செயலாக்க கூறுகளை திருப்புவதில் (அலுமினியம், துருப்பிடிக்காத எஃகு, செம்பு, டைட்டானியம், கலவை), குறிப்பாக முடிக்க, ஒரு கருவியை எவ்வாறு தேர்வு செய்வது? CNC மாஸ்டர்களின் அனுபவத்தின் சுருக்கம்:
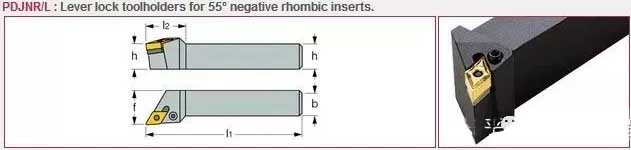
Turning finishing tool
1. முதலில், கருவியின் நுழைவு கோணத்தை தீர்மானிக்கவும்
Among the entering angles of conventional tools, those suitable for finishing are generally between 90° and 95°, especially 91°, 93°, and 95°. The approaching angle of 90° makes the cutting force follow the axis of the workpiece. No vertical force is applied to the workpiece to avoid vibration and deformation (thin-walled parts processing is especially important). Partial primary entry angle is generally assured on the arbor.
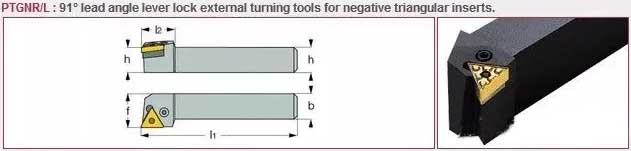
Set the tool tip angle for fine turning
2. இரண்டாவதாக, determine the angle of the tool tip, or choose the shape of the tool
பொதுவாக, the commonly used blade forms are: Round blade (start with R, ISO standard code, the same below); 90 degree square blade (beginning with S); 80 diamond blade (beginning with C); 80 degree convex triangle blade (beginning with W); 60 degree triangular blade (starting with T); 55 degree diamond blade (beginning with D); 35 degree diamond blade (beginning with V). These tool shapes basically cover more than 90% of conventional turning inserts. These types of blades are arranged in terms of tool strength: R, S, சி (டபிள்யூ), D, வி. R blade has the highest strength and V has the lowest. But the higher the strength, the greater the resistance and the greater the risk of vibration. எனவே, we often choose R, S, சி (டபிள்யூ) for roughing. For finishing, we will choose D and V. The profiling ability required for finishing is also V the best and R the worst.
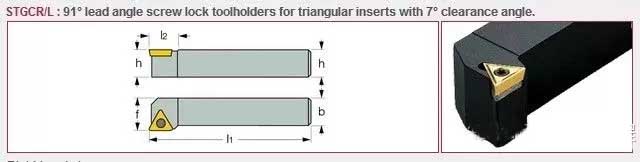
Set the rake angle and back angle of the finishing turning tool
3. Determine the front and rear corners of the tool
The negative rake angle tool has good rigidity and is not easy to chip, suitable for rough machining;
The positive rake angle blade cuts briskly and is more suitable for finishing. There is a matching relationship between the rear angle and the rake angle. பொதுவாக, the negative rake angle blades are basically 0 டிகிரி. The positive rake angle inserts have 5° (பி, ISO code, the same below), 7° (சி), 11° (P) of three commonly used tool clearance angles (only refers to turning).
Common combinations:
CC/CP (C-type positive rake angle blade 7°/11° rear angle);
DC (D type positive rake angle blade 7°rear angle);
VC/VB (V-type positive rake angle blade 7°/5°rear angle);,
WB/WC (W type positive rake angle blade 5°/7° clearance angle). These combinations are also the blade shapes used in conventional finishing (the front and rear corners are determined)
Combining the three, the tool form for conventional finishing is as follows:
95° entering angle arbor + CC insert
93° entering angle arbor + WB/WC/DC/VC/VB insert
91° entering angle arbor + DC/VC/VB insert
அவர்களில், the 93° entering angle toolholder + DC is the best finishing plan recommended by my individual (only in terms of turning radial). This program is equipped with suitable cutting parameters, and the processing effect should be one of the best in turning currently. I tried this 1.6 roughness on several different materials (துருப்பிடிக்காத எஃகு, டைட்டானியம், அலுமினியம்). தி 0.8 roughness of another steel part is because of the inner hole, and the diameter of the shank is limited, and only 95° entering angle shank + CC blade can be used.
நிச்சயமாக, the above options are not unique. Under the working conditions where large diameter solid materials can reach high linear velocity. Turning inserts with 0° clearance angle (ISO code N) can also be turned with better roughness. But the roughness at this time is more “grinded” by thick alumina CVD coated blades at high linear speeds. This roughness is basically about one grade different from the roughness processed by the tool selected above. வேறு வார்த்தைகளில் கூறுவதானால், the CN blade can be used for precision turning to 1.6, and the DC blade can be used for precision turning to 0.8.
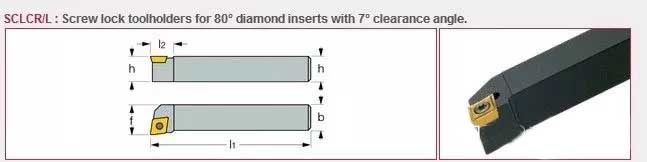
Commonly used inserts for fine turning inner holes
supplement:
Commonly used inserts in inner hole precision turning include TC/TP (T-type positive rake angle insert 7° / 11° rear angle)
Corresponding toolholder combination
91° entering angle arbor + TC / TP insert
For precision turning with an inner hole diameter of more than 16, DC blades can basically be used. எனினும், there are two types of DC blades, 07 மற்றும் 11. தி 07 blade can process 16-20 internal holes, and the DC11 blade can be used for 25 and above.
For precision turning with an inner hole of about 10-16, CC blades or TC / TP blades can be used.
If the inner hole is smaller than 10mm, generally only CC blades are more suitable. Japanese CC blades can achieve 5.5-6 மிமீ.
image:
1: Outer diameter precision turning
1. PDJNR
This kind of tool holder is suitable for fine turning of medium and large diameter workpieces. The improved toolholder can not only turn the outer diameter and end face, but also profile turning parts. It is widely used in fine turning. And the machining shaft pin workpiece and the center do not interfere.
2. PTGNR
Suitable for fine turning of medium and large diameter parts. Note that this type of toolholder can only turn the outer diameter, and is not suitable for turning outer diameter + end face.
3. STGCR and SCLCR
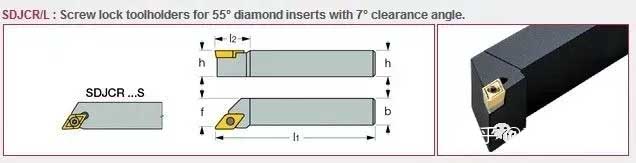
PDJNR toolholder is suitable for fine turning of medium and large diameter workpieces
It is suitable for fine turning of medium and small parts, but SCLCR is used for turning fine shafts, and STGCR is not suitable for turning end faces.
4. “The best partner” is here, SDJCR
It is suitable for fine turning of all outer diameter parts, including profiling and shaft pin parts. It is suitable regardless of the diameter. மேலும், it cuts lightly and is more resistant to chipping than VB / VC inserts.
2: Inner hole fine turning
1.PDUNR
Similar to the outer diameter, the shank is suitable for fine turning of medium and large diameter parts, and can also be profiled and end faces.
2.PTFNR
Suitable for fine turning of medium and large parts.
3.SCLCR
One of the commonly used inner hole precision turning toolholders, with a wide machining diameter range, the smallest can be about 5.5-6.
4.STFPR
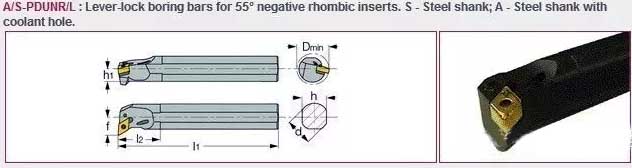
PTGNR turning tool turning workpiece outer diameter
One of the commonly used tool holders for small and medium-aperture precision turning. பொதுவாக, the machining hole diameter is not more than 20-25, and the minimum is about 8-10. The cutting is lighter than SCLCR, and the number of blades is half that of CC, which is economical.
5.SDUCR
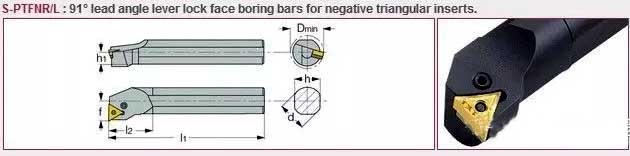
STGCR and SCLCR turning tools for turning small parts
Due to the limitation of the shape of the turning blade, the minimum machining diameter of this turning toolholder is about 14-16, so it is not as widely used as the above two toolholders. எனினும், because the turning tool has a smaller tip angle than the previous two models, the cutting is lighter and can be profiled.
Well, the five types of tools inside and outside can basically meet the conventional outer diameter and inner diameter finishing.
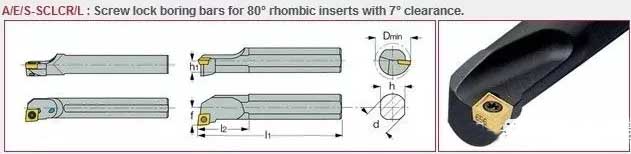
SDJCR turning tool is used for turning profiling and shaft parts
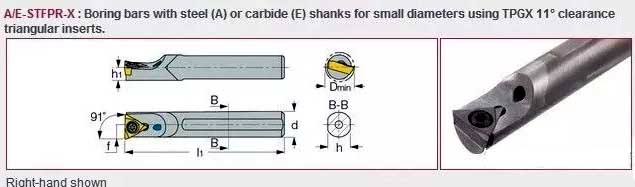
SDUCR insert for turning inner hole