Vid CNC-bearbetning, stor svarvbearbetning är en del av CMC-bearbetning. Denna del är mycket populär bland kunder, och även många regioner förlitar sig på denna teknik för att uppnå snabb ekonomisk utveckling. Vilka är fördelarna med storskalig svarvbearbetning, som kan locka så många människor att engagera sig i den här branschen?
Den främsta anledningen till att människor föredrar tekniken för storsvarvbearbetning är att det är lätt att säkerställa noggrannheten för varje bearbetningsyta på arbetsstycket. Detta motsvarar att garantera kvaliteten på arbetsstycket och ha en bättre grad av koordination i applikationen. Under bearbetning, arbetsstycket roterar runt en fast axel, och varje yta har samma rotationsaxel, så att koaxialitetskraven mellan bearbetningsytorna kan garanteras. Under skärprocessen, svarven är relativt stabil. under normala omständigheter, processen för svarvbearbetning är kontinuerlig, och det blir ingen påverkan, så det är stabilt.
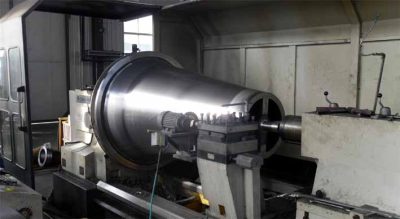
CNC-svarvning av stor svarv
Analys av processsvårigheter för smalt hål bearbetat av stor svarv
Stor svarvbearbetning är en relativt vanlig teknik, men denna teknik är inte lämplig för alla arbetsstycken. Bland dem, användningen av denna teknik för att bearbeta smala hål är ett svårt problem vid bearbetning av arbetsstycken. Tillverkaren kommer att analysera de största svårigheterna för dig i detalj.
Den exakta positioneringen av arbetsstycket är det första problemet man stöter på när man använder storsvarvbearbetningsteknik för att bearbeta smala hål. Anledningen till detta problem är att borrverktygets styvhet, storleken på den axiella bearbetningskraften, och fastspänningen och positioneringen av arbetsstycket kommer att påverka dess bearbetningsnoggrannhet. Med tanke på detta innehåll, speciella fixturer bör utformas enligt arbetsstyckets storlekskrav i kombination med specifik bearbetningsutrustning och processmetoder under konstruktion. Långskaftiga skärborrar lämpliga för vanliga svarvar är också ett av problemen, eftersom det är svårt att hitta lämpliga verktyg för ultradjupa hålsborrningar på marknaden, så det är nödvändigt att utforma lämpliga borrverktyg med långskaft i enlighet med arbetsstyckets storlekskrav.
Under vändningsprocessen, kylnings- och spånavlägsnande problem uppstår också. Under bearbetning, att säkerställa effektiv kylning av skärdelen och kontinuerlig utmatning av spån är nyckeln till bearbetningsprocessen. Den konventionella kylmetoden kan inte injiceras direkt i skärområdet, och effekten av kylning och spånavlägsnande är inte garanterad, så detta problem bör övervägas vid utformning av långskaftsborrverktyg.
Det sista problemet är parametrarna för skärprocessen. Arbetsstyckets rotationshastighet, verktygets matningshastighet, och skärvätskans flödestryck baseras på effekten av spånavlägsnande, och det är nödvändigt att överväga verktygets indragning och spånavlägsnande. Båda är viktiga processparametrar som måste övervägas noggrant och studeras.
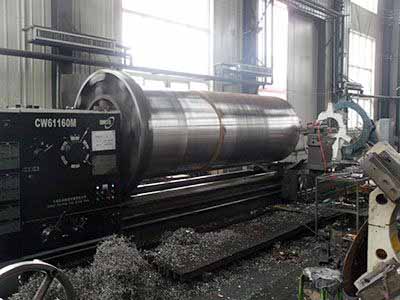
Svarvteknik av axeldelar
Vanliga CNC-bearbetningsmetoder för koniska ytor
För att bearbeta den koniska ytan, det är nödvändigt att säkerställa dimensionsnoggrannheten och konvinkeln, och det finns många vanliga bearbetningsmetoder. Stora svarvbearbetningstillverkare introducerar dig idag för flera vanligare metoder.
Metod 1: Vrid konen genom att rotera den lilla glidmetoden. Funktionen av denna metod är relativt enkel, men konvinkeln är i allmänhet bara exakt till en halv grad. På grund av begränsningen av den lilla glidplattans slaglängd, bearbetningen av för lång avsmalnande yta kan inte realiseras. I verklig drift, arbetaren försöker skära av delens koniska yta. Innan storleken inte uppfyller kraven, använd upprepade gånger en konpluggmätare eller ringmätare och andra mätverktyg för att testa konytan. Denna metod är tidskrävande och noggrannheten är inte särskilt hög.
Metod 2: Vridning av kon med offset tailstock-metod. Denna metod kan realisera automatisk matning och är lämplig för bearbetning av långa koniska ytor. dock, arbetsstycket begränsas av det övre stödet, och arbetsstycket med stor konvinkel kan inte bearbetas, och bearbetningsnoggrannheten är inte särskilt hög.