Yüksek basınçlı döküm nedir? Seri üretim basınçlı dökümlerin ürün maliyeti ve fiyatı
Yüksek Basınçlı Döküm (HPDC) seri veya seri üretime yönelik bir döküm işlemidir. Bunun için genellikle düşük erime noktasına sahip dökme alaşımlar kullanılır..
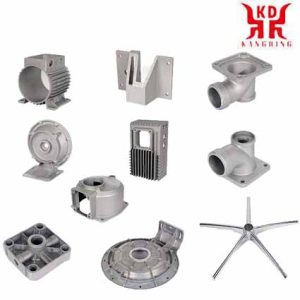
Çin Döküm
Basınçlı dökümde, sıvı eriyik bir basınçlı döküm kalıbına preslenir (döküm kalıbı, boşluk) yaklaşık yüksek basınç altında. 10 ile 200 MPa'ya kadar ve çok yüksek kalıp doldurma hızında 12 M / S, daha sonra katılaştığı yer. Basınçlı döküm işleminin özelliği, kalıcı bir kalıp kullanılmasıdır., yani. H. modeli olmayan. Sonuç olarak, kalıp bir dizi aynı bileşen için yalnızca bir kez üretilir, ancak önemli ölçüde daha yüksek bir üretim çabasıyla. Böylece, yüksek bir çıktı elde edilir, özellikle döküm kabının ve döküm pistonunun sürekli eriyik içinde olduğu sıcak odalı basınçlı döküm makinesinde. Daha yüksek erime noktasına sahip alaşımlar durumunda, soğuk oda basınçlı döküm prosesi kullanılır; döküm seti metalik eriyiğin dışında bulunur.
Yüksek basınçlı döküm prosesi nasıl çalışır??
Yüksek basınçlı döküm prosesinde, erimiş metal veya metal alaşımı kalıba yüksek hız ve yüksek basınçla enjekte edilir.
Yatay yüksek basınçlı döküm makineleri kalıbın tamamen kapalı olmasını sağlar. Uygulayabilecekleri sıkma kuvveti miktarına göre sınıflandırılırlar ve 550 ile 5700 ton.
Kullanılan metale bağlı olarak, Kalıbı dolduran enjeksiyon ünitesi sıcak oda veya soğuk oda olabilir. Sıcak kamaralı basınçlı dökümde, metal basınçlı döküm makinesinin içinde tutulur, daha sonra hazneye çekilir ve enjeksiyon pistonunun hareketi onu kalıba sokar. Makinenin bu parçaları her zaman erimiş metalle temas halindedir..
Soğuk oda sürecinde, metal önce ayrı bir fırında eritilir ve bir bekletme fırınına aktarılır; daha sonra doldurma haznesine dökülür ve kalıba enjekte edilir. geniş bir yelpazede soğuk kamaralı yüksek basınçlı döküm makineleri sunmaktadır.
Basınçlı döküm, plastik enjeksiyonlu kalıplamayla rekabet ediyor. Metalik malzemeler, bireysel durumlarda basınçlı döküm ürünleri pazarını güvence altına alan avantajlara sahiptir.
En sık kullanılan malzemeler şunlardır
Alüminyum (döküm alüminyum)
Çinko (döküm çinko)
Magnezyum (magnezyum döküm)
Silikon tombak
![]() Motor gövdesi döküm |
![]() Sokak lambası döküm |
![]() Dağıtım kutusu basınçlı döküm |
Döküm parçaların özellikleri
Döküm parçalar pürüzsüzdür, yüzeyleri ve kenarları temizleyin. Ek olarak, bu yöntem duvar kalınlıklarının diğer yöntemlere göre daha ince olmasını sağlar. çinko ile, Örneğin, parçalar duvar kalınlığına sahip olabilir 1 mm ve alüminyum ile 1.4 mm, istisnai durumlarda daha da az 1 mm.
Ulaşılabilir toleranslar ± 0.05 ± 0.15 mm, böylece kesin veya tamamlanmış bir dökümden bahsedilir. Büyük döküm parçalar için, Yine de, slightly larger tolerances are required.
It is possible to use parts made of other materials, örneğin. B. sockets, threaded bolts or pins to be poured in. Internal threads are produced directly with rotatable steel cores, which can then be removed again later. In contrast to other processes, the casting is called “shot” here. It is possible to carry out up to 1000 shots per hour (depending on the size of the machine). Depending on the casting material, the mold life is up to 2,000,000 shots (zinc alloys).
With aluminum, service lives of approx. 80,000 ile 200,000 shots are achieved. Uzun zamandır, die-cast aluminum was considered unsuitable for fusion welding and heat treatment. In the meantime, extensive investigations have made it possible to manufacture die-cast aluminum that is suitable for fusion welding and heat treatment. The particularly low-warpage beam welding processes (electron beam and laser beam welding) should be emphasized here – for optimum strength properties. Fakat, for optimal results it is necessary and advisable to consider the requirements of the process when designing. Ek olarak, Yine de, die-cast aluminum can also be welded very well using friction welding processes such as friction stir welding.
Die casting machine
Die casting machines usually consist of a mold clamping unit that is used to open and close the die casting mold. Components of the mold clamping unit (also called the closing part) are:
a fixed machine plate (also called a fixed plate) to hold the fixed casting mold half and, in the cold chamber process, the casting set
a movable machine plate (also mobile plate) to accommodate the hydraulic ejector and the movable mold half
the four guide pillars on which the movable machine platen is guided
the toggle lever system (consisting of a cylinder plate (also called crosshead), short and long lever and cross head)
the lock cylinder
The liquid metal is pressed from the casting chamber into the mold with a casting piston. Depending on the type of machine used, a distinction is made between the warm and cold chamber processes. The casting piston is driven by the casting unit’s drive. The drive piston is usually acted upon by a hydraulic pressure accumulator. In some cases the plunger is driven electrically.
Die casting machine peripherals
The peripheral units work in the vicinity of the die casting machine. These are process engineering devices that are necessary for the automatic process to run.
Mold spray machine or manipulator for mold spray or fixed nozzles
Heating and cooling devices
Extraction devices
Dosing oven or ladle
Vacuum-assisted die casting process
The vacuum-assisted die-casting process with forced ventilation enables workpieces with little or no gas inclusions. The cavity and the filling chamber are evacuated at the start of casting, so that the air contained therein and the gases produced are sucked out during casting and so fewer or no air inclusions can form in the melt.
Die casting recompression
A similar effect is achieved here by high compression in the phase before the final solidification of the workpiece. Pores and air pockets are significantly reduced.
As during the solidification of the melt. h there is a jump in volume during the transition from liquid to solid, volume deficits inevitably occur in the interior of thick-walled components.
In order to compensate for this effect of liquid shrinkage, the so-called squeeze process can be used to compress the solidifying melt. For this purpose, the pulpy melt is compressed by means of a “squeeze pin” in the die casting mold in areas where a volume deficit is expected.
Die casting mold and tool
The die-casting tools required in the die-casting process are manufactured in the tool shop or in the mold shop. Special materials or high-strength hot-work steels in accordance with DIN EN ISO 4957 are usually used as the material for the casting molds. A selection is shown in the following table.
Short material name | Material number |
32CrMoV 12-28 | 1.2365 |
X37CrMoV 5-1 | 1.2343 |
X40CrMoV 5-1 | 1.2344 |
Die casting phase sequence
Basınçlı dökümde, a pre-tempered (100 ile 300 santigrat derece) permanent mold (two or more parts) is filled with molten metal under pressure at high speed. The actual casting process can be divided into three phases.
The pre-filling phase is used to convey the melt in the casting chamber up to the gate. The air compressed in the sprue system during the first phase can escape through ventilation channels and through the molding plane due to the relatively low speed of the piston (0.05–0.7 m / S).
During the mold filling phase, the casting piston presses the melt into the mold at a very high speed (0.4–6 m / S). The mold filling time is extremely short at 5–60 ms. It is therefore practically impossible to vent the mold.
In the holding pressure phase at the end of the mold filling, a very high static final pressure is built up. The air trapped when the mold is filled is compressed and the cast part is replenished.
Casting pressure
Different casting materials each require a different casting pressure. Aluminum and magnesium alloys are cast at 300–1200 bar, zinc at 130–250 bar and brass at 300–1000 bar. The strength of a workpiece is greater at high casting pressure.
![]() Surface treatment of die castings |
![]() Radyatör kabuğunun dökümü |
![]() Die casting of meat grinder shell |
Shrinkage behavior of aluminum-silicon melts
If you pour liquid aluminum at about 700 ° C into a mold cavity in such a way that the mold is exactly filled, then the volume of the metal decreases to room temperature by a total of about 1.3% due to its contraction. Of this total, 0.05% is due to the liquid contraction, 0.75% to the solidification and 0.5% to the solid contraction.
This volume deficit of 1.3%, which is not much smaller with aluminum alloys than with pure metal, becomes noticeable in the solidifying cast part in the form of volume defects. In addition to normal shrinkage, these defects occur partly as sink marks, partly as macro-blowholes or as shrinkage pores.
The shrinkage cannot take place as unhindered in a die casting mold as it is in a sand casting mold, Örneğin. In foundry technology, the term “büzülme” means, in addition to a process, a measure, namely the percentage dimensional deviation of the cooled casting from the dimensions of the mold at operating temperature. Whether shrinkage can take place freely or with hindrance depends almost exclusively on the geometric shape of the cast part. It is therefore possible that the shrinkage rate of 0.5% that is generally used today can be used for many dimensions on one and the same cast part, while 0.4% could still be too much for other areas. The mold dimensions are to be determined taking into account a shrinkage drawing of the die-casting alloys concerned.
Shrinkage for die casting
Die-cast alloy | Shrinkage in% |
Aluminum alloys | 0,5–0,7 |
Magnesium alloys | 0,5–0,8 |
Zinc alloys | 0,4–0,6 |
Influence of the alloying elements in aluminum casting alloys
Silicon
yapı
With 12.5% silicon, aluminum forms a eutectic1 that melts at 577 ° C. In the binary system there is no connection between aluminum and silicon. The solubility of silicon in solid aluminum is 1.65% in equilibrium at 577 ° C., drops to 0.22% at 300 ° C. and even further at lower temperatures. If an alloy has more silicon than the solubility corresponds, the structure contains not only aluminum mixed crystals but also silicon crystals. If the cooling rate is not particularly fast, the silicon solidifies in the eutectic mixture in the form of angular crystals, needles and plates. These forms of training are made possible by small admixtures of z. B. sodium, strontium, antimony or phosphorus influenced. Die casting causes similar effects due to the rapid solidification.
Eutectic1 is a mixture of alloying elements, which of all possible compositions has the lowest melting point. The eutectic point, e.g. Örneğin .: an Al-Si alloy, is 12.5% Ve 577 ° C.
Casting properties
The higher the Si content, the more advantageous it has on the flow and mold filling capacity. The flowability deteriorates as the Si content decreases.
Influence of silicon on the feeding behavior
With an increasing Si content, over 11%, makro boşluk hacmi keskin bir şekilde artıyor. İnsidans hacmi makro boşluk hacmine ters yönde çalışır. Ondan daha az 9% Ve, kalın duvarlı parçalar emme boşluklarına sahip olma eğilimindedir. Basınçlı dökümde makro hava delikleri için besleme seçenekleri sınırlıdır (Kapıdan uzanan kalın duvarlı döküm parçalar bazı sorunlara yol açmaktadır, atış sırasında biriken malzeme en son doldurulup daha sonra katılaştığı için). Ötektik altı alaşımlarda, Emme noktalarından aşırı ısınma sonucu iri taneler fark edilir hale gelir.
Ötektik yakın bir erime (etrafında 11% Ve) daha güçlü makro boşluklara neden olur. Ötektik ve ötektik'e yakın Al-Si eriyor, "granüler" veya "rafine" bir yapıya yol açan, çevresel bir kabuk oluşumuyla katılaşır (dışsal katılaşma), böylece bu eriyikler emme deliklerine duyarlı olmaz.
ütü
Daha yüksek demir içeriğinin basınçlı döküm üzerinde olumlu etkisi vardır (Örneğin., alaşım EN AC-AlSi9Cu3 (Fe) maksimum. 1.2%), metalin kalıp yüzeyine yapışma eğilimini azalttığı için. Tolerans sınırları dahilinde, demirin normalde döküm özellikleri üzerinde hiçbir etkisi yoktur. Dökümhanede uygun olmayan ergitme veya çalışma yöntemlerinden kaynaklanan kasıtsız artış, döküm parçalarının gevrekleşmesine ve istenmeyen boşluk oluşumuna yol açabilir., sıcak çatlaklar veya çökme izleri. Düşük tutma ve dökme sıcaklıklarında, yerçekimi ayrışmaları sıklıkla meydana gelir, fırının tabanında toplananlar. Ayrışma ürünleri demirden oluşur, manganez ve silikon. Ayrışma ürünlerinin sertliği 500–1000 Vickers'tır.
bakır
Bakır katkı maddeleri katılaşma büzülmesini azaltır. Sonuç olarak, bakır içeren Al alaşımları basınca dayanıklı dökümlerin daha kolay yapılmasını sağlar. Cu katkı maddelerinin mukavemet ve işlenebilirlik üzerinde olumlu etkisi vardır. Bakır korozyon direncini azaltır.
manganez
%'nin onda birkaçı kadar manganez ilavesi, demirin uzama ve darbe direnci üzerindeki olumsuz etkisini azaltır. Fakat, Demir ve manganez daha yüksek bir içerikte mevcutsa, elverişsiz erime koşulları altında olabilirler, e.g. B. düşük tutma sıcaklıkları ile, sert ayrışmaya yol açar.
magnezyum
Eş zamanlı silikon varlığı ile, bakır veya çinko, Magnezyum sertliğin artması nedeniyle işlenebilirliğin iyileşmesine yol açar. Magnezyumun korozyon davranışı üzerinde olumsuz bir etkisi yoktur. Magnezyum otomotiv endüstrisinde de giderek daha ilgi çekici hale geliyor, özellikle daha düşük ağırlığı nedeniyle.
nikel
Nikel ilavesinin en önemli avantajı ısı direncinin artmasıdır.. Özellikle pistonlar ve silindir kafaları nikel içeren alüminyum alaşımlarının ana uygulama alanlarıdır.
çinko
Tolerans sınırları dahilindeki farklı çinko içeriğinin genellikle herhangi bir etkisi yoktur. Basınçlı dökümde, Sıcak çatlaklara eğilimli parçalarda magnezyum ile birlikte Zn içeriği zaman zaman azalır.
titanyum
Titanyum, Al alaşımlarına esas olarak tane inceltici olarak maksimuma kadar eklenir. 0.15%. Kum ve kokil kalıba döküm alaşımları durumunda, tane inceltici bir alaşım bileşenidir.
yol göstermek
Katı halde, kurşun ince damlacıklar halinde çözünmez. Tolerans sınırları dahilinde (<0.1%), Pb, alaşım özelliklerini belirgin şekilde etkilemez.
teneke
Birden fazla içeriğe sahip 0.02%, Kalay tane sınırları boyunca ayrılır ve normal toleransın aşılması durumunda sıcak çatlama davranışı üzerinde çok olumsuz bir etkiye sahiptir. – özellikle dökümde.
Comparison of die casting and injection molding
The investment costs for casting machines and the high manufacturing costs for the mold are roughly comparable. In both processes, large numbers of pieces have to justify these high investment costs. After that, the raw material costs have priority.
Die-cast metal components have a significantly higher flexural strength (rigidity) than injection-molded ones; it can be up to 20 times higher. The workpieces produced in die casting can still be subjected to loads at higher temperatures (aluminum up to approx. 450 ° C). In the case of injection-molded materials, the strength and rigidity decrease sharply at higher temperatures (from 100 ° C); the only exceptions are expensive special plastics. Another advantage is that when the components (with the exception of zinc) are stressed, there is no creep, birçok enjeksiyonla kalıplanmış iş parçasında olduğu gibi. Döküm parçalar çok daha iyi bir yapısal stabiliteye sahiptir, yani. mekanik olarak işlenmiş bir yüzey bir yüzey olarak kalır, plastik parçanın yüzeyi çok daha kolay deforme olur. Üstelik, Bazı enjeksiyonla kalıplanmış plastikler iklim koşulları altında şekil değiştirir. Döküm malzemeler elektromanyetik korumaya sahiptir ve organik çözeltilere dayanıklıdır. Ek olarak, kalite kaybı olmadan geri dönüşüm mümkündür.
Standart malzemeler kullanılırsa enjeksiyonla kalıplanmış bileşenler daha ucuzdur. Ek olarak, enjeksiyon kalıplama için renk kullanılabilir. Diğer bir avantaj ise döküm iş parçalarına kıyasla daha düşük ağırlıktır. İkincisi ayrıca daha zayıf korozyon özelliklerine sahiptir. Üstelik, basınçlı döküm metal bileşenlerin üretimi daha karmaşıktır ve “karmaşık” geometriler bazen mümkün değildir.