Vad är högtrycksgjutning? Produktkostnad och pris för masstillverkade pressgjutgods
Högtrycksgjutning (HPDC) är en gjutprocess för serie- eller massproduktion. För detta används vanligtvis gjutna legeringar med låg smältpunkt.
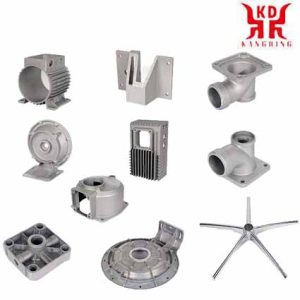
Kina formgjutning
I formgjutning, den flytande smältan pressas in i en pressgjutform (gjutform, hålighet) under högt tryck på ca. 10 till 200 MPa och vid en mycket hög formfyllningshastighet på upp till 12 m / s, där det sedan stelnar. Det speciella med pressgjutningsprocessen är den med en permanent form, dvs. H. utan modell. Som ett resultat, formen tillverkas endast en gång för en serie identiska komponenter, men med en betydligt högre produktionsinsats. På det här sättet, en hög effekt uppnås, speciellt i en varmkammarpressgjutmaskin där gjutbehållaren och gjutkolven ständigt är i smältan. När det gäller legeringar med högre smältpunkt, kallkammartryckgjutningsprocessen används; gjutsatsen är placerad utanför den metalliska smältan.
Hur fungerar högtrycksgjutningsprocessen?
I högtrycksgjutningsprocessen, smält metall eller metallegering sprutas in i formen med hög hastighet och högt tryck.
Horisontella högtrycksgjutmaskiner säkerställer att formen är helt stängd. De klassificeras efter hur mycket spännkraft de kan applicera och kan variera från 550 till 5700 ton.
Beroende på vilken metall som används, injektionsenheten som fyller formen kan vara antingen en varmkammare eller en kallkammare. Pressgjutning i varm kammare, metallen hålls i själva pressgjutmaskinen, sedan dras den in i kammaren och insprutningskolvens verkan inför den i formen. Dessa delar av maskinen är alltid i kontakt med den smälta metallen.
I kylrumsprocessen, metallen smälts först i en separat ugn och överförs till en lagringsugn; sedan hälls den i en fyllningskammare och injiceras i formen. erbjuder ett brett utbud av högtrycksgjutmaskiner för kallkammar.
Pressgjutning konkurrerar med formsprutning med plast. Metalliska material har fördelar i enskilda fall som säkrar marknaden för pressgjutna artiklar.
De mest använda materialen är
Aluminium (pressgjuten aluminium)
Zink (pressgjuten zink)
Magnesium (pressgjuten magnesium)
Silikontombak
![]() Motorhus pressgjutning |
![]() Gatulampa pressgjutning |
![]() Fördelningslåda pressgjutning |
Formgjutna delars egenskaper
Pressgjutna delar har släta, rena ytor och kanter. Dessutom, denna metod gör att väggtjocklekar är tunnare än andra metoder. Med zink, till exempel, delarna kan ha en väggtjocklek på 1 mm och med aluminium av 1.4 mm, i undantagsfall ännu mindre än 1 mm.
De uppnåbara toleranserna är ± 0.05 till ± 0.15 mm, så att man talar om en exakt eller färdig gjutning. För stora gjutna delar, dock, lite större toleranser krävs.
It is possible to use parts made of other materials, Till exempel. B. sockets, threaded bolts or pins to be poured in. Internal threads are produced directly with rotatable steel cores, which can then be removed again later. In contrast to other processes, the casting is called “shot” here. It is possible to carry out up to 1000 shots per hour (depending on the size of the machine). Depending on the casting material, the mold life is up to 2,000,000 shots (zinc alloys).
With aluminum, service lives of approx. 80,000 till 200,000 shots are achieved. Under en lång tid, die-cast aluminum was considered unsuitable for fusion welding and heat treatment. In the meantime, extensive investigations have made it possible to manufacture die-cast aluminum that is suitable for fusion welding and heat treatment. The particularly low-warpage beam welding processes (electron beam and laser beam welding) should be emphasized here – for optimum strength properties. dock, for optimal results it is necessary and advisable to consider the requirements of the process when designing. Dessutom, dock, die-cast aluminum can also be welded very well using friction welding processes such as friction stir welding.
Die casting machine
Die casting machines usually consist of a mold clamping unit that is used to open and close the die casting mold. Components of the mold clamping unit (also called the closing part) are:
a fixed machine plate (also called a fixed plate) to hold the fixed casting mold half and, in the cold chamber process, the casting set
a movable machine plate (also mobile plate) to accommodate the hydraulic ejector and the movable mold half
the four guide pillars on which the movable machine platen is guided
vippspakssystemet (bestående av en cylinderplatta (även kallad crosshead), kort och lång spak och tvärhuvud)
låscylindern
Den flytande metallen pressas från gjutkammaren in i formen med en gjutkolv. Beroende på vilken typ av maskin som används, man skiljer på varm- och kallkammarprocesserna. Gjutkolven drivs av gjutenhetens drivning. Drivkolven påverkas vanligtvis av en hydraulisk tryckackumulator. I vissa fall drivs kolven elektriskt.
Pressgjutningsmaskin kringutrustning
De perifera enheterna arbetar i närheten av pressgjutningsmaskinen. Dessa är processtekniska enheter som är nödvändiga för att den automatiska processen ska köras.
Formspraymaskin eller manipulator för formspray eller fasta munstycken
Värme- och kylanordningar
Extraction devices
Dosing oven or ladle
Vacuum-assisted die casting process
The vacuum-assisted die-casting process with forced ventilation enables workpieces with little or no gas inclusions. The cavity and the filling chamber are evacuated at the start of casting, so that the air contained therein and the gases produced are sucked out during casting and so fewer or no air inclusions can form in the melt.
Die casting recompression
A similar effect is achieved here by high compression in the phase before the final solidification of the workpiece. Pores and air pockets are significantly reduced.
As during the solidification of the melt. h there is a jump in volume during the transition from liquid to solid, volume deficits inevitably occur in the interior of thick-walled components.
För att kompensera för denna effekt av vätskekrympning, den så kallade squeeze-processen kan användas för att komprimera den stelnande smältan. För det här syftet, den massaaktiga smältan komprimeras med hjälp av en "squeeze pin" i pressgjutformen i områden där ett volymunderskott förväntas.
Pressgjutningsform och verktyg
De pressgjutverktyg som krävs i pressgjutningsprocessen tillverkas i verktygsverkstaden eller i formverkstaden. Specialmaterial eller höghållfasta varmbearbetningsstål enligt DIN EN ISO 4957 används vanligtvis som material för gjutformarna. Ett urval visas i följande tabell.
Kort materialnamn | Materialnummer |
32CrMoV 12-28 | 1.2365 |
X37CrMoV 5-1 | 1.2343 |
X40CrMoV 5-1 | 1.2344 |
Formgjutningsfassekvens
I formgjutning, en förhärdad (100 till 300 grader Celsius) permanent mögel (två eller flera delar) fylls med smält metall under tryck vid hög hastighet. Själva gjutningsprocessen kan delas in i tre faser.
Förfyllningsfasen används för att transportera smältan i gjutkammaren upp till porten. Luften som komprimeras i inloppssystemet under den första fasen kan strömma ut genom ventilationskanaler och genom formplanet på grund av kolvens relativt låga hastighet (0.05–0,7 m / s).
Under formfyllningsfasen, gjutkolven pressar in smältan i formen med mycket hög hastighet (0.4–6 m / s). Formfyllningstiden är extremt kort, 5–60 ms. Det är därför praktiskt taget omöjligt att ventilera formen.
I hålltrycksfasen i slutet av formfyllningen, ett mycket högt statiskt sluttryck byggs upp. Luften som fångas när formen fylls komprimeras och den gjutna delen fylls på.
Gjuttryck
Olika gjutmaterial kräver vart och ett olika gjuttryck. Aluminium och magnesiumlegeringar gjuts vid 300–1200 bar, zink vid 130–250 bar och mässing vid 300–1000 bar. Styrkan hos ett arbetsstycke är större vid högt gjuttryck.
![]() Ytbehandling av pressgjutgods |
![]() Pressgjutning av kylarskal |
![]() Pressgjutning av köttkvarnsskal |
Krympbeteende hos smältor av aluminium och kisel
Om du häller flytande aluminium vid ca 700 ° C in i en formhålighet på ett sådant sätt att formen är exakt fylld, då minskar metallens volym till rumstemperatur med totalt ca 1.3% på grund av dess sammandragning. Av detta totalt, 0.05% beror på vätskekontraktionen, 0.75% till stelnandet och 0.5% till den fasta sammandragningen.
Detta volymunderskott på 1.3%, vilket inte är mycket mindre med aluminiumlegeringar än med ren metall, becomes noticeable in the solidifying cast part in the form of volume defects. In addition to normal shrinkage, these defects occur partly as sink marks, partly as macro-blowholes or as shrinkage pores.
The shrinkage cannot take place as unhindered in a die casting mold as it is in a sand casting mold, till exempel. In foundry technology, the term “shrinkage” means, in addition to a process, a measure, namely the percentage dimensional deviation of the cooled casting from the dimensions of the mold at operating temperature. Whether shrinkage can take place freely or with hindrance depends almost exclusively on the geometric shape of the cast part. It is therefore possible that the shrinkage rate of 0.5% that is generally used today can be used for many dimensions on one and the same cast part, while 0.4% kan fortfarande vara för mycket för andra områden. Formens dimensioner ska bestämmas med hänsyn till en krympritning av de berörda pressgjutlegeringarna.
Krympning för pressgjutning
Pressgjuten legering | krympning i % |
Aluminiumlegeringar | 0,5–0,7 |
Magnesiumlegeringar | 0,5–0,8 |
Zinklegeringar | 0,4–0,6 |
Inverkan av legeringselementen i aluminiumgjutlegeringar
Kisel
strukturera
Med 12.5% kisel, aluminium bildar ett eutektikum1 som smälter vid 577 °C. I det binära systemet finns ingen koppling mellan aluminium och kisel. Lösligheten av kisel i fast aluminium är 1.65% i jämvikt kl 577 °C., faller till 0.22% på 300 °C. och ännu längre vid lägre temperaturer. Om en legering har mer kisel än motsvarar lösligheten, strukturen innehåller inte bara aluminiumblandade kristaller utan även kiselkristaller. Om kylhastigheten inte är särskilt hög, the silicon solidifies in the eutectic mixture in the form of angular crystals, needles and plates. These forms of training are made possible by small admixtures of z. B. sodium, strontium, antimony or phosphorus influenced. Die casting causes similar effects due to the rapid solidification.
Eutectic1 is a mixture of alloying elements, which of all possible compositions has the lowest melting point. The eutectic point, t.ex. T.ex .: an Al-Si alloy, är 12.5% och 577 °C.
Casting properties
The higher the Si content, the more advantageous it has on the flow and mold filling capacity. The flowability deteriorates as the Si content decreases.
Influence of silicon on the feeding behavior
With an increasing Si content, över 11%, the macro-void volume increases sharply. The incidence volume runs in the opposite direction to the macro void volume. With less than 9% Och, thick-walled parts tend to have suction cavities. The feeding options for macro-blowholes are limited in die casting (thick-walled cast parts lying from the gate cause some problems, since accumulations of material during the shot are filled last and then solidify). In hypoeutectic alloys, coarse grain becomes noticeable as a result of overheating from suction points.
A near-eutectic melt (around 11% Och) causes stronger macro-voids. Eutectic and near-eutectic Al-Si melts, which lead to a “granular” or “refined” structure, solidify with the formation of a peripheral shell (exogenous solidification), so that these melts are not susceptible to sucking holes.
järn
A higher iron content has a positive effect on die casting (e.g., alloy EN AC-AlSi9Cu3 (Fe) max. 1.2%), as it reduces the tendency of the metal to stick to the mold surface. Within the tolerance limits, iron normally has no influence on the casting properties. Unintentional increase due to improper melting or working methods in the foundry can lead to embrittlement of the cast parts and undesired formation of cavities, hot cracks or sink marks. At low holding and pouring temperatures, gravity segregations often occur, which collect on the floor of the furnace. The segregation products consist of iron, manganese and silicon. The hardness of segregation products is 500–1000 Vickers.
koppar
Copper additives reduce the solidification shrinkage. Som ett resultat, copper-containing Al alloys permit pressure-tight castings more easily. Cu additives have a positive influence on strength and machinability. Copper reduces the corrosion resistance.
manganese
Manganese addition of a few tenths of a% reduces the negative influence of iron on elongation and impact resistance. dock, if iron and manganese occur in a higher content, they can under unfavorable melting conditions, t.ex. B. by low holding temperatures, lead to hard segregation.
magnesium
With the simultaneous presence of silicon, copper or zinc, magnesium leads to an improvement in machinability due to an increase in hardness. Magnesium has no negative influence on the corrosion behavior. Magnesium is also becoming more and more interesting in the automotive industry, especially because of its lower weight.
nickel
The most important advantage of the addition of nickel is the increase in heat resistance. Pistons and cylinder heads in particular are the main areas of application for nickel-containing aluminum alloys.
zink
Olika zinkhalter inom toleransgränserna är i allmänhet utan inverkan. I formgjutning, Zn-halten tillsammans med magnesium reduceras ibland i delar som är utsatta för heta sprickor.
titan
Titan tillsätts till Al-legeringar främst som spannmålsraffinör upp till max 0.15%. När det gäller sand och permanent formgjutningslegeringar, det är en kornförädlande legeringskomponent.
leda
I fast tillstånd, bly är olöst i form av fina droppar. Within the tolerance limits (<0.1%), Pb påverkar inte legeringsegenskaperna märkbart.
tenn
Med ett innehåll på mer än 0.02%, tenn separerar längs korngränserna och har en mycket negativ effekt på hetsprickningsbeteendet om den normala toleransen överskrids – speciellt inom pressgjutning.
Jämförelse av pressgjutning och formsprutning
Investeringskostnaderna för gjutmaskiner och de höga tillverkningskostnaderna för formen är i stort sett jämförbara. I båda processerna, ett stort antal stycken måste motivera dessa höga investeringskostnader. Efter det, råvarukostnaderna har prioritet.
Pressgjutna metallkomponenter har en betydligt högre böjhållfasthet (stelhet) än formsprutade; det kan vara upp till 20 gånger högre. Arbetsstyckena som produceras i pressgjutning kan fortfarande utsättas för belastningar vid högre temperaturer (aluminium upp till ca. 450 °C). När det gäller formsprutade material, styrkan och styvheten minskar kraftigt vid högre temperaturer (från 100 °C); de enda undantagen är dyra specialplaster. En annan fördel är att när komponenterna (med undantag för zink) är stressade, det finns inget kryp, som är fallet med många formsprutade arbetsstycken. Die-cast parts have a much better structural stability, dvs. a mechanically processed surface remains a surface, whereby the surface of a plastic part deforms much more easily. dessutom, some injection-molded plastics change shape under climatic conditions. Die-cast materials have electromagnetic shielding and are resistant to organic solutions. Dessutom, recycling is possible without any loss of quality.
Injection molded components are cheaper if standard materials are used. Dessutom, color can be used for injection molding. Another advantage is the lower weight compared to die-cast workpieces. The latter also have poorer corrosion properties. dessutom, the production of die-cast metal components is more complex and “complicated” geometries are sometimes not possible.