Reaming is to use a reaming drill to further process the drilled hole to enlarge the hole diameter and improve the accuracy and reduce the surface roughness value. The dimensional tolerance grades that can be achieved for reaming are IT11~IT10. The surface roughness value is Ra12.5~6.3μm. It belongs to the semi-finishing machining method of holes, which is often used as pre-processing before reaming, and can also be used as the final processing of holes with low precision.
Broschningsmetoden visas i figuren 7-4, och brotschningsbidraget (D-d) kan konsulteras i tabellen. Formen på brotschen varierar med diametern. Diametern på Φ10~Φ32 är en brotsch med koniska skaft, som visas i figur 7-5a. Diametern på Φ25~Φ80 är en brotschborr av hylstyp, som visas i figur 7-5b.
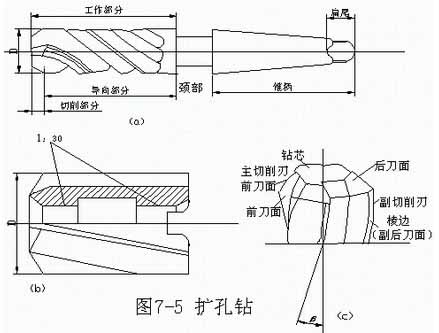
The structure of the reamer
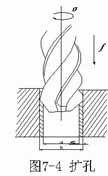
Method of reaming
Compared with the twist drill, the structure of the reamer drill has the following characteristics:
1. Good rigidity. Due to the small cutting amount of the reaming hole and less chips, the chip pockets of the reaming drill are shallow and narrow, and the drill core diameter is larger, which increases the rigidity of the working part of the reaming drill.
2. Good orientation. The reaming drill has 3 till 4 tänder, the number of edges around the tool is increased, and the guiding effect is relatively enhanced.
3. The chip condition is better. The reamer has no chisel edge to participate in the cutting, and the cutting is brisk. Larger feed rate can be used, higher productivity;
Också, due to less chips, chip removal is smooth, and the machined surface is not easily scratched.
Därför, compared with drilling, reaming has higher machining accuracy, lower surface roughness value, and can correct the axis error of drilling to a certain extent. Dessutom, the machine tool suitable for reaming is the same as for drilling.