Причин деформации алюминиевых деталей множество., которые связаны с материалом, инструмент обработки, форма детали, и технологическое оборудование. В основном это следующие аспекты: Деформация, вызванная внутренним напряжением заготовки., деформация, вызванная силой резания и теплом резания, и деформация, вызванная силой зажима.
Один, Технологические мероприятия по снижению деформации обработки
1. Уменьшите внутреннее напряжение алюминиевой заготовки.
Естественное или искусственное старение и вибрационная обработка позволяют частично устранить внутренние напряжения заготовки.. Предварительная обработка также является эффективным методом процесса.. Для больших заготовок, из-за большой маржи, деформация после обработки также велика. Если лишняя часть заготовки обрабатывается заранее и уменьшается припуск каждой детали, деформация обработки в последующем процессе может быть уменьшена. Более того, после предварительной обработки и размещения на определенный период времени, часть внутреннего напряжения также может быть снята.
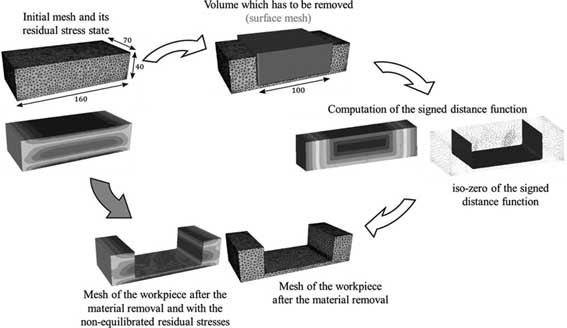
Причины фрезерной деформации алюминиевых деталей
2. Улучшить режущую способность инструмента.
Материал и геометрические параметры инструмента оказывают важное влияние на силу резания и теплоту резания.. Правильный выбор инструмента имеет важное значение для уменьшения деформации деталей..
(1) Разумно выбирать параметры геометрии инструмента.
① Передний угол инструмента: При условии сохранения прочности клинка, передний угол должен быть соответственно больше. С одной стороны, он может шлифовать острые режущие кромки, и с другой стороны, это может уменьшить деформацию резки, сделать удаление стружки плавным, а затем уменьшите силу резания и температуру резки. Никогда не используйте инструменты с отрицательным передним углом..
② Угол наклона инструмента: Размер заднего угла оказывает прямое влияние на износ боковой поверхности и качество обрабатываемой поверхности.. Толщина резания является важным условием выбора заднего угла.. При черновом фрезеровании, из-за большой скорости подачи, тяжелая режущая нагрузка и большое выделение тепла, необходимы хорошие условия отвода тепла от инструмента. Поэтому, угол заднего угла должен быть меньше. При завершении фрезерования, режущая кромка должна быть острой, уменьшить трение между боковой поверхностью и обрабатываемой поверхностью, и уменьшить упругую деформацию. Поэтому, угол заднего угла следует выбирать больше.
③ Угол спирали инструмента: Для того, чтобы сделать фрезерование плавным и уменьшить силу фрезерования., угол спирали следует выбирать как можно больше.
④Угол в плане инструмента:
Правильное уменьшение угла входа инструмента может улучшить условия отвода тепла и снизить среднюю температуру зоны обработки..
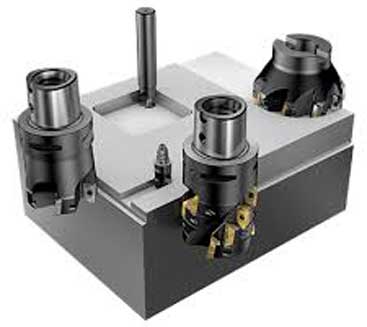
Режущая способность фрезы
(2) Улучшить структуру инструмента.
①Уменьшите количество зубьев фрезы и увеличьте пространство для стружки.. Благодаря большой пластичности алюминиевых материалов, большая деформация резания при обработке, и требуется больше места для чипа, поэтому нижний радиус стружкоприемной канавки должен быть больше, а количество зубьев фрезы должно быть меньше.
② Тонко заточить зубы. Значение шероховатости режущей кромки зуба фрезы должно быть менее Ra=0,4 мкм.. Прежде чем использовать новый нож, вам следует использовать тонкий масляный камень, чтобы аккуратно отшлифовать переднюю и заднюю часть зубьев ножа, чтобы устранить остаточные заусенцы и небольшие зазубрины при заточке ножа.. Таким образом, можно не только уменьшить теплоту резки, но и деформация резания относительно невелика.
③ Строго контролировать стандарты износа инструмента.. После износа инструмента, увеличивается значение шероховатости поверхности заготовки, температура резания повышается, и деформация заготовки увеличивается. Поэтому, в дополнение к выбору инструментальных материалов с хорошей износостойкостью, стандарт износа инструмента не должен превышать 0,2 мм., в противном случае легко получить накопившиеся кромки стружки. При резке, температура заготовки обычно не должна превышать 100°C во избежание деформации..
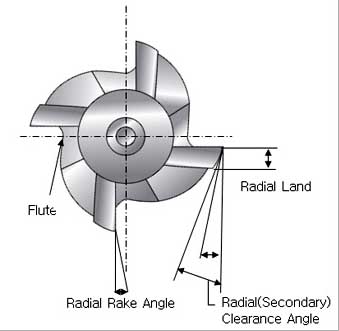
Геометрические параметры фрезерного инструмента
3. Улучшите метод зажима заготовки
Для тонкостенных алюминиевых заготовок с плохой жесткостью, Для уменьшения деформации можно использовать следующие методы зажима:
① Для тонкостенных втулок., если для зажима в радиальном направлении используется трехкулачковый самоцентрирующийся патрон или пружинный патрон, как только он будет выпущен после обработки, заготовка неизбежно будет деформирована. В это время, следует использовать метод прессования осевого торца с большей жесткостью. Чтобы найти внутреннее отверстие детали, сделать самодельную оправку с резьбой насквозь, вставьте его во внутреннее отверстие детали, прижмите торец накладкой и затем затяните ее гайкой. Деформацию зажима можно избежать при обработке внешнего круга., тем самым получая удовлетворительную точность обработки.
② При обработке тонкостенных и тонколистовых заготовок с полостью., лучше всего использовать вакуумные присоски для равномерного распределения прижимной силы., а затем обработать меньшим количеством резания, который может хорошо предотвратить деформацию заготовки.
Кроме того, Также можно использовать метод упаковки. С целью повышения технологической жесткости тонкостенных заготовок, среда может быть заполнена внутри заготовки, чтобы уменьшить деформацию заготовки во время зажима и резки. Например, залить расплав мочевины, содержащий 3% к 6% нитрат калия в заготовку, и после обработки, погрузите заготовку в воду или спирт для растворения наполнителя и вылейте его.
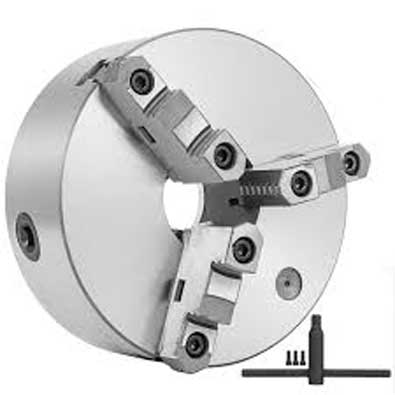
Трехкулачковый самоцентрирующийся патрон
4. Разумная организация процедур обработки
Во время высокоскоростной резки, благодаря большому припуску на обработку и прерывистому резанию, процесс фрезерования часто вызывает вибрацию, что влияет на точность обработки и шероховатость поверхности. Поэтому, Процесс высокоскоростной резки с ЧПУ обычно можно разделить на: Черновая обработка, получистовая обработка, обработка углов, чистовая обработка и другие процессы.. Для деталей с высокими требованиями к точности, иногда необходимо выполнить вторичную получистовую, а затем чистовую обработку. После черновой обработки, детали могут охлаждаться естественным путем, чтобы устранить внутренние напряжения, вызванные грубой обработкой, и уменьшить деформацию.. Припуск, оставшийся после черновой обработки, должен быть больше, чем величина деформации., в целом 1 к 2 мм. Во время отделки, на чистовой поверхности детали должен сохраняться равномерный припуск на механическую обработку, обычно подходит 0,2-0,5 мм, чтобы инструмент находился в стабильном состоянии во время процесса обработки.. Это может значительно уменьшить деформацию резки., получить хорошее качество обработки поверхности, и обеспечить точность продукта.
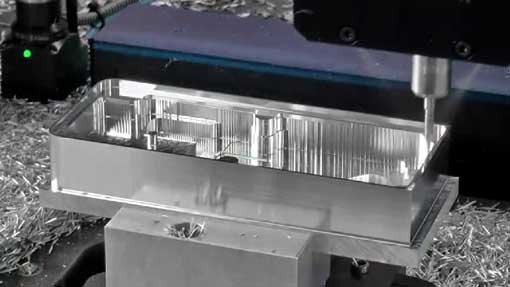
Высокоскоростная резка алюминиевых деталей