Kalibrering av verktyg för CNC-verktygsmaskiner är en viktig färdighet vid bearbetning. Noggrannheten i verktygsinställningen avgör detaljens bearbetningsnoggrannhet, och kalibreringsverktygets effektivitet påverkar direkt delens bearbetningseffektivitet. Verktygsinställning är mycket viktig för bearbetning av verktygsmaskiner.
Efter att CNC-svarven är påslagen, nollretur (referenspunkt) operation måste utföras. Syftet är att skapa en enhetlig referens för positionsmätning, kontrollera, och visning av CNC-svarven, det är, verktyget återgår till verktygsmaskinens ursprung. Verktygsmaskinens ursprung är vanligtvis vid verktygets maximala positiva slag, och dess position bestäms av verktygsmaskinens positionssensor. Efter att verktygsmaskinen återgår till noll, avståndet mellan verktygets position (verktygsspets) och maskinens ursprung är fast. Därför, för att underlätta verktygskalibrering och bearbetning, verktygsspetsens position efter maskinens nollretur kan betraktas som maskinens ursprung.
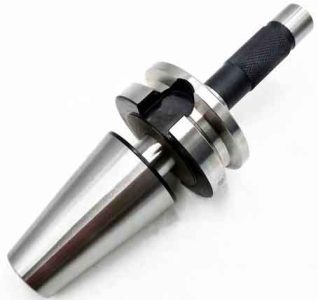
Verktygskalibreringsmetod för CNC-bearbetning
Kalibrering av verktyget är processen att upprätta arbetsstyckets koordinatsystem i maskinkoordinatsystemet för CNC-maskinverktyget, och att få ursprunget för arbetsstyckets koordinatsystem att sammanfalla med programmeringsursprunget. Mät avståndet mellan verktygsspetsens programmeringspunkt i verktygsmaskinens koordinatsystem och bearbetningsorigin i X- och Z-riktningarna med provskärning eller beröringsfria metoder, och ställ in värdet på maskinparametrarna. Genom programsamtalet, arbetsstyckets koordinatsystem upprättas. Det absoluta koordinatvärdet för baspunkten i programmet baseras på ursprunget för det etablerade arbetsstyckets koordinatsystem, och delens kontur bearbetas.
Det finns många sätt att kalibrera kniven på CNC-svarven, och provskärningsmetoden används ofta i arbetet. Följande introducerar FANUC-0Jag CNC-svarv vanligt förekommande kalibreringsverktygsmetod.
1. Mät och mata in verktygsoffsetmetod
1) Provskär arbetsstyckets yttre cirkel med det valda verktyget, och rikta in verktyget i X-riktningen. I manuellt driftläge, försök att skära den yttre cirkeln, håll X-riktningen oförändrad, och verktyget går ut längs Z-axeln. Använd en nockmätare för att mäta diametervärdet α för den avskurna yttre cirkeln, och klicka på “OFFSETNING” knappen för att gå in i gränssnittet för parameterinställning för formkompensation. Flytta markören till X-positionen för verktygskompensation, skriv in Xα, och klicka på programknappen [Mäta]. Det numeriska styrsystemet beräknar automatiskt koordinaterna för den aktuella verktygsspetsen i X-riktningen i verktygsmaskinens koordinatsystem, och X-riktningen slutför kalibreringen av verktyget.
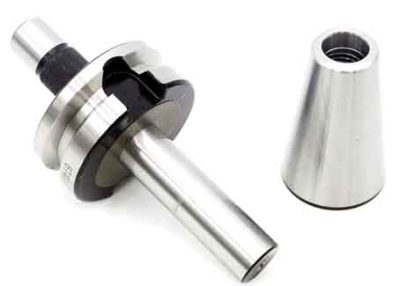
Kalibrering av verktygsmaskiner
2) Använd det valda verktyget för att skära ändytan och kalibrera verktyget i Z-riktning. I manuellt driftläge, verktyget skär ändytan av arbetsstycket till mitten. Då förblir Z-riktningen orörlig, och verktyget går ut i X-riktningen. Gå in i gränssnittet för parameterinställning för formkompensation, flytta markören till motsvarande position för verktygskompenseringens Z-koordinat, skriv in Z0, tryck på [Mäta] mjukknapp, motsvarande verktygsoffset matas in automatiskt, och verktygsinställningen är klar. Denna metod är att ställa in bearbetningsorigin i mitten av arbetsstyckets högra ände, vilket är en vanlig metod för allmänna axeldelar. Om det är en vänster-höger symmetrisk del, bearbetningsorigin måste ställas in i arbetsstyckets symmetriska mitt, mata sedan in Zβ, β är hälften av delens axiella längd.
Ange sedan värdet på verktygets nosbågaradie R och verktygspositionsnumret T enligt verktygets geometriska storlek och monteringsposition, till exempel:
För nr. 1 verktyg, radien för verktygsspetsbågen är R=0,8 mm, flytta markören till den position som motsvarar nr. 1 verktyg under R, knappa in 0.8, ange verktygspositionsnumret vid motsvarande position för T, och tryck “INPUT” att mata in, sedan kan den användas för bearbetning.
2. Z-riktnings kalibreringskniv efter att arbetsstycket har vridits runt
Efter att arbetsstycket har vänts, bearbetningen måste säkerställa detaljens totala längd efter bearbetning. Därför, kniven måste kalibreras två gånger. X-riktningen är densamma som den tidigare metoden för verktygsinställning. Stegen för verktygsinställning i Z-riktning är som följer:
Skär ändytan av arbetsstycket till mitten, håll Z-riktningen stilla, tryck på knappen X framåt, och verktyget går ut. Mät arbetsstyckets totala längd i Z-riktningen som Z1, den erforderliga totala längden på arbetsstycket är Z, och längdskillnaden är ∆=Z1-Z. Innan du kör programmet, Du måste först ställa in O-punkten som bearbetningsursprung (se figur 1), och gå in i parameterinställningsgränssnittet för formkompensation. Flytta markören till Z-koordinatpositionen, ange Z∆, (∆ är Z-koordinatvärdet för verktygsspetsens aktuella position i de nyskapade arbetsstyckeskoordinaterna), tryck på [Mäta] mjukknapp, och motsvarande verktygsoffset matas in automatiskt.
3. G92 ställer in arbetsstyckets koordinatsystem
1) Använd ett externt svarvverktyg för att först försöka vrida den yttre cirkeln. Efter att ha mätt diametern på den yttre cirkeln, verktyget dras tillbaka i Z-axelns positiva riktning, och spindeln stannar. Notera det absoluta koordinatvärdet X1 för verktyget i verktygsmaskinens koordinatsystem vid denna tidpunkt, och mät samtidigt den yttre cirkeldiametern D.
2) Skär ändytan mot mitten, X rör sig inte, och gå ut längs Z-riktningen. Skriv ner det absoluta koordinatvärdet Z1 för verktyget i verktygsmaskinens koordinatsystem vid denna tidpunkt;
3) Välj startpunkt. Startpunkten ska väljas utanför arbetsstycket. Om startpunkten är inställd på 50 mm i X-riktningen och 50 mm i Z-riktningen från mitten av den högra ändytan. Då är startpunktens position i maskinkoordinatsystemet X = X1-D+100,0 (diameter programmering), Z=Z1+50,0;
4) Justera verktyget för att nå punkten. Innan programmet körs med arbetsstyckets koordinatsystem inställt av G92, verktyget måste justeras till upp-punktsläget. Metoder enligt nedan:
Flytta först verktyget till positionen nära startpunkten i manuellt läge, och justera sedan förstoringen med handratten för att nå den exakta positionen;
5) Just nu, utgångspunkten för programmet måste vara: G92 X100.0 Z50.0
Beskrivning:
(1) Verktyget måste kalibreras innan denna instruktion utförs, och verktygsspetsen måste placeras i den startpunktsposition som krävs av programmet genom att justera verktygsmaskinen;
(2) Att utföra G92-kommandot kommer inte att orsaka någon rörelse av verktygsmaskinen. Låt bara systemet ersätta det gamla koordinatvärdet med det nya koordinatvärdet, därigenom etablera ett nytt koordinatsystem.
När du använder provskärningsmetoden för att verifiera verktyget, verifieringsverktygets fel kommer huvudsakligen från mätfelet efter provskärningen av arbetsstycket och felet som orsakas av den visuella inspektionen under operationen. De viktigaste åtgärderna för att minska verktygsinställningsfelet är: Attityden måste vara rigorös, operationen måste vara försiktig, och avläsningen måste vara korrekt; Vid bearbetning, överväg inverkan av verktygsmaskinens upprepade positioneringsnoggrannhet på verktygets inställningsnoggrannhet och inverkan av verktygsplaceringspunktens installationshöjd på verktygets inställningsnoggrannhet; Efter verktygsinställning, verktygskompensationsvärdet ska korrigeras enligt felet mellan den faktiska storleken på den del som bearbetas av verktyget och den programmerade storleken.
Numeriska styrsvarvar har en mängd olika styrsystem. Verktygskalibreringsmetoderna inkluderar manuell kalibrering, kalibrering av verktygsmaskinens externa kalibrator, och automatisk kalibrering. Manuell verktygsinställning antar läget för “provklippning-mätning-justering”, vilket är enkelt och ekonomiskt, tar lång tid i verktygsmaskinen, och har ett stort fel. Att använda kalibratorn för verktygsinställning kan automatiskt beräkna skillnaden mellan längden på varje kniv och standardkniven, och lagra det i systemet. Vid bearbetning av andra delar, endast standardkniven behövs, vilket i hög grad sparar arbetshjälptid. Dessutom, användningen av ett verktygsinställningsinstrument för verktygsinställning kan eliminera fel under mätning och avsevärt förbättra noggrannheten i verktygsinställningen. Automatisk verktygsinställning realiseras av verktygsspetsdetektionssystemet. Verktygsspetsen närmar sig beröringssensorn med en inställd hastighet. När spetsen på verktyget vidrör sensorn och skickar en signal, CNC-systemet registrerar omedelbart koordinatvärdet i det ögonblicket och korrigerar automatiskt verktygskompensationsvärdet. Även om principen för att mata in parametrar för externt verktygsinställningsinstrument och automatisk verktygsinställning liknar den för manuell verktygsinställning, principen och mätmetoden är olika, graden av automatisering är hög, och arbetseffektiviteten förbättras.
Varje verktygskalibreringsmetod har sina egna fördelar och nackdelar, och operatörer kan använda dem flexibelt efter deras faktiska behov. På det här sättet, hela verktygsinställningsarbetet är enkelt, och bearbetningskvaliteten kan säkerställas, och hjälptiden kan sparas mycket, och produktionseffektiviteten kan effektivt förbättras.