Categorias de Produtos
Etiquetas de produto
Serviços de fresagem CNC na China
Fresagem CNC é um processo de fabricação no qual um software de computador pré-programado dita o movimento das ferramentas e máquinas da fábrica.. Protótipos rápidos ou peças de produção – Temos as opções certas de fresagem CNC para suas necessidades de produção de peças de plástico ou metal. O método pode ser usado para controlar uma série de máquinas complexas, desde retificadoras e tornos até fresadoras e fresadoras. Com fresagem CNC, tarefas de corte tridimensionais podem ser executadas em um único conjunto de instruções.
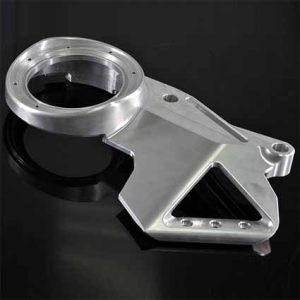
Acabamento CNC de peças de liga de alumínio
A fresagem CNC desempenha um papel vital na fabricação moderna.
O que é fresagem CNC? Como isso desempenha um papel na fabricação, e o que o maquinista CNC faz?
Fresagem CNC é um processo de fabricação no qual um software de computador pré-programado dita o movimento das ferramentas e máquinas da fábrica.. Protótipos Rápidos ou Peças de Produção – Temos as opções certas de fresagem CNC para suas necessidades de produção de peças de plástico ou metal. O método pode ser usado para controlar uma série de máquinas complexas, desde retificadoras e tornos até fresadoras e fresadoras. Com fresagem CNC, tarefas de corte tridimensionais podem ser executadas em um único conjunto de instruções.
Abreviação de “Controle Numérico Computadorizado”, o processo CNC contrasta com as limitações do controle manual, que exige que operadores ativos consultem e orientem comandos de ferramentas de usinagem por meio de alavancas, botões e rodas. Para o espectador, a CNC system may resemble a normal set of computer components, but the software programs and consoles used in CNC Milling set it apart from all other forms of computation.
Before NC and CNC Milling
NC machining and later CNC made it possible to control machine tools without the high proportion of manual intervention that had to take place until then to machine a part.
Por exemplo, before CNC and NC machining, the drilling of a tube was done by placing the tube in the press of the machine tool to hold it, selecting in this machine the rotation speed of the drill (generally with belt pulleys) and activating the spindle. These actions had a high proportion of manual manipulation (placing the bit on the axis, activating the axis, placing the workpiece under the drill, machining the hole and shutting down the axis), something that did not pose major problems with small quantities , but as it was required to machine a greater number of parts and carry out more complex machining actions, the probability of fatigue of the person due to the tedium of the operation increased, and therefore decreased productivity and increased the margin of error.
NC machining represented a breakthrough in this sense because it allowed the machine tool to be controlled by means of a perforated belt containing the movements of the machine in relation to the coordinate axes that specified the movement of the cutting tool. Desta maneira, the intervention of the person was not needed at each step, they could do other tasks, and productivity was greatly increased.
Before numerical control, machining processes had a high component of manual manipulation. Today some isolated operations are carried out manually, with few parts.
Subsequently, this control went from being done with a perforated tape to being done by computer, including the placement of the drill on the shaft, activation, etc.. This had several advantages.
Main advantages of CNC Milling
Improved automation compared to numerical control without a computer: This means that the intervention of the person in each step can be reduced or even eliminated, although some type of manual action always takes place for specific tasks, such as repair and prototyping. That allows for higher production in the same time, since CNC machines are capable of running 24 hours a day.
Greater precision and consistency of the pieces obtained: Today’s CNC machines have astonishing precision and repeatability specifications, with two, ten, or a thousand identical workpieces easily achievable once the program is verified. That was critical in mass production.
Greater flexibility: Being machine tools controlled by a computer program, carrying out a new machining that only contains a few small changes compared to a previous job only requires loading a saved project, making certain changes and saving it separately, as in any other software. This allows quick changes and adaptation to any type of part, and eliminates most prototypes.
Greater security: to have a minimal interaction of the operator with the machine in most of the movements. Previously, when intervening in actions such as changing heads, loading material, stopping a movement, etc., there were more chances of having accidents.
Main challenges of CNC Milling
High operating costs: Although CNC machines reduce the number of manual workers required in a manufacturing plant, the machines are more expensive to operate. No entanto, the costs associated with running the machines are gradually decreasing.
Training need: Initially, the generalization of CNC Milling led to high unemployment, as the need for manual workers was reduced. No entanto, with proper training, this system creates new opportunities for specialized employment. as it requires CNC machine tool operators, programmers, maintenance personnel, as well as machine tool manufacturing engineers and technicians and trainers to teach its operation.
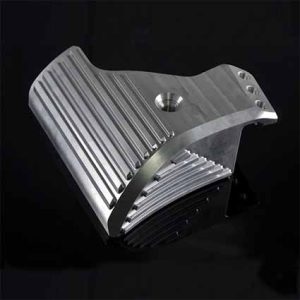
Peças de acabamento CNC
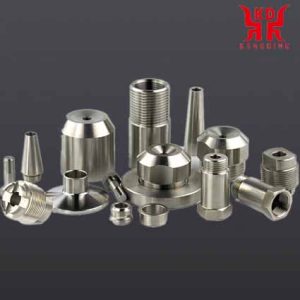
Acabamento CNC de peças de aço inoxidável
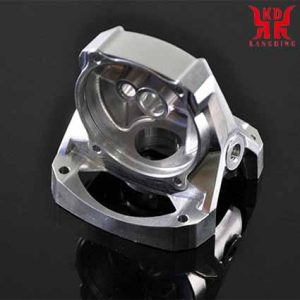
5-peças de acabamento de eixo
How CNC Milling Works
Broadly speaking, CNC Milling allows doing practically everything that was previously done manually: placing the drill bit on the axis, activating it, placing the part to be machined on the machine, machining it and turning off the axis. Once the machine tool is configured by CNC and put to work, it requires little intervention from the operators. You can even automate the part loading process.
No entanto, the task of the operator is still required to make measurement checks and adjustments to keep the CNC machine working properly.
Movement control
Any CNC Milling machine tool allows programming two or more directions of movement (eixos, which can be linear-along a straight line- or rotary-along a circular path-). Common linear axis names are X, S, e Z. Common rotary axis names are A, B, and C. The more axes the machine has, the more complex it is. In drilling, the three linear axes would position the tool over the hole to be machined in the part on the X and Y axes and would machine the hole with the third Z axis.
Programmable accessories
Although the fundamental function that all CNC Milling machines have is to control movement according to axes, what really gives value to each machine is not moving the part in two or more axes. but rather the programmable accessories that it carries, which make them multiply their functions.
Por exemplo, a machining center may have an automatic tool loader to change the cutting instrument without operator intervention. and if necessary, you can choose the tool and automatically place it on the spindle for machining, or programming the axis speed and spindle activation, or the coolant to lubricate and cool the part that can be turned on and off from within of the machine cycle.
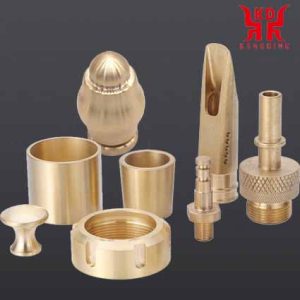
CNC finishing of copper parts
With the CNC Milling system, a part is machined using the following steps:
1) Design of the conceived part: use CAD software to create a 2D or 3D model of the part.
2) CNC programming: use CAM software to convert CAD model to g-code. G-Code is the language used to program CNC machines, which can be edited from a normal text manager (Notepad, Word) or a specialized program.
3) CNC machine setup: In this step, the machine is setup by clamping, suitable tools and G-code editing program (by DNC system), and the tool data is loaded to prepare the machine to machine the part. The operator will also tell the machine where the zero point is to start.
4) CNC Milling of the part: with all the above ready, it is time to start machining the part.
CNC Milling allows doing practically everything that was previously done manually: placing the drill bit on the axis, activating it, placing the part to be machined on the machine, machining it and turning off the axis.
Metal industry and CNC Milling
CNC Milling has revolutionized the metal industry, decisively influencing its economic potential, with higher production at lower cost. Basically we can distinguish three large groups within the metal industry that make CNC Milling machine tools their main work system:
Metal fabrication industry: Thin plates such as steel plates are required in many industries for various purposes, and such plates are machined in the manufacturing industry. generally with CNC machines that carry out various operations such as cutting, flame or plasma cutting, socando, laser cutting, contouring and welding and many other applications.
This industry was one of the most used manual machines decades ago (punching machines, disc cutting machines, presses, etc.) mas hoje as versões CNC dessas mesmas máquinas estão totalmente ampliadas e são utilizadas de forma majoritária.
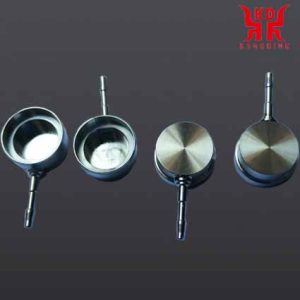
Cavidade de liga de titânio para implante médico
Protótipos Rápidos ou Peças de Produção - Temos as opções certas de fresagem CNC para suas necessidades de produção de peças de plástico ou metal.
Ampla gama de materiais
Conheça as tolerâncias mais rigorosas
Usinagem de peças diretamente de modelos CAD 3D
Prazo de entrega padrão entre 1 e 2 semanas, dependendo do pedido
Os prazos de entrega podem ser mais curtos (2 para 5 dias úteis), dependendo da capacidade disponível
Tolerâncias para o tamanho dos detalhes:
Padrão: +/- 0.005
Mínimo: +/- 0.002 para metal e +/- 0.003 para plástico
Tolerâncias para diâmetro do furo:
Padrão: +/- 0.005
Mínimo: +/- 0.001 para metal e +/- 0.002 para plástico
Tolerâncias para planicidade, excentricidade, cilindricidade, perpendicularidade e outras geometrias:
Padrão: +/- 0.005
Mínimo: +/- 0.001, dependendo da geometria
As tolerâncias acima não se aplicam ao usinar conjuntos soldados ou placas com menos de 1/4 "grosso e maior que 20" espesso, ou 1/8 "grosso com mais de 10" comprimento. Nesses casos, a equipe MFG precisará revisar as tolerâncias.
CNC Milling is a subtractive manufacturing process whereby material is trimmed from the origin to create a finished component. Our standard surface finish is 63 para 125 Rms. No entanto, we can grind or polish the part to between 4 e 8 Rms.
Shot blasting
Electropolished
Heat treatment
Sandblasting
Steam polishing
Advantage
Send us your 3D CAD data by email, indicate the specifications of your project and we will present you with a personalized quote in less than 24 horas
Girando, dual revolver lathe with rotary machining, 3-, 4- and 5-axis machining, stress attenuation / heat treatment, Soldagem, anodizing and powder coating
CNC machined parts in as little as 6-8 dias úteis (dependendo da geometria)
Dedicated project managers to help you throughout the entire process
Contate-nos
Aguardando seu e-mail, responderemos dentro de 12 horas com informações valiosas que você precisava.