This article will introduce the turning technology of different materials (tool selection and parameter setting): Steel turning, stainless steel turning, duplex stainless steel turning, cast iron turning, heat-resistant super alloy (HRSA) sústruženie, aluminum turning, mild steel turning.
Steel turning
Steels can be classified into: unalloyed, low-alloy and high-alloy steels, all of which affect machining recommendations for turning.
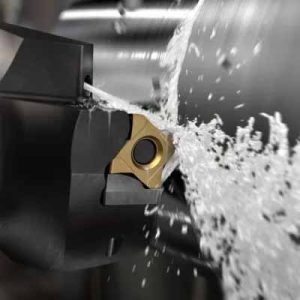
Turning steel technology
Turning of unalloyed steel
Material classification: P1.1
Non-alloy steel has a carbon content of up to 0.55%. Low carbon steels (carbon content <0.25%) require special attention because chip breaking is difficult and because of their tendency to clogging (built-in edge).
To break and direct the chip, aim for the largest possible feed. It is recommended to use a wiper insert.
Use high cutting speeds to avoid a built-in edge on the insert, which could adversely affect the surface. Sharp edges and light cutting geometry will reduce the tendency to pack and prevent edge deterioration.

Turning duplex stainless steel technology
Low Alloy Steel Turning
Material classification: P2.x
The ease of machining of low alloy steels depends on the alloy content and the heat treatment (hardness). For all materials in this group, the most common wear mechanisms are flange and crater wear. For hardened materials, plastic deformation is also a common wear mechanism due to the higher temperature in the cutting area.
In the case of unhardened low alloy steels, the first choice is the series of geometries and grades for steel. In hardened materials, it is beneficial to use a harder grade (liatina, ceramic and CBN grades).
High Alloy Steel Turning
Among the high alloy steels to carbon included, a total content exceeding 5% zliatina. This group includes both unhardened and hardened materials. Ease of machining is reduced the higher the alloy content and the higher the hardness.
For low alloy steels, the first choice is steel grades and geometries.
Steels with more than 5% alloying elements and a hardness greater than 450 HB have higher requirements for resistance to plastic deformation and edge strength. Consider using a harder grade (liatina, ceramic, and CBN grades).
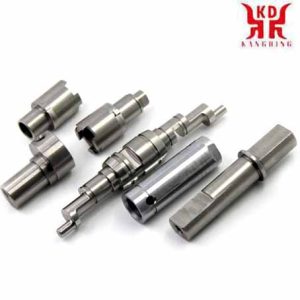
Turning cast iron technology
Stainless steel turning
Stainless steels can be classified as ferritic / martensitic, austenitic, and duplex (austenitic / ferritic) each with their specific machining recommendations for turning.
Turning of ferritic and martensitic stainless steels
Material classification: P5.1
This stainless steel is classified as a steel material, to jest, with a P5.x material classification. The general machining recommendations for this type of steels are our grades and geometries for stainless steel.
Martensitic steels can be machined under hardness conditions with higher requirements for resistance to plastic deformation of the insert. Consider using CBN grades, HRC = 55 and higher.
Austenitic Stainless Steel Turning
Material classification: M1.x and M2.x
Austenitic stainless steel is the most common type of stainless steel. This group also includes super-austenitic stainless steels, defined as stainless steels with a Ni content greater than 20%.
The recommended grades and geometries are our offer of CVD and PVD grades for stainless steel.
For intermittent cuts or where hammering or chip jamming is the main wear mechanism, use PVD grades.
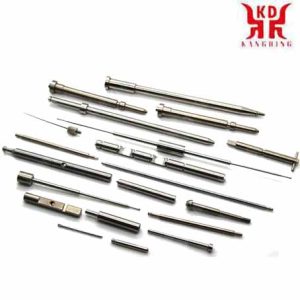
Turning heat-resistant super alloy (HRSA) technology
Other considerations:
Always use coolant to reduce crater wear and plastic deformation and select the largest possible nose radius. Read more about refrigerant
Use round inserts or reduced lead angles to prevent notch wear.
The tendency for the cutting edge or the filler edge to become pregnant is common. Both adversely affect surface finish and service life. Use sharp edges and / or geometries with a positive rake angle facet.
Duplex Stainless Steel Turning (Austenitic / Ferritic)
Material classification: M3.4
For duplex steels with a higher alloy, names such as super-duplex or even hyper-duplex stainless steels are used. Their higher mechanical strength makes these materials more difficult to machine, especially with regard to heat generation, cutting forces and chip control.
The recommended grades and geometries are our offer of CVD and PVD grades for stainless steel.
Other considerations:
Use coolant to improve chip control and prevent plastic deformation. Use tools with internal coolant supply, preferably precision ones.
Use small entry angles to avoid notch wear and burr formation.
Cast iron turning
There are five main types of cast iron:
Gray cast iron (GCI)
Nodular cast iron (NCI)
Malleable cast iron (MCI)
Compact Graphite Cast Iron (CGI)
Austempered Ductile Iron (ADI)
The function is an Fe-C composition with Si (1-3%) and C content greater than 2%. It is a short chip material with good chip control under most conditions.
For most cast materials, it is recommended to use our cast grades and geometries. The use of ceramic and CBN grades is recommended for nodular cast iron at higher cutting speeds.
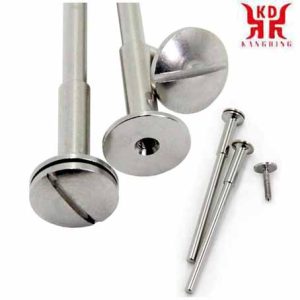
Turned stainless steel medical components
Turning Heat Resistant Super Alloys (HRSA)
A heat-resistant superalloy is an alloy that exhibits excellent creep and mechanical strength (the tendency of solids to slowly yield or deform under stress) at elevated temperatures. It also offers good resistance to corrosion / oxidácia. HRSAs can be divided into four groups of materials:
Nickel-based (napríklad, Inconel)
With iron base
Cobalt-based
Titanium alloys (titanium can be pure or incorporate alpha or beta structures)
The ease of machining both HRSA and titanium is poor, especially under aging conditions, imposing particular demands on cutting tools. It is important to use sharp edges to avoid the formation of so-called white layers, with different hardness and residual stresses.
HRSA material: PVD and ceramic grades are often used for turning HRSA materials. It is recommended to use HRSA optimized geometries.
Titanium alloys: mainly use uncoated and PVD grades. It is recommended to use optimized geometries for HRSA.
A common wear criterion for both titanium and HRSAs is notch wear. Follow these guidelines for optimal performance:
It is recommended to use a position angle of less than 45 °.
Use the correct ratio of insert diameter / nose radius to depth of cut.
When using ramping or multi-pass machining, it is recommended to use a depth of cut greater than 0.25 mm (0.0098 in.).
Coolant should always be applied when turning HRSA and titanium alloys, regardless of whether carbide or ceramic inserts are used. The volume of refrigerant should be high and well managed.
When using ceramics, it is recommended to apply a pre-chamfering operation to minimize the risk of burr when the insert enters and exits the cut for optimum performance.
Turning of non-ferrous materials (hliník)
This group contains non-ferrous soft metals such as aluminum, meď, bronz, mosadz, metal matrix composites (MMC) and magnesium. Ease of machining differs based on alloy elements, heat treatments, and manufacturing processes (forging, odlievanie, atď.).
Turning of aluminum alloys
Material classification: N1.2
Basic positive and sharp-edged inserts should always be used. The first choice is uncoated and PCD grades.
For aluminum alloys with a Si content greater than 13%, PCD should be used since the service life of solid carbide grades is significantly reduced.
In aluminum machining, coolant is used primarily for chip evacuation.
Mild Steel Turning
Turning hardened steel with a typical hardness of 55–65 HRC is defined as hard part turning and is a cost-effective alternative to grinding. Hard part turning offers greater flexibility, optimized lead times and higher quality.
Cubic boron nitride (CBN) grades are the quintessential cutting tool material for hard part turning of case hardened and induction hardened steels. For steels with a hardness of approximately less than 55 HRC, use ceramic or carbide inserts.
Use CBN grades optimized for hard part turning.
Make sure you have good machine and fixture stability.
Use the smallest depth of cut possible for a small stance angle and correct edge preparation to improve tool life.
Use a wiper to achieve the best surface finish.