Det finns många anledningar till deformering av bearbetade aluminiumdelar, som är relaterade till aluminiummaterialet, delens form, och CNC-maskiner och utrustning. Det finns främst följande aspekter: tom inre stress, skärkraft, deformation orsakad av skärvärme, och deformation orsakad av klämkraft.
Processåtgärder för att minska behandlingsdeformation
1. Reduce the internal stress of the blank. Naturlig eller konstgjord åldrande och vibrationsbehandling kan delvis eliminera den inre stressen hos det tomma. Förbehandling är också en effektiv processmetod. För stora tomma ämnen, the deformation after processing is also large due to the large margin. If pre-milling the excess part of the large blank. It can not only reduce the processing deformation in the subsequent process, but also can release a part of the internal stress after pre-processing.
2. Improve the cutting ability of the tool and the material of the tool. Geometric parameters have an important influence on cutting force and cutting heat. Rätt val av verktyg är viktigt för att minska deformationen av delar.
1) Reasonably choose the geometric parameters of the milling tool.
① The rake angle: Under villkoret att upprätthålla styrkan hos bladet, Rake -vinkeln ska vara på lämpligt sätt större. Å ena sidan, det kan slipa skarpa skärkanter, och å andra sidan, det kan minska skärning av deformation, Gör chipborttagningen smidig, och sedan minska skärkraften och skärningstemperaturen. Använd aldrig negativa rake -vinkelverktyg.
② Relief angle: Storleken på lättnadsvinkeln har en direkt effekt på slitaget på flankytan och kvaliteten på den bearbetade ytan. Att skära tjocklek är ett viktigt tillstånd för att välja lindringsvinkeln. Under grov malning, På grund av den stora matningshastigheten, Tung skärbelastning och stor värmeproduktion, Goda värmeavledningsförhållanden för verktyget krävs. Därför, the clearance angle should be smaller. När du avslutar fräsning, the cutting edge is required to be sharp to reduce the friction between the flank face and the machined surface and reduce the elastic deformation. Därför, the relief angle should be larger.
③ Helix angle: För att göra fräsningen slät och minska fräskraften, Helixvinkeln bör väljas så stor som möjligt.
④ Entering angle: Appropriately reducing the entering angle can improve the heat dissipation conditions and reduce the average temperature of the processing area.
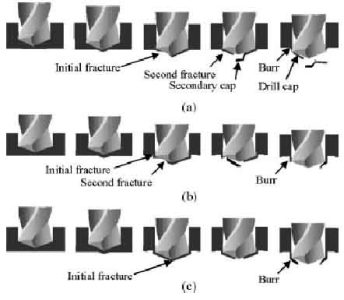
Method to prevent deformation of machined aluminum parts
2) Improve the milling tool structure.
① Reduce the number of milling cutter teeth and increase the chip space. På grund av den stora plasticiteten hos aluminiummaterial, stor skärningsdeformation under bearbetningen, och större utrymme för chipkapacitet krävs, Så den nedre radien för den chip-accepterande flöjten ska vara större och antalet malningständer bör vara mindre.
② Fine grinding of milling cutter teeth. The roughness value of the cutting edge of the tooth should be less than Ra=0.4um. Innan du använder en ny kniv, you should lightly grind the front and back of the teeth with a fine oil stone to eliminate the residual burrs and slight serrations when sharpening the teeth. På det här sättet, Skarningsvärmen kan inte bara reduceras, men också skärningsdeformationen är relativt liten.
③ Strictly control the wear standard of milling tools. Efter att verktyget har slitits, Ytråhetsvärdet för arbetsstycket ökar, skärtemperaturen stiger, och deformationen av arbetsstycket ökar. Därför, Förutom valet av verktygsmaterial med god slitmotstånd, Verktygslitarstandarden bör inte vara större än 0,2 mm, otherwise it is easy to produce built-up edge. Vid skärning, Arbetsstyckets temperatur bör i allmänhet inte överstiga 100 ° C för att förhindra deformation.
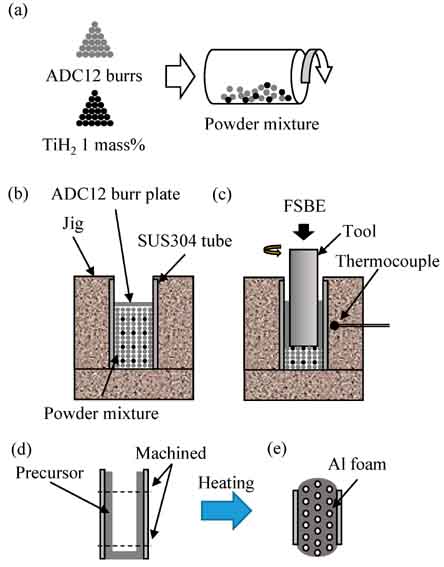
Filling method to prevent deformation of machined large aluminum parts
3. Förbättra klämmetoden för arbetsstycket. För tunnväggiga aluminiumarbetsstycken med dålig styvhet, Följande klämmetoder kan användas för att minska deformation:
① For thin-walled aluminum bushing parts. If a three-jaw self-centering chuck or spring chuck is used to clamp from the radial direction, När den släpps efter bearbetning, Arbetsstycket kommer oundvikligen att deformeras. Just nu, the clamping method of the axial end face with better rigidity should be used. För att hitta det inre hålet i delen, Gör en självgjord gängad genom Mandrel, ärm i det inre hålet i delen, Tryck på ändytan med en täckplatta och dra sedan åt den med en mutter. Klämdeformationen kan undvikas när den yttre cirkeln bearbetas, därmed erhålla tillfredsställande bearbetningsnoggrannhet.
② When processing thin-walled and thin-plate aluminum workpieces, Det är bäst att använda vakuumsugskoppar för att få jämnt fördelad klämkraft, and then process with a smaller cutting thickness (quantity), som väl kan förhindra deformation av arbetsstycket. Dessutom, an internal filling method can also be used. För att öka processstyvheten hos tunnväggiga arbetsstycken, Medium kan fyllas inuti arbetsstycket för att minska deformationen av arbetsstycket under klämma och skärning. Till exempel, Häll en urea -smälta som innehåller 3% till 6% kaliumnitrat i arbetsstycket. Efter bearbetning, immerse the workpiece in water or alcohol to dissolve the filling and pour it out.
4. Arrange the procedures reasonably. Under höghastighetsskärning, due to the large machining allowance and continuous cutting, Malningsprocessen producerar ofta vibrationer, som påverkar bearbetningsnoggrannheten och ytråheten.
Därför, the machining process of CNC high-speed cutting can generally be divided into: roughing – Semi-finishing – Clear corner processing – Finishing and other processes. För delar med hög precisionskrav, sometimes it is necessary to perform a second semi-finish machining and then finish machining. Efter grov bearbetning, Delarna kan kylas naturligt för att eliminera inre stress orsakade av grov bearbetning och minska deformation. Marginalen kvar efter grov bearbetning bör vara större än deformationsmängden, allmänt 1 till 2 mm. Under avslutning, Partsbehandlingsytan bör upprätthålla ett enhetligt bearbetningsbidrag, i allmänhet är 0,2-0,5 mm lämplig, så att verktyget är i ett stabilt tillstånd under bearbetningsprocessen. Det kan kraftigt minska skärning av deformation, få god ytbehandlingskvalitet, och säkerställa produktnoggrannhet.
In addition to the above-mentioned reasons, the operation method of aluminum parts is also very important in actual operation.