A usinagem de precisão CNC inclui principalmente torneamento fino, muito chato, fresagem fina, processos de moagem fina e moagem:
(1) Torneamento fino e mandrilamento fino: A maior parte da liga leve de precisão (liga de alumínio ou magnésio, etc.) as peças da aeronave são processadas principalmente por este método. Geralmente, natural single crystal diamond tools are used, and the radius of the blade arc is less than 0.1 mícrons. Machining on a high-precision lathe can obtain an accuracy of 1 micron and a surface unevenness with an average height difference of less than 0.2 mícrons, and the coordinate accuracy can reach ±2 microns.
Machining and grinding of non-standard steel, Liga, aço inoxidável: pistons, turbine sleeves, fixed sleeves, spacer rings, washers, shaft mounts, metal gears, piston cylinders (blackening/phosphating)
![]() Precision piston grinding |
![]() Tratamento de galvanização da manga da turbina |
![]() Blackening and phosphating of the fixed sleeve |
![]() Spacer ring, washer |
![]() Shaft fixing seat |
![]() Metal gear |
(2) Fine milling: used to process aluminum or beryllium alloy structural parts with complex shapes. Rely on the precision of the machine tool’s guide rail and spindle to obtain high mutual position accuracy. High-speed milling using a finely ground diamond head can obtain a precise mirror surface.
(3) Fine grinding: used for machining shaft or hole parts. Most of these parts are made of hardened steel, which has high hardness. Most high-precision grinding machine spindles use static pressure or dynamic pressure liquid bearings to ensure high stability. The ultimate accuracy of grinding is not only affected by the rigidity of the machine tool spindle and bed, but also related to the selection and balance of the grinding wheel, and the machining accuracy of the center hole of the workpiece. Fine grinding can obtain a dimensional accuracy of 1 micron and an out-of-roundness of 0.5 micron.
(4) Grinding: Use the principle of mating parts to selectively process irregular convex parts on the processed surface. Abrasive particle diameter, cutting force and cutting heat can be precisely controlled, so it is the highest precision machining method in precision machining technology. The hydraulic or pneumatic fittings in the precision servo parts of the aircraft, and the bearing parts of the dynamic pressure gyro motor are all processed in this way. To achieve an accuracy of 0.1 or even 0.01 microns and a microscopic unevenness of 0.005 mícrons.
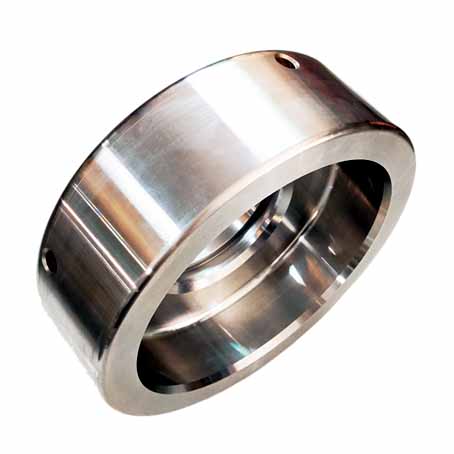
CNC machining of piston cylinder