Acessórios para máquinas de máscara facial plana, eixo de gravação, pressione a roda, rolo de máquina de máscara, rolo
O rolo é a parte principal do laminador. Está sujeito a um certo impacto durante o uso real, e a superfície é esfregada por alta velocidade, aço vermelho de alta temperatura. A superfície deve ter boa resistência à abrasão, e ao mesmo tempo, deve ter resistência suficiente para evitar que seja quebrado por impacto.
In view of the special purpose of the roller, its material must have:
1, high-speed wear resistance;
2, enough red hardness;
3. Sufficient strength and toughness.
In actual use, it is more appropriate to approximate white cast iron. No entanto, since this material is generally used in the as-cast state, casting defects inevitably exist, and the hardness can reach 50-60HRC. Além disso, the roller wheel (as shown in the figure) requires a high degree of coaxiality, which brings great difficulties to the turning process.
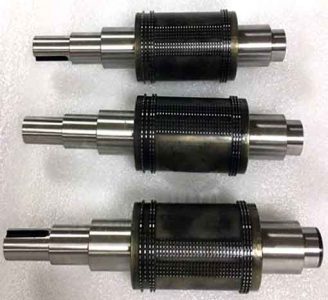
Processamento de torneamento do rolo de gravação da máquina de máscara
1. Reasonably choose the brand of turning tools
The strength and hardness of the roller material have reached the strength and hardness of ordinary carbide tools (Yt), so ordinary tools cannot cut normally at all. Although the hardness can be appropriately reduced by quenching and tempering treatment, which is convenient for cutting processing, but the cost is too large and the cycle is long, so direct processing in the as-cast state is still selected. Through trial-cutting and repeated comparison of various high-hardness tools (including ceramic tools and imported tools), the YS8 brand turning tool, whose hardness and wear resistance meet the cutting requirements and is relatively low in price, was selected for turning. Claro, for the rollers that need to be repaired after use, because the use process is equivalent to cold work hardening, the hardness is extremely high, and YS8 can not be cut, we use ceramic blades for turning and repairing.
2. The geometric angle and cutting amount of the tool for turning cast iron rollers
Because there are considerable elements such as Cr and Mo in the blank, it has good plasticity, high strength and hardness, and large deformation resistance. The cutting force is 2 para 3 times higher than that of ordinary steel, the cutting heat also increases, the thermal conductivity is low, the heat dissipation is difficult, the temperature in the cutting zone is extremely high, and the tool is easily damaged. Além disso, the blank is a casting, and there are defects such as surface crust, pores, blisters, uneven machining allowance, and uneven material hardness. This will inevitably lead to increased processing instability, reduced tool life, increased production costs, and decreased production efficiency. In response to these factors, we improve the cutting process by selecting cutting parameters reasonably.
1. Rough machining of cast iron rollers
During rough machining, the machining surface allowance is uneven, and the rough surface has a hard surface, so the cutting depth should be as large as possible. Quanto maior a profundidade de torneamento, the higher the cutting heat generated, and the greater the cutting force the tool can withstand. In order to enable the tool to withstand sufficient compressive stress, a negative rake angle and a negative edge angle (0°~-5°) are used to increase the rigidity of the tool;
The relief angle is generally between 6° and 8°, the main declination angle is between 10° and 30°, and the sub-deflection angle is between 10° and 15°. Due to the high hardness of the blank and poor heat dissipation, a low speed (80r/min) and a small feed rate (0.15mm/r) are used to appropriately reduce the cutting force during rough turning. The cutting depth is selected between 2 e 3 milímetros.
2. Finishing of cast iron rollers
Because the cutting depth is small, the cutting force is small, and the cutting heat is small, in order to improve the surface quality, a larger rake angle is used, and the rear angle is a larger value of 10°. Minimize the friction and extrusion between the tool and the workpiece to improve the surface processing quality of the workpiece, and the entering angle is between 10° and 30°; The secondary declination angle is between 5° and 10°. In order to avoid the outflow of chips from scratching the processed surface, a positive blade inclination angle between 0° and 5° is adopted. Using a higher spindle speed (120r/min), Small cutting depth (0.2~0.3mm) and small feed rate of 0.1mm/r.
3. Machining of the arc surface of cast iron rollers
Ao girar o círculo externo, inner hole and total length, it is more economical and economical to process on an ordinary lathe, but the size of the arc surface is not easy to guarantee on an ordinary lathe, so the arc surface of the roller is completed by a CNC lathe. In view of uneven blank margin and hard material, set low spindle speed and small feed by increasing the number of passes during programming. Aiming at the situation that sand holes and air holes are easy to cause the cutter head to break, set the starting point of the program before each cut during programming to avoid “starting from the beginning” after each cut. This can save a lot of time and reduce “useless work” to improve production efficiency.