“3 eksen arasındaki fark nedir?, 3+2 eksen, 4-eksen, ve genellikle bahsettiğimiz 5 eksen CNC işleme yöntemleri?”
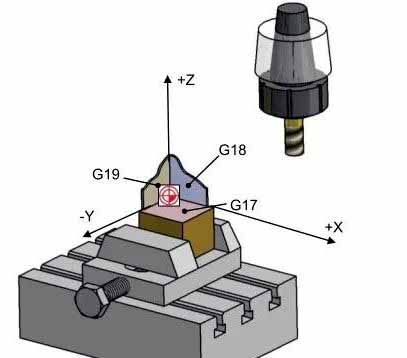
3-axis CNC machining method
3-axis CNC machining method
The 3-axis CNC machining is processed by linear feed axes X, e, ve Z. İşleme özellikleri: The direction of the cutting tool remains unchanged during the movement along the entire cutting path. The cutting state of the tool tip cannot be perfect in real time.
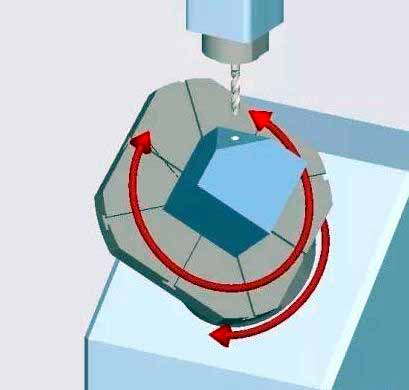
3+2 eksen işleme yöntemi
3+2 eksen işleme yöntemi
The two rotating axes fix the cutting tool in an inclined position first, and then perform processing by the feed axes X, e, ve Z. This kind of machine tool is also called positioning 5-axis machine tool. The CYCLE800 function of Siemens can be used for programming processing. CYCLE800 is a static plane transformation, which can define the rotating work plane in space by 3+2 eksen işleme (such as rotary head or rotary table). In this work plane, 2D or 3D CNC machining operations can be programmed.
Processing features of 3+2 eksen: The rotary axis always rotates to the position where the machining plane is perpendicular to the tool axis for machining, and the machining plane remains fixed during machining.
4-eksen işleme: Genel olarak, when the workpiece is not positioned in space, there are six degrees of freedom processing range, three linear displacement degrees of freedom of X, e, Z and three degrees of freedom of rotation displacement corresponding to the machined parts A, B, C .
The characteristics of 4-axis machining: Genel olarak, the parts machining center corresponding to the 4th axis pair is used in the index-controlled machine tool. And add a rotation axis to the general machining center.
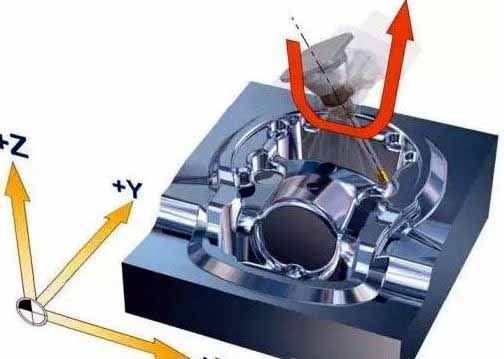
5-eksen işleme yöntemi
5-eksen işleme yöntemi
5-axis machining consists of linear interpolation movement of feed axes X, e, Z and any 5 axes of X, e, Z rotation axes A, B, ve C. Siemens’ motion conversion instruction TRAORI can well support 5-axis conversion.
Features of 5-axis machining: The tool direction can be optimized during the movement along the entire stroke, and the tool can be moved linearly at the same time. Böylece, the optimal milling state can be maintained on the entire path.