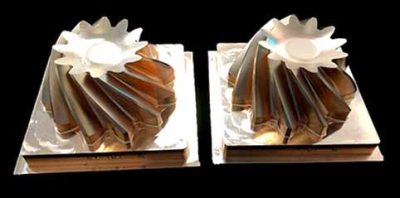
5-axelbearbetning av kopparyta
5-axelbearbetning av komplexa krökta delar (aluminiumlegering, rostfritt stål, koppar, titan, magnesium, koppar)
Flera delar av 5-axlig bearbetning av komplexa krökta delar: krökta ytor och vändskär genererade på CAD/CAM-programvara
Nästan alla komplexa krökta ytor bearbetas med höghastighetsfräsning i produktionen. Syftet är att förbättra produktionseffektiviteten, minska produktkostnaden, och samtidigt förbättra arbetsstyckets formnoggrannhet och minska ytjämnheten. För att möta behoven för höghastighetsfräsning, verktygsmaskinens spindel använder nästan utan undantag en elektrisk spindel. Spindelhastigheten är kontinuerligt variabel beroende på diametern på det använda verktyget, och hastighetsområdet är från flera tusen varv per minut till tiotusentals varv per minut. Drivsystemet på skjutbordet skiljer sig också från konventionella bearbetningscentra vid höghastighetsfräsning. Vanligt använda system inkluderar höghastighetsskruvmutterpar och linjärmotordrift, och den maximala matningshastigheten kan nå mer än 100m/min.
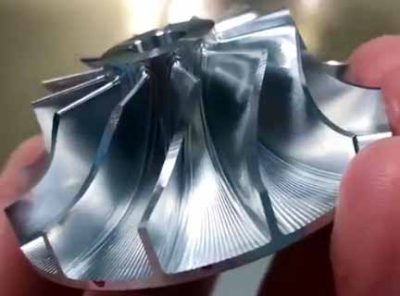
5-axelbearbetning av pumphjulets krökta yta
Vid bearbetning av komplexa krökta ytor, verktygsmaskinens CNC-system måste också uppfylla vissa speciella krav. Till exempel, NC-bearbetningsprogram för komplexa krökta ytor genereras vanligtvis på CAD/CAM-programvara. Ett program med krökt yta kräver ofta flera megabyte (Byte) av lagringsutrymme, och det är inte längre möjligt att överföra NC-programmet med en diskett. Därför, det numeriska styrsystemet måste ha funktionen att nätverka med andra datorsystem för att direkt ta emot numeriska styrprogram från CAD/CAM. Dessutom, det numeriska styrsystemet måste också anta avancerad styrteknik, för det första, det kräver blicken framåt (Se framåt) fungera. Med andra ord, innan verktygsmaskinen bearbetar ett visst spår, datasystemet analyserar ytan som ska bearbetas i förväg, beroende på krökningen av varje punkt på ytan och sambandsförhållandet mellan angränsande punkter. Justera verktygsmaskinens matningshastighet korrekt för att uppnå högsta produktivitet samtidigt som du säkerställer arbetsstyckets noggrannhet. För att minska det dynamiska felet i bearbetningsprocessen, den nya typen av datasystemservofelkorrigering använder inte längre den tidigare serieproportionella differentialintegralen (PID) regulator. Istället, den använder en tillståndsregulator som kompenserar för tillståndsparametrar som position och hastighet. Användningen av denna regulator kan helt eliminera drivfördröjningsfelet, kompensera för det olinjära felet som orsakas av gapet eller friktionen, och till och med kompensera vissa vibrationer i verktygsmaskinen. För att möta kraven på att förbättra arbetsstyckets formnoggrannhet och minska ytjämnheten.
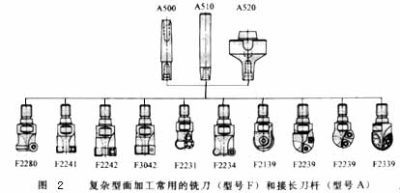
CNC fräs för bearbetning av krökta ytor
Verktygssystemet spelar en avgörande roll för produktionseffektiviteten och bearbetningskvaliteten vid bearbetning av komplexa krökta ytor. När du väljer ett skärverktygssystem, vi måste först utgå från geometrin hos de delar som ska bearbetas, och rimligtvis använda typerna av skärverktyg. När det gäller arbetsstycket som visas i figur 1, den geometriska variationen för varje del är mycket olika. Om endast en kuländfräs används för bearbetning, en kuländfräs med liten diameter måste väljas, vilket gör det svårt att förbättra bearbetningseffektiviteten. Dessutom, bågradien för vissa delar är så liten att den inte kan bearbetas även med en liten kuländfräs. Därför, med hänsyn till kraven på både produktionseffektivitet och arbetsstyckets form, andra typer av fräsar, såsom pinnfräsar och trefasfräsar, måste vara utrustad på det femaxliga bearbetningscentret för bearbetning av komplexa krökta ytor.
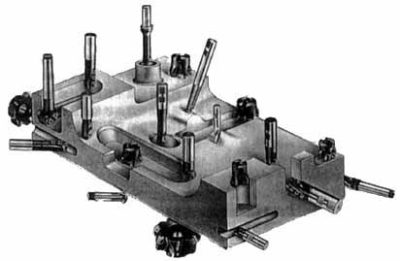
5-axelfräsning av olika ytor
Figur 2 visar några av de valda frästyperna. Så länge storleken tillåter, oavsett formen på fräsverktyget, skäret ska vara ett maskinklämt vändskär. Sådana knivar kan kombineras med blad och kroppar, och bladen och karosserna kan tillverkas av olika företag. Därför, en storskalig specialiserad produktion kan bildas, vilket inte bara bidrar till att förbättra kvaliteten på verktyget, men också bidrar till att minska produktionskostnaden för verktyget.
Verktygets livslängd är nära relaterad till matningen, skärhastighet och fräsdjup. Den optimala fräsmängden är ofta ett litet intervall, som bör bestämmas enligt det specifika verktyget och arbetsstyckets material.
Dessutom, skärstrategier som t.ex: Planering av verktygsvägar, verktygsaxelns yta normalvektor (ytans normala riktning vid denna punkt) eller längs yttangentvektorn (yttangensriktning vid denna punkt) är också en nyckelfaktor för bearbetning av komplexa ytor. Det påverkar inte bara ytråheten hos det bearbetade arbetsstycket, men påverkar också arbetsstyckets form och dimensionella noggrannhet. Figur 3 visar de olika skärstrategierna som används vid bearbetning av en cylindrisk krökt yta. För fräsning i omkretsriktningen, verktygsbanan måste interpoleras med tvåaxlig länk. Vid skärning längs generatrisriktningen, verktyget behöver bara utföra enaxelinterpolation. Dessutom, olika skärmetoder har stora skillnader i verktygsslitage: Verktygsslitaget vid nedfräsning är betydligt lägre än vid upp-nedfräsning, och slitaget under fram- och återgående fräsning är mycket större än vid enkelriktad fräsning.
För att förbättra stabiliteten i bearbetningsprocessen, kontinuiteten i skärningen måste säkerställas vid optimering av skärstrategin. På samma gång, minska skärrörelsen och tomgångsslaget så mycket som möjligt för att förkorta frästiden. Vid grovfräsning av ståldelar, det är nödvändigt att säkerställa kontinuerlig nedfräsning för att minimera skäreggens toppvärde under skärprocessen.
Vid bearbetning av arbetsstycket som visas i figur 4, om radskärnings- och frässpåret som visas i figur 5a används för bearbetning av skiljeväggar; Rörelsen av verktyget är mycket orimlig, skärförhållandena är mycket otillfredsställande, bearbetningstiden är 33min, och arbetsstyckets ytråhet är 6-9μm. Om cirkelskärspåret som visas i figur 5b används istället för bearbetning, handläggningstiden är ca 27 minuter, och arbetsstyckets grovhet kan också reduceras till 2 till 4 μm.