When titanium alloy is milled at low speed in an inert gas medium, the milling deformation coefficient is greater than 1.0; But in the atmosphere, when the milling speed Vc=30 m/min, the chip deformation coefficient is less than 1.0. This is because titanium alloys have a great affinity for oxygen and nitrogen in the atmosphere during high-temperature milling. Under the condition of high temperature of 800℃, the chips of titanium alloy violently absorb these gases from the surrounding atmosphere, causing a phase change and re-elongation of the shortened milling chips. When the titanium alloy is milled, the temperature is very high and the impact force is large. The cutter tooth material of the milling cutter should be able to withstand the alternating load and thermal shock well. YG type cemented carbide is usually used, and cobalt and aluminum super-hard high-speed steel can also be used.
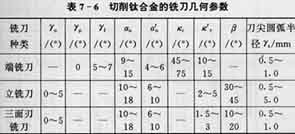
Geometric parameters of milling cutter for milling titanium
The geometric parameters and milling parameters of titanium alloy milling cutters are shown in Table 7-6 и таблица 7-7.
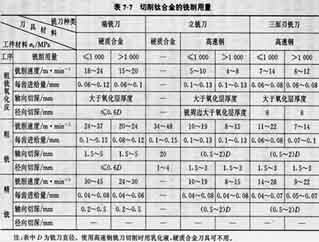
Set the cutting amount of milling titanium
When milling titanium alloys, it is advisable to use asymmetric down milling. Таким образом, the part of the front of the cutter teeth away from the tip of the cutter first contacts the workpiece, and the chips when the cutter teeth are cut away are very thin, and it is not easy to stick to the cutting edge. With up-cut milling, the edge of the milling cutter is prone to chip sticking. When the cutter tooth cuts in again, the chip is broken, causing the cutter material to peel off and chipping.
The offset e between the end milling cutter and the axis of the workpiece can determine the best position where the cutter teeth of the milling cutter first contact the workpiece. The chip thickness during down milling or up-milling and cutting off is generally based on the offset e=(0.04~0,1) делать (do is the diameter of the end milling cutter).
Due to the small modulus of elasticity of titanium alloys, down milling causes tool loss, which requires the machine tool and tool to have greater rigidity. При фрезеровании, the contact length between the tool and the chips is short, and it is not easy to curl up the chips. The tool is required to have good tooth strength and a larger chip holding space, otherwise the blockage of chips will cause severe wear of the tool.