İşleme merkezi tezgahında birden fazla takım kullanılması, karmaşık bir çubuk iş parçasının beş veya altı tarafının tamamını işleyebilir. Aktarım verimliliği, ek tahrik araçlarına sahip torna tezgahlarından önemli ölçüde daha yüksektir. 5-Çubuk stoğunun eksenli frezelenmesi, çok küçük iş parçaları partilerinin işlenmesinde de ekonomiktir.
Uzun zamandır, hunting guns or sports guns were produced by traditional manual methods. The product is characterized by high quality and precision requirements, and each gun has its own characteristics, so it will inevitably form the characteristics of small batch production. In the past few years, machine gun parts were mass-produced annually, and now each order quantity is generally 100 ile 500 pieces. As the development cycle of new products is required to be shorter and shorter, and the inventory needs to be reduced in order to reduce costs, the future production batch is required to be 30 ile 200 pieces.
Figür 1. Machining center suitable for bar stock
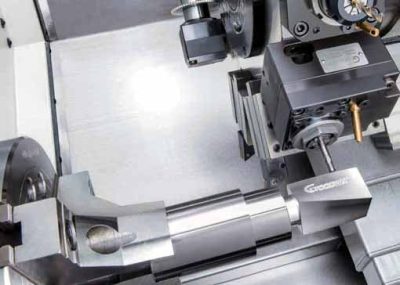
5-eksen çubuğu işleme merkezi
In order to rationalize the processing, a multi-station automatic machine tool with circular conveying or a multi-axis automatic lathe can be used. Fakat, due to the small production batch, the former is excluded due to the high cost of replacing tooling, and the latter due to the need to master new processing techniques.
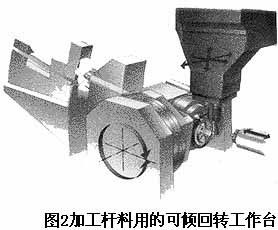
5-axis compound machining striker
The ideal solution is to use the MC530/SM machining center produced by Stama Machinery Plant (Şekil'e bakın 1). The spindle power of the machine tool is 21kW (70N•m), and the speed is 36~9000r/min. The spindle can automatically change tools, and can be loaded with tools up to 88mm in diameter, 250mm in length, and 12kg in weight (cutting to cutting time is 3.5s). The working range of its X, e, Z coordinates is 800mm×400mm×350mm, plus the A and B axis of the tiltable rotary table (Şekil'e bakın 2), the resolution is 0.001°, and pentahedral processing can be realized. The coordinates are all controlled by CNC, with interpolation function. Through the tiltable rotary table, it can pass through 800mm long rod material (diameter or diagonal size is 20-60mm). On the left side of the rotary table, there is a loading station for bars (bars and shaped rods). After manual loading, the material automatically moves until it hits the fixed stop installed on the spindle, and then it is clamped and fixed by a spring chuck. Can also be equipped with rod material library. It is connected with the loading station, so that the machine tool can automatically process for a long time. A reversible material handling manipulator can be installed on the workbench of the machine tool to realize six-sided processing. The long workpiece can be supported and clamped by the tailstock installed on the opposite side. The machine tool is equipped with an automatic tool changer magazine, and the headstock directly grabs the tools from the magazine (no other tool change mechanism). It can drill Ø40mm holes in St60 steel to process M27 threads, and the milling amount is 350cm3/min (600cm3/min when milling aluminum materials). The length of the adjusted tool is determined by the laser measuring device on the machine tool for wear detection. The auxiliary time of the machine tool is short, and the rapid feed rate can reach 40m/min. The positioning accuracy tolerance reaches P14, and the positioning dispersion Ps=10µm. Apply a special program to thermally compensate the machine tool.
The machining center can directly process 40mm×15mm bars into complete strikers. Its first processing plan is to compile a processing program with 20 knives and 38 steps. After processing, use a disc milling cutter (100mm, 125m/dak) to cut the workpiece initially, leaving a few millimeters margin. Nihayet, use a needle knife (Ø6mm, 4800r/min) to separate the workpiece (this can prevent the processed workpiece from breaking and falling off without control).
According to this process, the cutting time of each workpiece is th = 5.62min, the auxiliary time (machine adjustment time, vesaire.) totals 3.05min, and the x and y positioning time is 0.49min. Böylece, the total time for processing each workpiece is 9.16min, yani, the machine efficiency (under 80% load) is 5 pieces/h. In the two-shift system, there are 84 cases per working day.