Den här artikeln introducerar flera CNC-svarvningstekniker för mycket specifika material: produkter inkluderar svarvning av mjukt gummi, svarvning av slipskivor, svarvning av hårdmetall, svarvning av keramik, svarvning av kompositmaterial. För olika material, välja olika verktygsmaterial, verktygets geometriska parametrar, styckningsmängd, och skärvätska.
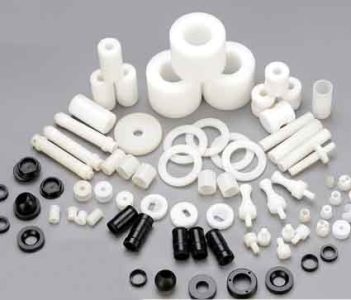
Svarvning av plastdelar
1. Svarvning av plastdelar:
The hardness (Shore A type 30~35) and strength (σb 20~25 MPa) of soft rubber are extremely low, Very poor thermal conductivity (0.14W/m/k), The plasticity is extremely high (δ=500~700), and the elastic modulus is extremely small (2~4 MPa). Because of the above properties, it has good elasticity, flexibility and variability, so it is difficult to cut it.
① Tool materials for turning soft rubber: high-speed steel, YG cemented carbide.
② The geometric parameters of the tool for turning soft rubber: γ0=45~55°, α0=10~15°, β0=20~30°; when scraping, γ0=0°, α0=70°, also use the cutter (β0= 5~10°), nesting knife.
③ Cutting rate for turning soft rubber: Vc≤100 m/min. αp=2~5mm; f=0.5~0.7 mm/r.
④ Cutting fluid for turning soft rubber: use an oil-free aqueous solution.
2. Turning of grinding wheel:
Allmänt, the hardness of corundum abrasives is 1800~2450HV, and the hardness of silicon carbide abrasives is 3100~3400HV. Using PCD and PCBN tools to turn these two abrasive wheels is as easy as cutting tofu with a knife.
① In order to prevent the grinding wheel from chipping during turning, a machine-clamped tool with a round blade is used.
② The geometrical parameters of the cutting tool for turning grinding wheel: circular blade γ0=-8~-10°, α0=8~10°.
③ Cutting rate of turning grinding wheel: Vc=30~50m/min. αp=4~5mm; f=1~1.5 mm/r.
3. Carbide turning:
“Cemented carbide has high hardness (HRA85-92.5, HV1300-1650, HRC67-81) and high brittleness (σb 900-2500 MPa). In the past, only grinding and electrical machining were used for processing. Due to the appearance of PCD and PCBN superhard tools, conditions are provided for turning processing.
① Tool materials for turning carbide: PCD, PCBN.
② Geometric parameters of cutting tools for turning cemented carbide: γ0=0~-5°, α0=6~8°, κr≤30~45°.
③ Cutting rate for turning cemented carbide: Vc=20~35m/min, αp=0.1~1.5mm, f=0.05~0.15 mm/r.
④ Note: To prevent edge chipping: use kerosene as cutting fluid.
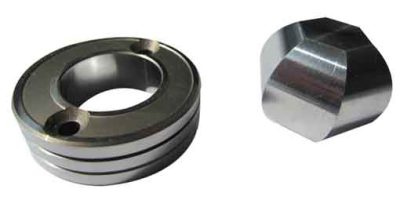
Turning of cemented carbide parts
4. Turning of engineering ceramics:
Traditional ceramics are ground with diamond wheels. This is because of its high hardness (1100~2250HV), low bending strength (450~1300MPa), and high elastic modulus (315000~400000MPa).
① Tool materials for turning ceramics: PCD, PCBN; easy-cutting ceramics, cemented carbide can also be used, but the tool durability is low.
② The geometric parameters of the tool for turning ceramics: γ0=-10~-15°, α0=8~12°, κr=30~60°. In order to make the cut-out and cut-in smoothly, a round blade can also be used.
③ Cutting amount of turning ceramics: Use cemented carbide tools to turn easy-to-cut ceramics Vc=10-20m/min. Use PCD and PCBN tools Vc=30~60m/min, αp=0.1~2mm; f=0.05~0.1 mm/r.
④ Cutting fluid for turning ceramics: Emulsion is used in one batch.
⑤ Pay attention to the problem of turning ceramics: prevent edge chipping.
5. Turning of composite materials:
Composite material is a solid material composed of multiple phases artificially made from two or more materials with different physical, kemisk, och mekaniska egenskaper. Till exempel, FRP is a typical composite material. The types of composite materials include glass fiber reinforced composite materials (GFRP), carbon fiber reinforced composite materials (CFRP), aramid fiber reinforced composite materials (KFRP), boron fiber reinforced composite materials, collectively referred to as resin-based fiber reinforced composite materials (FRP). It has only high specific strength and specific stiffness (3-8 times higher than metal), and has good fatigue resistance, shock absorption and fracture safety. And it is widely used in aerospace, aviation, chemical and other industries. During the cutting of composite materials, due to the low thermal conductivity of the material (less than 1/16 of that of ordinary steel), the cutting temperature is high, which is prone to deterioration and softening. The performance of fiber and resin is very different, the surface roughness is difficult to achieve, and the tool wear is serious, and cutting fluid cannot be used in most cases.
① Tool materials for turning composite materials: high-speed steel, coated high-speed steel, and YG cemented carbide. In order to increase the durability of tools by tens to hundreds of times, PCD and PCBN tools should be selected.
② Tool geometry parameters for turning composite materials: I allmänhet, γ0=-10~-15°, α0=10~12°, γε=1~3mm, to prevent chipping when threading γt=-15~-25°.
③ Cutting amount of turning composite materials: high-speed steel tool Vc=1O~15 m/min;
Carbide tool Vc=40~80m/min;
PCD and PCBN tools Vc=80~120m/min, f=0.2~0.5 mm/r, αp has no special requirements.
④ Note: In order to prevent delamination and tearing, protective measures should be taken (supporting the protective plate, reducing the cutting tool’s leading angle and feed, and chamfering at the cutting-in and cutting-out places, etc.).