O que é fundição de alta pressão? Custo do produto e preço de peças fundidas fabricadas em massa
Fundição sob pressão de alta pressão (HPDC) é um processo de fundição para produção em série ou em massa. Ligas fundidas com baixo ponto de fusão são geralmente usadas para este.
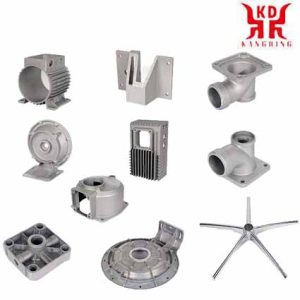
China Die Casting
Na fundição sob pressão, o líquido fundido é pressionado em um molde de fundição sob pressão (molde de fundição, cavidade) sob alta pressão de aprox.. 10 para 200 MPa e com uma velocidade de enchimento de molde muito alta de até 12 eu / é, onde então se solidifica. A coisa especial sobre o processo de fundição sob pressão é que com um molde permanente, ou seja. H. sem modelo. Como resultado, o molde é produzido apenas uma vez para uma série de componentes idênticos, mas com um esforço de produção significativamente maior. Desta maneira, um alto rendimento é alcançado, especialmente em uma máquina de fundição sob pressão de câmara quente, na qual o recipiente de fundição e o pistão de fundição estão constantemente no fundido. In the case of alloys with a higher melting point, the cold chamber pressure casting process is used; the casting set is located outside of the metallic melt.
How does the high pressure casting process work?
No processo de fundição de alta pressão, metal fundido ou liga metálica é injetado no molde em alta velocidade e alta pressão.
Máquinas de fundição sob pressão horizontais de alta pressão garantem que a matriz esteja totalmente fechada. Eles são classificados de acordo com a quantidade de força de fixação que podem aplicar e podem variar de 550 para 5700 toneladas.
Dependendo do metal utilizado, a unidade de injeção que preenche o molde pode ser uma câmara quente ou uma câmara fria. Em fundição sob pressão em câmara quente, o metal é mantido dentro da própria máquina de fundição sob pressão, então ele é puxado para dentro da câmara e a ação do pistão de injeção o introduz no molde. These parts of the machine are always in contact with the molten metal.
No processo de câmara fria, o metal é primeiro derretido em um forno separado e transferido para um forno de retenção; então é derramado em uma câmara de enchimento e injetado no molde. offers a wide range of cold chamber high pressure casting machines.
Die casting competes with injection molding with plastics. Metallic materials have advantages in individual cases that secure the market for die-cast articles.
The most commonly used materials are
Alumínio (die-cast aluminum)
Zinc (die-cast zinc)
Magnesium (magnesium die-cast)
Silicon tombac
![]() Motor housing die casting |
![]() Street lamp die casting |
![]() Distribution box die casting |
Die-cast parts properties
Die-cast parts have smooth, clean surfaces and edges. Além disso, this method allows wall thicknesses to be thinner than other methods. With zinc, por exemplo, the parts can have a wall thickness of 1 mm and with aluminum of 1.4 milímetros, in exceptional cases even less than 1 milímetros.
The achievable tolerances are ± 0.05 to ± 0.15 milímetros, so that one speaks of an exact or finished casting. For large cast parts, no entanto, slightly larger tolerances are required.
It is possible to use parts made of other materials, como. B. sockets, threaded bolts or pins to be poured in. Internal threads are produced directly with rotatable steel cores, which can then be removed again later. In contrast to other processes, the casting is called “shot” here. It is possible to carry out up to 1000 shots per hour (depending on the size of the machine). Depending on the casting material, the mold life is up to 2,000,000 shots (zinc alloys).
With aluminum, service lives of approx. 80,000 para 200,000 shots are achieved. Por muito tempo, die-cast aluminum was considered unsuitable for fusion welding and heat treatment. In the meantime, extensive investigations have made it possible to manufacture die-cast aluminum that is suitable for fusion welding and heat treatment. The particularly low-warpage beam welding processes (electron beam and laser beam welding) should be emphasized here – for optimum strength properties. No entanto, for optimal results it is necessary and advisable to consider the requirements of the process when designing. Além disso, no entanto, die-cast aluminum can also be welded very well using friction welding processes such as friction stir welding.
Die casting machine
Die casting machines usually consist of a mold clamping unit that is used to open and close the die casting mold. Components of the mold clamping unit (also called the closing part) are:
a fixed machine plate (also called a fixed plate) to hold the fixed casting mold half and, in the cold chamber process, the casting set
a movable machine plate (also mobile plate) to accommodate the hydraulic ejector and the movable mold half
the four guide pillars on which the movable machine platen is guided
the toggle lever system (consisting of a cylinder plate (also called crosshead), short and long lever and cross head)
the lock cylinder
The liquid metal is pressed from the casting chamber into the mold with a casting piston. Depending on the type of machine used, a distinction is made between the warm and cold chamber processes. The casting piston is driven by the casting unit’s drive. The drive piston is usually acted upon by a hydraulic pressure accumulator. In some cases the plunger is driven electrically.
Die casting machine peripherals
The peripheral units work in the vicinity of the die casting machine. These are process engineering devices that are necessary for the automatic process to run.
Mold spray machine or manipulator for mold spray or fixed nozzles
Heating and cooling devices
Extraction devices
Dosing oven or ladle
Vacuum-assisted die casting process
The vacuum-assisted die-casting process with forced ventilation enables workpieces with little or no gas inclusions. The cavity and the filling chamber are evacuated at the start of casting, so that the air contained therein and the gases produced are sucked out during casting and so fewer or no air inclusions can form in the melt.
Die casting recompression
A similar effect is achieved here by high compression in the phase before the final solidification of the workpiece. Pores and air pockets are significantly reduced.
As during the solidification of the melt. h there is a jump in volume during the transition from liquid to solid, volume deficits inevitably occur in the interior of thick-walled components.
In order to compensate for this effect of liquid shrinkage, the so-called squeeze process can be used to compress the solidifying melt. For this purpose, the pulpy melt is compressed by means of a “squeeze pin” in the die casting mold in areas where a volume deficit is expected.
Die casting mold and tool
The die-casting tools required in the die-casting process are manufactured in the tool shop or in the mold shop. Special materials or high-strength hot-work steels in accordance with DIN EN ISO 4957 are usually used as the material for the casting molds. A selection is shown in the following table.
Short material name | Material number |
32CrMoV 12-28 | 1.2365 |
X37CrMoV 5-1 | 1.2343 |
X40CrMoV 5-1 | 1.2344 |
Die casting phase sequence
Na fundição sob pressão, a pre-tempered (100 para 300 graus Celsius) permanent mold (two or more parts) is filled with molten metal under pressure at high speed. The actual casting process can be divided into three phases.
The pre-filling phase is used to convey the melt in the casting chamber up to the gate. The air compressed in the sprue system during the first phase can escape through ventilation channels and through the molding plane due to the relatively low speed of the piston (0.05–0.7 m / é).
During the mold filling phase, the casting piston presses the melt into the mold at a very high speed (0.4–6 m / é). The mold filling time is extremely short at 5–60 ms. It is therefore practically impossible to vent the mold.
In the holding pressure phase at the end of the mold filling, a very high static final pressure is built up. The air trapped when the mold is filled is compressed and the cast part is replenished.
Casting pressure
Different casting materials each require a different casting pressure. Aluminum and magnesium alloys are cast at 300–1200 bar, zinc at 130–250 bar and brass at 300–1000 bar. The strength of a workpiece is greater at high casting pressure.
![]() Surface treatment of die castings |
![]() Fundição sob pressão da carcaça do radiador |
![]() Die casting of meat grinder shell |
Shrinkage behavior of aluminum-silicon melts
If you pour liquid aluminum at about 700 ° C into a mold cavity in such a way that the mold is exactly filled, then the volume of the metal decreases to room temperature by a total of about 1.3% due to its contraction. Of this total, 0.05% is due to the liquid contraction, 0.75% to the solidification and 0.5% to the solid contraction.
This volume deficit of 1.3%, which is not much smaller with aluminum alloys than with pure metal, becomes noticeable in the solidifying cast part in the form of volume defects. In addition to normal shrinkage, these defects occur partly as sink marks, partly as macro-blowholes or as shrinkage pores.
The shrinkage cannot take place as unhindered in a die casting mold as it is in a sand casting mold, por exemplo. In foundry technology, the term “encolhimento” means, in addition to a process, a measure, namely the percentage dimensional deviation of the cooled casting from the dimensions of the mold at operating temperature. Whether shrinkage can take place freely or with hindrance depends almost exclusively on the geometric shape of the cast part. It is therefore possible that the shrinkage rate of 0.5% that is generally used today can be used for many dimensions on one and the same cast part, while 0.4% could still be too much for other areas. The mold dimensions are to be determined taking into account a shrinkage drawing of the die-casting alloys concerned.
Shrinkage for die casting
Die-cast alloy | Shrinkage in% |
Aluminum alloys | 0,5–0,7 |
Magnesium alloys | 0,5–0,8 |
Zinc alloys | 0,4–0,6 |
Influence of the alloying elements in aluminum casting alloys
Silicon
estrutura
With 12.5% silicon, aluminum forms a eutectic1 that melts at 577 ° C. In the binary system there is no connection between aluminum and silicon. The solubility of silicon in solid aluminum is 1.65% in equilibrium at 577 ° C., drops to 0.22% at 300 ° C. and even further at lower temperatures. If an alloy has more silicon than the solubility corresponds, the structure contains not only aluminum mixed crystals but also silicon crystals. If the cooling rate is not particularly fast, the silicon solidifies in the eutectic mixture in the form of angular crystals, needles and plates. These forms of training are made possible by small admixtures of z. B. sodium, strontium, antimony or phosphorus influenced. Die casting causes similar effects due to the rapid solidification.
Eutectic1 is a mixture of alloying elements, which of all possible compositions has the lowest melting point. The eutectic point, e.g. Por exemplo .: an Al-Si alloy, is 12.5% e 577 ° C.
Casting properties
The higher the Si content, the more advantageous it has on the flow and mold filling capacity. The flowability deteriorates as the Si content decreases.
Influence of silicon on the feeding behavior
With an increasing Si content, over 11%, the macro-void volume increases sharply. The incidence volume runs in the opposite direction to the macro void volume. With less than 9% Si, thick-walled parts tend to have suction cavities. The feeding options for macro-blowholes are limited in die casting (thick-walled cast parts lying from the gate cause some problems, since accumulations of material during the shot are filled last and then solidify). In hypoeutectic alloys, coarse grain becomes noticeable as a result of overheating from suction points.
A near-eutectic melt (around 11% Si) causes stronger macro-voids. Eutectic and near-eutectic Al-Si melts, which lead to a “granular” or “refined” structure, solidify with the formation of a peripheral shell (exogenous solidification), so that these melts are not susceptible to sucking holes.
ferro
A higher iron content has a positive effect on die casting (e.g., alloy EN AC-AlSi9Cu3 (Fe) máx.. 1.2%), as it reduces the tendency of the metal to stick to the mold surface. Within the tolerance limits, iron normally has no influence on the casting properties. Unintentional increase due to improper melting or working methods in the foundry can lead to embrittlement of the cast parts and undesired formation of cavities, hot cracks or sink marks. At low holding and pouring temperatures, gravity segregations often occur, which collect on the floor of the furnace. The segregation products consist of iron, manganese and silicon. The hardness of segregation products is 500–1000 Vickers.
cobre
Copper additives reduce the solidification shrinkage. Como resultado, copper-containing Al alloys permit pressure-tight castings more easily. Cu additives have a positive influence on strength and machinability. Copper reduces the corrosion resistance.
manganese
Manganese addition of a few tenths of a% reduces the negative influence of iron on elongation and impact resistance. No entanto, if iron and manganese occur in a higher content, they can under unfavorable melting conditions, e.g. B. by low holding temperatures, lead to hard segregation.
magnésio
With the simultaneous presence of silicon, copper or zinc, magnesium leads to an improvement in machinability due to an increase in hardness. Magnesium has no negative influence on the corrosion behavior. Magnesium is also becoming more and more interesting in the automotive industry, especially because of its lower weight.
nickel
The most important advantage of the addition of nickel is the increase in heat resistance. Pistons and cylinder heads in particular are the main areas of application for nickel-containing aluminum alloys.
zinco
Different zinc content within the tolerance limits are generally without any influence. Na fundição sob pressão, the Zn content together with magnesium is occasionally reduced in parts prone to hot cracks.
titânio
Titanium is added to Al alloys mainly as a grain refiner up to a maximum of 0.15%. In the case of sand and permanent mold casting alloys, it is a grain-refining alloy component.
liderar
In the solid state, lead is undissolved in the form of fine droplets. Within the tolerance limits (<0.1%), Pb does not noticeably influence the alloy properties.
lata
With a content of more than 0.02%, tin separates along the grain boundaries and has a very negative effect on hot cracking behavior if the normal tolerance is exceeded – especially in die casting.
Comparison of die casting and injection molding
The investment costs for casting machines and the high manufacturing costs for the mold are roughly comparable. In both processes, large numbers of pieces have to justify these high investment costs. After that, the raw material costs have priority.
Die-cast metal components have a significantly higher flexural strength (rigidity) than injection-molded ones; it can be up to 20 times higher. The workpieces produced in die casting can still be subjected to loads at higher temperatures (aluminum up to approx. 450 ° C). In the case of injection-molded materials, the strength and rigidity decrease sharply at higher temperatures (from 100 ° C); the only exceptions are expensive special plastics. Another advantage is that when the components (with the exception of zinc) are stressed, there is no creep, as is the case with many injection-molded workpieces. Die-cast parts have a much better structural stability, ou seja. a mechanically processed surface remains a surface, whereby the surface of a plastic part deforms much more easily. Além disso, some injection-molded plastics change shape under climatic conditions. Die-cast materials have electromagnetic shielding and are resistant to organic solutions. Além disso, recycling is possible without any loss of quality.
Injection molded components are cheaper if standard materials are used. Além disso, color can be used for injection molding. Another advantage is the lower weight compared to die-cast workpieces. The latter also have poorer corrosion properties. Além disso, the production of die-cast metal components is more complex and “complicated” geometries are sometimes not possible.