Since the machining center is generally developed on the basis of a milling machine, it can be called a gantry milling machine machining center, and it is customarily referred to as a gantry machining center for short. The gantry machining center is currently one of the most widely used CNC machine tools in the world. Its main features are:
(1) On the basis of CNC boring machine or CNC machine tool, a self-internal tool changer is added, so that after one-time clamping of the workpiece, continuous processing of the workpiece surface can be completed continuously, and the process is highly concentrated.
(2) Geralmente, it is equipped with an automatic indexing rotary table or headstock, que pode girar automaticamente o ângulo. Por isso, depois que a peça de trabalho é fixada uma vez, o processamento multiprocesso de vários planos ou múltiplas posições angulares é concluído automaticamente.
(3) O centro de usinagem do pórtico pode alterar automaticamente a velocidade do fuso, taxa de avanço e o caminho do movimento da ferramenta em relação à peça de trabalho e outras funções auxiliares.
(4) Se o centro de usinagem pórtico possuir mesa de troca, a peça está sendo processada na mesa enquanto as outras peças são carregadas e descarregadas na mesa na posição de carga e descarga sem afetar o processamento normal da peça.
Acima estão as características comuns dos centros de usinagem CNC de pórtico. Aproveitando esta oportunidade, partindo das características do centro de usinagem pórtico CNC, I will give you a detailed introduction to the processing procedures for large parts.
(1) The use of equipment implements a fixed-person-specific mechanism, requiring the operator to operate the equipment with an operating certificate. When large-scale equipment is operated by multiple people, a special person must be instructed.
(2) The operator should be familiar with the main technical performance, estrutura, maintenance content and finishing standards of the equipment used.
(3) Preparation before work:
um. Check the equipment’s transmission system, operating system, lubrication system, pneumatic system, various switch starting positions, safety brake protection device, electric power stabilizing system and electrical instructions. The above-mentioned systems must be uniform, correct, sensitive, reliable and complete. As peças periféricas apertadas e as peças de conexão não devem ser afrouxadas.
b. Lubrifique de acordo com a tabela de lubrificação do equipamento.
c. Execute manualmente o eixo principal e cada eixo servo em baixa velocidade.
D. De acordo com a planilha do programa de processamento de peças, verifique se o valor de compensação da ferramenta e a posição de deslocamento do ponto chave na tabela de memória do sistema CNC estão errados. O valor de compensação da ferramenta e o valor de deslocamento zero devem ser consultados para verificar se estão corretos.
E. Ao usar fita de papel para inserir, verifique sempre se a fita de papel utilizada não está danificada e se o leitor fotoelétrico está normal.
F. As especificações dos parafusos T usados para peças circunferenciais apertadas devem ser consistentes com as especificações da ranhura T da tabela do equipamento. A força de aperto deve ser moderada. It is forbidden to add force to correct parts in all parts of the equipment.
G, Check whether the precautions specified in the “Machine Tool Manual” are followed.
(4) After the power is turned on, the inspection items before work:
Press the NC device power start key “ON”, the initial position coordinates of the machine tool will appear on the CRT display. Check the total pressure gauge installed on the upper part of the machine tool. If the gauge reads “4MPa”, it indicates that the system pressure is normal and formal operation can be performed.
(5) The correct operation steps at work are as follows:
A. Use it reasonably and operate it correctly according to the equipment manual. It is forbidden to use over load, over performance and over standard.
B. During the first programming trial processing, the operator must cooperate closely with the programmer. After confirming that the program is correct, it can be transferred to formal processing.
C, When installing the tool, wipe clean the handle and spindle taper hole and positioning.
D. Workpieces and tools must be installed securely. Prevent collisions with the machine when loading and unloading workpieces. Heavier parts and fixtures should be loaded and unloaded by crane or with the assistance of others.
E. During the processing, the operator is not allowed to leave the post or entrusted to take care of it, and cannot do anything irrelevant to the work. To leave the job temporarily, aperte o “Pause” button. To use the “emergency stop switch” correctly, it is strictly forbidden to switch off the power at will during work.
F. It is forbidden to place tooling, measuring tools, stacking parts and irrelevant objects on the guide rail surface and work surface of the equipment. Lin is forbidden to step on the protective cover, and shoes with metal nails are not allowed to step on the work surface.
G, Pay attention to abnormal phenomena during the operation of the equipment, stop in time when a failure occurs, take measures, and record and display the content of the failure. In the event of an accident, stop and cut off the power immediately, protect the scene, report to it in time, and not cover it up, and cooperate with the competent authority to conduct analysis and investigation.
(6) Maintenance after work.
um. The operator should clean up the chips and debris on the equipment in time, organize the work site, and do a good job of maintenance.
b. After the equipment has been maintained, the operator should move the switches and parts of the equipment back to their original positions. Each workbench is protected by oil, and the power supply is cut off in the prescribed order.
c. Exchange in accordance with the regulations on shifts and keep records.
Because the machining center has the above-mentioned functions and strict operating procedures, it greatly reduces the workpiece clamping measurement and the high-speed adjustment time of the machine tool and the turnover, handling and storage time of the workpiece, making the cutting time utilization rate of the machine tool 3-4 times higher than that of the ordinary machine tool. Thereby improving productivity, especially when processing workpieces with complex shapes, high precision requirements, and a complicated variety of replacement periods, é mais econômico.
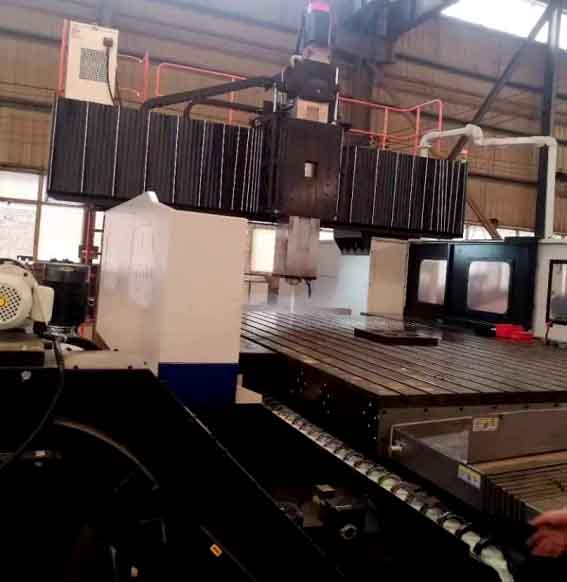
Processing characteristics of CNC gantry machining center