В мгновение ока, Работаю на токарных станках с ЧПУ более десяти лет., и накопили некоторые навыки обработки и опыт работы на токарных станках с ЧПУ.. В том числе токарная обработка различных материалов (нержавеющая сталь, алюминий, медь, углеродистая сталь, титан, цементированный карбид, и т. д.). Из-за частой замены обрабатываемых деталей и ограниченных заводских условий, уже десять лет мы программируем сами, настраиваем инструменты сами, доводка и доработка деталей сами. В итоге, навыки эксплуатации делятся на следующие пункты.
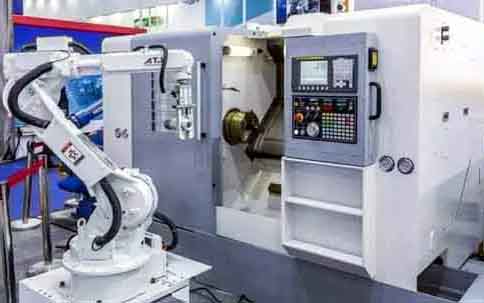
Работа на токарном станке с ЧПУ
Один, Навыки программирования токарных станков
Потому что на нашем заводе высокие требования к точности обрабатываемой продукции., вещи, которые необходимо учитывать при программировании,:
1. Processing sequence of parts:
Drill first, then turn the flat end (this is to prevent shrinkage during drilling);
Rough turning first, then fine turning (this is to ensure the accuracy of parts);
The position with large tolerance is processed first, and the final processing with small tolerance (this is to ensure that the surface of small tolerance size is not scratched and prevent deformation of parts).
2. Choose reasonable speed, feed and depth of cut according to material hardness:
1) Select carbon steel material with high speed, high feed rate and large cutting depth. Такой как: 1Gr11, select S1600, F0.2, and cut depth 2mm;
2) Low speed, low feed rate and small cutting depth are selected for hard alloy. Такой как: GH4033, select S800, F0.08, and cut depth 0.5mm;
3) Choose low speed, high feed rate and small cutting depth for titanium alloy. Такой как: Ti6, select S400, F0.2, and cut depth 0.3mm.
Take the processing of a certain part as an example: the material is K414, which is a very hard material. After many tests, the final selection is S360, F0.1, and the depth of cut 0.2, in order to process qualified parts.
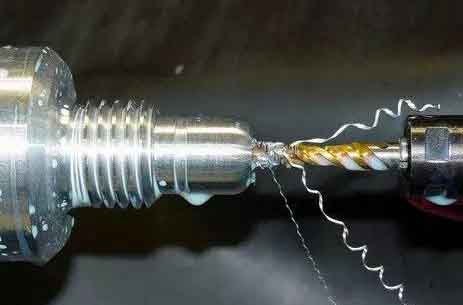
Процесс сверления на токарном станке с ЧПУ
два, Tool setting skills of lathe
Tool setting is divided into: tool setting with tool setting instrument and direct tool setting. The tool setting technique mentioned below is direct tool setting.
First select the center of the right end face of the part as the tool setting point and set it as the zero point. After the machine tool returns to the origin, each tool that needs to be used is set with the center of the right end face of the part as the zero point;
When the tool touches the right end face, enter Z0 and click to measure, and the measured value will be automatically recorded in the tool compensation value, which means that the Z-axis tool is set. X tool setting is a trial cutting tool setting, and the outer circle of the part is turned with a tool. Measure the value of the turned outer circle (например, x is 20mm) and enter x20, click Measure, the tool compensation value will automatically record the measured value, and then the x axis will also complete the tool setting;
This tool setting method will not change the tool setting value even after the machine is powered off. It is suitable for mass production of the same part for a long time, during which the lathe does not need to recalibrate the tool after restarting.
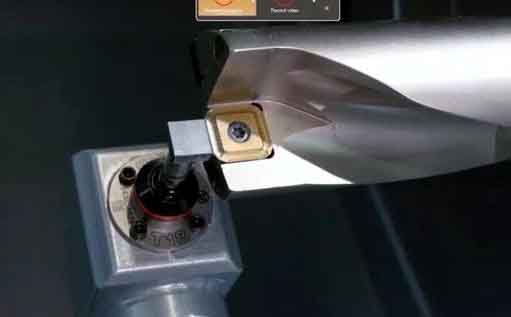
Common tool setting instruments for CNC lathes
три, Debugging skills of lathe
После программирования деталей, необходима пробная резка и отладка после настройки инструмента. Во избежание ошибок и ошибок настройки инструмента в программе, приводящих к несчастным случаям при столкновении., мы должны сначала выполнить обработку моделирования холостого хода. В системе координат станка, переместите инструмент вправо на 2-3 раз больше общей длины детали; Затем начните обработку моделирования. После завершения обработки моделирования, убедитесь, что программа и настройка инструмента верны, а затем приступаем к обработке деталей. После завершения первых работ по механической обработке деталей, первое самотестирование, чтобы подтвердить право на участие, проверьте, чтобы найти штатных инспекторов, квалифицированные штатные инспекторы подтвердили, что это указывает на окончание ввода в эксплуатацию.
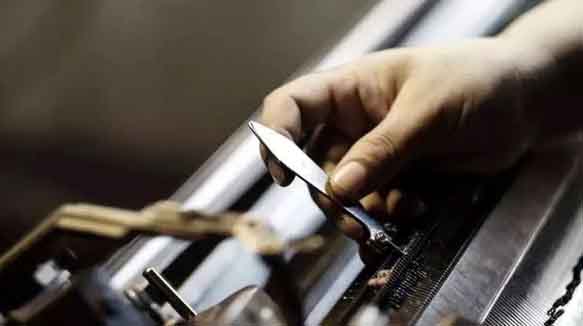
Пробная резка и доводка токарных станков с ЧПУ.
четыре, Finish machining of parts
After the trial cut of the first prototype is completed, the parts will be mass produced. Однако, the qualified product of the prototype does not mean that the entire batch of parts will be qualified, because in the processing process, the tool will wear out due to the difference in the processing materials. When the processing material is soft, the tool wear is small, and the processing material is hard and the tool wears quickly. Поэтому, in the process of processing, it is necessary to check more, increase and decrease the tool compensation value in time to ensure the qualified parts.
Take a part as an example, the processing material is K414, and the total processing length is 180mm. Due to the extremely hard material, the tool wears very quickly during processing. От начальной точки до конечной точки, угол 10-20 мм будет возникать из-за износа инструмента.. Поэтому, надо искусственно добавить в программу величину компенсации 10-20мм, Чтобы обеспечить квалифицированные детали.
Основные принципы токарной обработки: Сначала черновая обработка, удалить излишки материала с заготовки, а затем закончить обработку; Избегайте вибрации во время обработки; Избегайте термической денатурации заготовки во время обработки.. Существует множество причин вибрации, вызванной чрезмерной нагрузкой.; Это может быть резонанс станка и заготовки., или жесткость станка может быть недостаточной, или это может быть вызвано пассивацией инструмента. Мы можем уменьшить вибрацию следующими методами; Уменьшите поперечную подачу и глубину обработки., проверьте, надежно ли закреплена заготовка, увеличьте скорость инструмента и уменьшите скорость, чтобы уменьшить резонанс. Кроме того, проверьте, необходимо ли заменить новый инструмент.
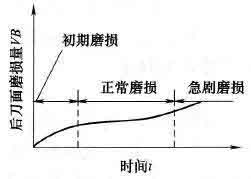
Процесс износа токарных инструментов и стандарт затупления
Пятерки, Опыт предотвращения столкновений машин
Столкновение станка наносит серьезный ущерб точности станка., и это по-разному влияет на разные типы станков. Вообще говоря, оказывает большее воздействие на станки с низкой жесткостью. Поэтому, для высокоточных токарных станков с ЧПУ, коллизии должны быть абсолютно исключены. При условии, что оператор осторожен и владеет определенными методами предотвращения столкновений., Столкновения можно предотвратить и избежать.
Основная причина столкновения:
1> Неверно укажите диаметр и длину инструмента;
2> Размер заготовки и другие сопутствующие геометрические размеры введены неверно, и исходное положение заготовки установлено неправильно;
3> Система координат заготовки станка установлена неправильно, или нулевая точка станка сбрасывается в процессе обработки, что вызывает изменение. Большинство столкновений станков происходит во время быстрого движения станка.. Столкновения, происходящие в это время, также являются наиболее вредными, и их следует категорически избегать.. Поэтому, оператор должен уделять особое внимание станку на начальном этапе выполнения программы и при смене инструмента на станке. В это время, однажды программа отредактирована неправильно и неправильно введены диаметр и длина инструмента, collisions are likely to occur. At the end of the program, if the NC axis retracts the tool in a wrong sequence, then collisions may also occur.
In order to avoid the collision mentioned above, the operator must give full play to the sensory functions when operating the machine tool. Observe whether there is abnormal movement of the machine tool, whether there is spark, whether there is noise and abnormal noise, whether there is vibration, whether there is a burning smell. The program should be stopped immediately when the abnormal situation is found, and the machine tool can continue to work after the problem of the standby bed is solved.