Challenge: How to re-optimize hard material part turning?
Решение: Correct application of the latest turning insert grades and geometries based on existing operating data.
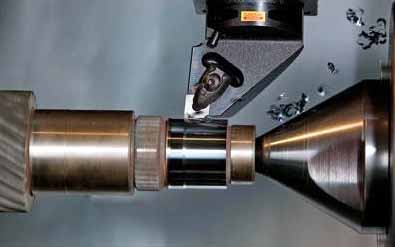
Turning chilled cast iron
Hard material turning (HPT) as a machining process has come a long way since it was widely promoted in the mid-1980s. Advances in machinery, part materials, quenching processes, cutting tools, and complete hard part turning setups have made hard part turning a highly efficient process that can be mastered by any shop.
The many benefits of hard part turning make it necessary to analyze most applications involving round hard parts. While hard part turning should not be considered a replacement for all grinding operations, there are some applications where the two processes can complement each other.
Cubic Boron Nitride Reduces Cycle Time, Improves Quality and Production Efficiency
The main advantages of hard part turning are:
• Easy to adapt to complex part shapes
• Quickly switch multiple parts
• Ability to perform multiple operations in a single setup
• High metal removal rate
• Ability to take advantage of the calculator CNC lathes used for commissioning turning
• Low investment in machine tools
• Metal chips are good for the environment
• Coolant not required in most cases
• Minimize tool stocks and floor space
• Surface finish tends to be an advantage.
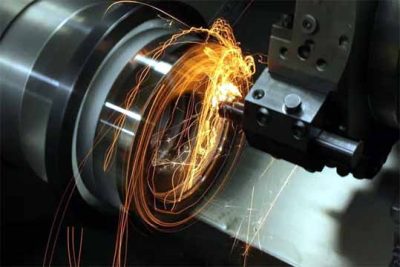
Turning of hard steel workpieces
Cubic boron nitride (CBN) is the most widely used tool material for hard part turning because it meets the requirements of most applications. It is very hard (second only to diamond) and can be combined with blade grades of varying toughness. There are several newly developed grades of CBN inserts available today to meet evolving process requirements such as: cutting speeds, feeds, continuous and interrupted cuts, surface finishing, and various operating conditions.
The combination of high cutting force concentrated in the machining area and high temperature generates high pressure. Поэтому, in the machining of hard parts, the main manifestation of tool wear is crater wear on the cutting edge. Hard cubic boron nitride is the only tool material that can meet these requirements with reasonable toughness. Recent developments in CBN grades have provided the means to further limit wear while also improving edge safety, expanding application range and increasing cutting speeds by around 20%.
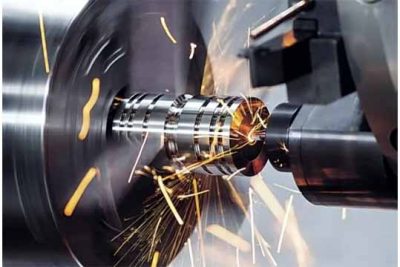
Turning of superhard materials
Productivity, quality consistency and process reliability are the basic criteria for hard part turning today. As hard part turning has developed into a widely used process with the advantage of finishing parts after heat treatment, various demands have been made in terms of machining efficiency.
As productivity is an increasingly important factor in today’s hard part machining, tool development plays an important role. Trends include higher cutting speeds (over 200 m/min for some grades), longer tool life, and improved tool life predictability. Feed rates have also been increased, and cutting times have been shortened through the development of insert strength and geometry.
Hardening of inserts is becoming increasingly desirable to meet the operational requirements of today’s cutting world. Cubic boron nitride grades are generally preferred, followed by ceramic grades, optimizing for a variety of application needs:
• CB7015 is suitable for continuous cutting with stable working conditions to occasional light interrupted cutting, mainly used for surface hardened steel.
• CB7025 is suitable for longer continuous cuts to heavier interrupted milling. Often characterized by poor plunge conditions, such as burrs and non-beveled corners, mainly for hardened steels.
• CB7050 is suitable for severe conditions where the shape of the parts varies greatly and may have severe distortion, or there are non-inclined breaks, mainly for hardened steels.
• GC6050 is a ceramic grade that complements cubic boron nitride in some operations and is suitable for light duty continuous finishing in good conditions. Mainly used for case hardened steels where surface quality is not critical.
For machining parallel or perpendicular to the part centerline, case hardened parts
Turning of hard parts should use Xcel inserts of the CB7015 series
In terms of insert geometry, the cutting edge of hard part machining inserts is relatively blunt due to the high edge strength required, but this does not mean that the geometry issue is not important. While the chipbreaker is not part of the edge chamfering of the insert profile, the combination of honing, nose radius, wiper edge and lead angle is critical to performance and results.
Over the years, wiper insert technology has revolutionized turning finishing in general. It also improves hard part turning. Сегодня, specially developed wiper inserts are available for hard part turning finishing and semi-finishing operations with significantly higher feedrate capabilities than conventional nose radii.
The Xcel insert geometry is a further optimization of the feedrate/surface finish for hard part turning. It carefully balances a straight cutting edge with a small entry angle with wiper technology. This small lead angle accepts the lead angle of the main insert, which is slightly higher than the depth of cut value of the insert. It acts to thin the chips, allowing higher feed rates to be used. This will benefit productivity and help reduce insert wear at depth-of-cut boundaries. The Xcel concept reduces cutting temperatures and brings considerable productivity gains.
Hard Part Turning (HPT) is the CNC turning of high hardness workpieces. Typically, the hardness range for this process is 58 к 68 HRc. Workpiece materials include hardened alloy steel, tool steel, case hardened steel and heat treated powder metallurgy parts. It is mainly a finishing process, but it can also be a semi-finishing process, which requires high precision in size, shape and surface finish. These surfaces have traditionally been ground.