What is milling? What is the process of milling? What parts can be machined by CNC milling? What precision can China mill parts achieve?
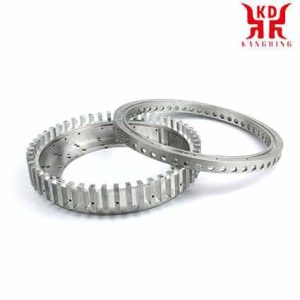
What is milling?
CNC milled parts
How are CNC milled parts manufactured?
CNC milled parts are machined on CNC milling machines with the help of rotating tools. CNC milling machines with different degrees of freedom of movement are used: 3-ось, 4-axis and 5-axis milling machines.
3-axis milling machines can only machine CNC milled parts from one accessibility direction. They are cheaper than the other types of milling machines. 4-axis milling machines have an additional axis of rotation for the milled part, for example for the production of spindles and other helical geometries. 5-Осевые фрезерные станки могут обрабатывать фрезерованные детали с ЧПУ со всех сторон., в зависимости от зажима, а также создавать сложную геометрию.
С нашей сетью поставщиков, мы можем изготовить широкий спектр фрезерованных деталей с ЧПУ для самых разных требований..
Мы специализируемся на механической обработке с ЧПУ, наш автоматический расчет цен постоянно расширяется и в настоящее время охватывает компоненты со следующими свойствами.
Фрезерование заключается в основном в резке материала, который обрабатывается вращающимся инструментом с несколькими кромками., называемые зубы, кромки или твердосплавные вставки, который выполняет запрограммированные перемещения рабочего стола практически в любом направлении из трех возможных осей, по которым может перемещаться стол, на котором фиксируется обрабатываемая деталь..
С ростом использования фрезерных станков с числовым программным управлением, the milling operations that can be carried out with this type of machine are increasing, and thus milling has become a multipurpose machining method. The development of the tools has also contributed to create new possibilities of milling in addition to considerably increasing the productivity, quality and accuracy of the operations carried out.
Our manufacturing options for CNC milled parts
Component dimensions from 2 mm x 2 mm x 2 мм |
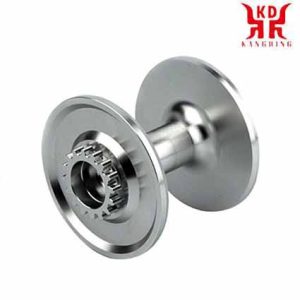
фрезерные детали с чпу
Milling tools
The milling tools are characterized by their outside diameter, the number of teeth, the pitch of the teeth (understood as the distance between two consecutive teeth) and the fastening system of the cutter on the machine.
Types of milling
In the universal milling machines using the appropriate accessories or in the numerical control milling machines the following Planning can be carried out.
The most frequent application of milling is face milling that aims to achieve flat surfaces. For the face milling milling cutters with interchangeable carbide inserts are generally used, there is a very varied range of diameters of these mills and the number of inserts that each milling cutter mounts. Insert manufacturers recommend as a first option the use of round inserts or with 45º angles as an alternative.
Square milling. Square milling is a variant of face milling that consists of leaving perpendicular steps in the part to be machined. Для этого, square inserts are used that are located in the tool holder in an appropriate way.
Cube Milling. The cubing operation is very common in vertical or horizontal milling machines and consists of preparing the metal dowels or other material such as marble or granite in the appropriate cubic dimensions for subsequent operations. This milling is also done with interchangeable insert face milling cutters.
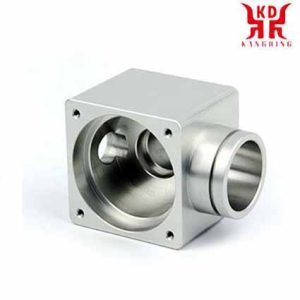
фрезерные детали с чпу Виды фрезерования
Cut milling. One of the initial machining operations that must be carried out often consists of cutting the pieces to the determined length starting from commercial bars and profiles of a greater length. Band saws or milling machines equipped with cylindrical cutters are used interchangeably for industrial cutting of parts. What is significant about cutting burs is that they can be made of high-speed steel or hard metal. They are characterized by being very thin (on the order of 3 мм, although it may vary), having a large diameter and very fine teeth. An example of the characteristics of a cutter would be the following: diameter of 200 мм, thickness of 3 мм, diameter of the hole of 32 mm and 128 зубы: Fine 128, Coarse 64.
Straight Grooving Milling. For milling straight grooves, cylindrical cutters with the width of the groove are generally used and often, to increase production, several cutters are mounted on the cutter shaft allowing to increase machining productivity. The assembly of several cylindrical strawberries is called a train of strawberries or compound strawberries. Cylindrical burs are characterized by having three cutting edges: the front and the two sides. High speed steel burs are used in most applications since carbide burs are very expensive and are therefore only used in very large productions.
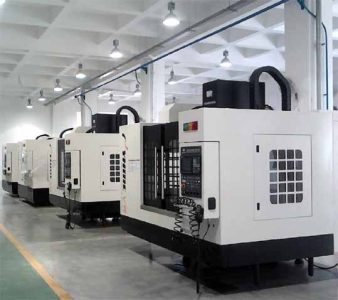
фрезерные детали с чпу Виды фрезерования
Shape grooving.. Burs of the appropriate shape for the groove are used, which can be T-shaped, dovetail, и т. д..
Keyway grooving. Cylindrical strawberries with handles, known in slang as ballerinas, are used that can cut both in a direction perpendicular to its axis and parallel to it.
Milling in Copying. Round insert profile cutters are used for copy milling in order to be able to carry out machining operations in orographies and profiles of changing faces. There are two types of copy cutters: those with a half ball profile and those with a round or toric edge.
Cavity milling. In this type of operation, it is advisable to carry out a prior drilling and from there and with suitable milling cutters, approach the cavity machining, bearing in mind that the radii of the cavity must be at least 15% greater than the radius of the milling cutter.
Lathe-milling. This type of machining uses circular interpolation in numerical control milling machines and is used for both precision hole turning and external turning. The process combines the rotation of the workpiece and the milling tool, making it possible to achieve a cylindrical surface. This surface can be concentric with respect to the center line of rotation of the part, or it can be eccentric if the milling is moved up or down. With axial displacement it is possible to achieve the required length.
Thread milling. Thread milling requires a milling machine capable of simultaneous helical interpolation in two degrees of freedom: the rotation of the part with respect to the axis of the helix of the thread and the translation of the part in the direction of said axis.
Face milling. It consists of milling that is carried out with cylindrical helical burs that attack the milling operation frontally. More and more fully integral carbide burs are used in numerical control milling machines that allow working at very high speeds.
Gear milling. Gear milling is hardly carried out on universal milling machines using the dividing plate anymore, but is done on special machines called gear hobbing machines and with the use of special milling cutters of the appropriate tooth module.
Бурение, reaming and boring. These operations are usually carried out on numerical control milling machines equipped with a tool magazine and using the appropriate tools for each case.
Mortising. It consists of machining keyways in the holes, для чего используются протяжные станки или специальный аксессуар, который крепится к головке универсального фрезерного станка и преобразует вращательное движение в альтернативное вертикальное движение.
Рамповое фрезерование. Это распространенный тип фрезерования при обработке форм, который выполняется либо на копировально-фрезерных станках, либо на фрезерных станках с числовым программным управлением..
Как работает фрезерный станок с ЧПУ?
Внедрение компьютеризированного числового управления. (ЧПУ) экспоненциально расширил применение промышленных машин за счет программируемой автоматизации производства и достижения движений, которые невозможно выполнить вручную., такие как круги, диагональные линии и другие более сложные фигуры, позволяющие изготавливать детали весьма сложных профилей.. This also translates into the optimization of many essential variables of any manufacturing process: productivity, precision, safety, speed, repeatability, flexibility and reduction of waste.
The multiplicity of milling machines that exist today has comfortably expanded into the proliferation of their CNC-equipped peers. Фактически, there are also special kits to transform old milling machines into a CNC milling machine.
Basically, the CNC milling machines are very similar to the conventional ones and have the same moving parts, то есть, the table, the cutting head, the spindle and the side and cross slide carriages. Однако, they do not have levers or cranks to operate these moving parts, but rather a screen inserted in a panel full of controls and a metal box that houses the electrical and electronic components that regulate the operation of motors destined to carry out the same work that they did. the levers and cranks of the old machines. Among these components is the CNC, which is a computer mainly responsible for the movements of the milling machine through the corresponding software. The combination of electronics and drive motors or servo motors is capable of achieving all possible milling operations.
To understand the movement control exercised by the CNC, we are going to briefly review how a conventional milling machine works.
The figure schematizes a typical milling machine. In this type of machine, the cranks actuate the moving parts manually so that the cutting tool (milling cutter) moves linearly in at least three axes, which are called main axes:
X axis: horizontal and parallel to the clamping surface of the part. It is associated with the movement in the longitudinal horizontal plane of the milling table.
Y axis: forms a direct direction trihedron with the X and Z axes. It is associated with the movement in the horizontal transverse plane of the milling table.
Z axis: where the cutter is mounted, it is the one that has the cutting power and can adopt different positions according to the possibilities of the head. It is associated with the vertical displacement of the machine head.
If the milling machine has a fixed table, these three movements are executed by the spindle.
Однако, it is clear that the milling of more complex parts will require a greater number of axes whose trajectory is not only linear, but also rotary. At this point is where the concept of CNC comes into play, giving rise to a multiplicity of complementary axes controlled independently and determined by the movement of rotary tables and / or adjustable heads. This gives rise to a variety of machine models that allow the machining of the part by different planes and approach angles.
In the following figure we see an example of a CNC milling machine with its basic components and main (Икс, Да, Z) and complementary (Б, Вт) axes.
1 – Column
2 – Workpiece
3 – Milling table, with movement in the X and Y axes
4 – Поворот
5 – Cutting head including spindle motor
6 – CNC control panel
7 – Coolant hoses
Икс, Да, Z – Main axes of travel
Б – Complementary axis of rotary displacement of the cutting head
Вт – Complementary axis of longitudinal displacement of the cutting head
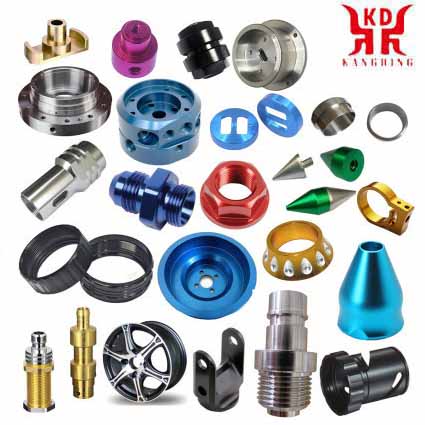
фрезерные детали с чпу Виды фрезерования
The main function of the CNC is to control the movements of the table, the transverse and longitudinal carriages and / or the spindle along their respective axes by means of numerical data. Однако, this is not all, because the control of these movements to achieve the desired final result requires the perfect adjustment and the correct synchronization between different devices and systems that are part of every CNC process. These include the main and complementary axes, the transmission system, the workpiece clamping systems and the tool changers, each of which presents its modalities and variables that must also be properly stipulated.
This rigorous control is carried out by software that is supplied with the milling machine and is based on one of the CNC numerical programming languages, such as ISO, HEIDENHAIN, Fagor, Fanuc, SINUMERIK and Siemens. This software contains numbers, letters and other symbols – например, the G and M codes – that are encoded in an appropriate format to define an instruction program capable of carrying out a specific task. G codes are machine motion functions (rapid moves, feeds, radial feeds, pauses, cycles), while M codes are miscellaneous functions that are required for machining parts, but are not machine motion. (spindle start and stop, tool change, coolant, program stop, и т. д.). From this it follows that to operate and program this type of machine requires basic knowledge in machining operations on conventional equipment, elementary knowledge of mathematics, technical drawing and handling of measuring instruments.
В настоящее время, the use of CAD (computer-aided design) and CAM (автоматическое производство) programs is an almost obligatory complement to any CNC machine, which is why, в целом, the manufacture of a part involves the combination of three types of software:
САПР: makes the design of the part.
САМ: calculates the displacements of the axes for the machining of the part and adds the feed rates, rotation speeds and different cutting tools.
Control software (included with the machine): receives the instructions from the CAM and executes the orders to move the moving parts of the milling machine in accordance with these instructions.
The following video illustrates the manufacture of a part using CAD / САМ:
CNC milling machines are specially adapted for milling profiles, cavities, контуры поверхности и операции высечки, при котором две или три оси фрезерного стола должны управляться одновременно. Хотя, в зависимости от сложности станка и выполняемого программирования, Фрезерные станки с ЧПУ могут работать автоматически., для замены фрез обычно требуется оператор, а также монтаж и демонтаж заготовок.
Отрасли, в которых обычно используются фрезерные станки с ЧПУ, включают автомобилестроение. (конструкция блоков двигателя, формы, и разные компоненты), аэрокосмический (авиационные турбины), и электроника (пресс-форма и прототипирование), а также производство машин, инструменты и электрические компоненты.