HPDC)? Yüksek basınçlı döküm Ürünleri süreci nasıl çalışır??
Yüksek basınçlı döküm prosesinde, erimiş metal veya metal alaşımı kalıba yüksek hız ve yüksek basınçla enjekte edilir.
Yatay yüksek basınçlı döküm makineleri kalıbın tamamen kapalı olmasını sağlar. Uygulayabilecekleri sıkma kuvveti miktarına göre sınıflandırılırlar ve 550 ile 5700 ton.
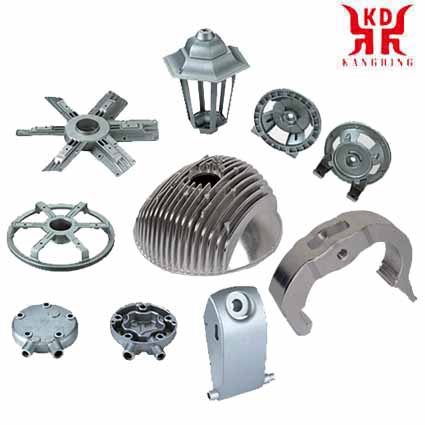
Manufacturing for Sie-Casting Products
Kullanılan metale bağlı olarak, Kalıbı dolduran enjeksiyon ünitesi sıcak oda veya soğuk oda olabilir. Sıcak kamaralı basınçlı dökümde, metal basınçlı döküm makinesinin içinde tutulur, daha sonra hazneye çekilir ve enjeksiyon pistonunun hareketi onu kalıba sokar. These parts of the machine are always in contact with molten metal.
Soğuk oda sürecinde, metal önce ayrı bir fırında eritilir ve bir bekletme fırınına aktarılır; daha sonra doldurma haznesine dökülür ve kalıba enjekte edilir. KANGDING offers a wide range of cold chamber high pressure casting machines.
Advantages of the high pressure casting process
High pressure casting technology can produce very large alloy parts in high volumes and at high speed.
These machines produce light alloy parts with great precision, superior surface finish, excellent uniformity and optimal mechanical properties.
The high-pressure casting process can also produce thin-walled components and cast parts together with different types of parts, such as screws and liners, which are then an integral part of the product itself.
Cold chamber die casting.
In the cold chamber process, the melting of the metal is carried out in furnaces outside the machine, and the injection chamber is at a temperature lower than that of the casting of the alloy.
In cold chamber injection molding, the molten material is fed from an external melting pot or furnace to the injection chamber (either manually or automatically), where a hydraulically operated plunger pushes it into the mold. Injection machines are equipped with hydraulic and pneumatic circuits, and controlled by automatons in such a way that they can be programmed to carry out the injection process autonomously.
Diagram of cold chamber injection phases.
The cycle speed is fast and high pressures are reached during the process. All castable metals and alloys, alüminyum, bakır, pirinç, magnezyum, çinko, vesaire. can be injected.
It is necessary to synchronize the filling of the chamber with the closing of the mold, so that when the mold closes, the injection can be carried out immediately, preventing the cycle from being delayed and also preventing the material from cooling down.
Vertical cold room. The compression chamber and the entire injection mechanism are arranged in a vertical position. At the initial moment, the lower piston covers the mold nozzle, while the working or upper piston is in its upper position. Sonraki, the upper piston, hydraulically actuated, moves downwards with a certain adjustable speed (injection speed), and when it comes into contact with the metal, the lower piston also begins to move downwards, uncovering the nozzle from the mold. . The upper piston continues its race until the metal completely fills the cavities of the mold including the funnel and the runners, leaving a portion of the metal in the chamber. Sonraki, both the upper piston and the lower piston rise to remove the excess solidified material.
![]() Casting of electronic equipment box |
![]() High Pressure Die Casting Service |
![]() Aluminum alloy castings |
There are two types of cold chamber machines:
Horizontal cold chamber The filling chamber is arranged in a horizontal position. The piston advances by closing the intake port and injecting the metal into the mold. The metal fills all the cavities and the piston remains in its forward position, maintaining pressure until complete solidification of the metal. When the two halves of the mold are opened, the piston continues to exert pressure on the solidified riser to help the part come out.
Başvuru
Cold-chamber high-pressure casting technology is ideal for the production of a diverse range of aluminum and magnesium parts for the automotive industry, such as engine blocks, gearbox crankcases, oil pans, engine mounts and structural parts. like the cross beams.
It is widely used in other industries to manufacture components for applications ranging from the simplest (a lighting component) to the most demanding (parts for an aerospace engine).
We have advanced machines and equipment, and our professional engineers use the latest CAD / KAM / CAE design software.
We provide molds in aluminum alloys, and cast zinc and aluminum alloys for connectors used in telecommunications, fiber optics, antennas and mobile devices. Die casting is ideal for multiple copies of hundreds or thousands of parts with a high quality surface finish, and we can also apply textures to your finished parts.
Choose us to manufacture your custom aluminum and zinc die castings. We stand out for precision and our cast ornaments weighing up to 11 kg. Our experience with machine tools is at the core of our commitment to becoming a world-class component supplier.
Molten Metals
Your choice of materials will depend on the cost, weight, and engineering used. Ask our experts for technical advice.
Die Cast Aluminum:
Ideal for strong and complex geometries, but light. The available alloys are ADC12, A380, ADC10 and A413.
Die Cast Zinc:
Used mostly for very ductile parts that may require galvanizing. Relatively simple cast. The available alloys are Zn 3 # and Zn 5 #.
Die Cast Magnesium:
For light parts that require a good strength / weight ratio. The alloy is AZ91D.
Döküm
We manufacture dies for die casting various parts and components used in automotive, medical and general industrial applications. For most of our production we use H13 steel with a Rockwell hardness of 42-48. Our customers can also choose other metals to create molds.
Yüzey
There are numerous finishing options available including sandblasting, water blasting, parlatma, galvanizing, tablo, lacquering, pad printing, screen printing, anodizing and factory finishing. We always recommend to our clients the best options for their design.
![]() LED ısı emici döküm |
![]() Die casting of transmission and gearbox housing |
![]() Die casting of communication equipment shell |