Fresagem de plástico facilitada!
Se você deseja fresar plástico para fazer modelos, para o seu hobby ou no trabalho, you can quickly run into some problems when processing the soft material.
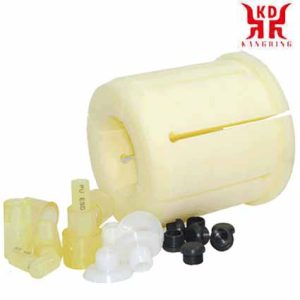
Moinho de peças plásticas
Por exemplo, if the machining parameters are incorrectly selected, the heat build-up can quickly result in melted edges on your workpieces.
Warpage is also a common problem when machining plastic components.
This article answers the following questions:
Which plastics can be processed?
How can you clamp plastic workpieces?
What are the 7 most important points to consider when milling plastic?
What do you have to pay particular attention to when milling plastic?
What is important when milling plastics
1. The sharpness of the plastic cutter
The sharpness of the cutter is very important, as a blunt cutter leads to the melting of the material and thus to unclean cut edges.
It is best to use special milling cutters for milling plastic.
You are best advised to use a milling cutter for aluminum, as it is filigree and precise and does not lead to heat development due to the good cutting edge.
I have had the best experiences with new single-flute milling cutters. But then I only use this for plastics and never for metals, so that the cutting edge does not wear out.
2. The correct cutting speed
The working speed also has a significant influence, so that fast milling generates less heat than if you slowly smear through the material with the milling cutter. The reason is that if the cutting speed is too low, the chip will no longer be cut properly but will be torn off.
The working speed also has a significant influence, so that fast milling generates less heat than if you slowly smear through the material with the milling cutter. The reason is that if the cutting speed is too low, the chip will no longer be cut properly but will be torn off.
The heat input into the base material can be reduced by suitable cooling (e.g. drilling emulsion or compressed air cooling).
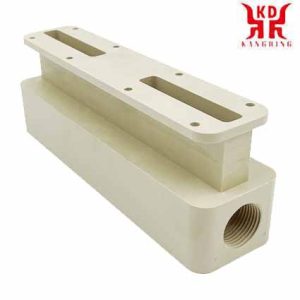
Machining of PEEK parts
7 important points for the machining of plastics:
You may know it: You have just finished milling a plastic component on your milling machine with the correct cutting parameters, unclamped it and the part is already warping after it has been removed from the CNC machine. A good knowledge of the material properties, the use of suitable tools and the correct work preparation can help you at this point.
Melting temperature
Take the melting temperature of thermoplastics into account (approx. 150 ° C). Use the correct cutting data and milling cutter for this. To help you find a PDF from Licharz here: Help for the selection of milling cutters when milling plastics.
cooling
Cooling with compressed air or drilling emulsion reduces temperature-related problems.
clamping:
To keep plastic sheets tension-free, it is best to clamp them with a vacuum. Alternatively, the semi-finished plastic product can be glued to a stiff plastic sacrificial plate with good double-sided adhesive tape (e.g. Tesafix 4959).
The sacrificial plate can then be milled and is simply replaced the next time it is used.
Completely support the plastic on the support, otherwise it will bend during processing.
Tool choice
Use only very sharp tools (single or double-edged).
Deburring
When milling plastics, there is often an unsightly burr, which can most easily be removed with a sharp deburring knife.
Delay:
Similar to sheet steel, plastic sheets can also warp after processing. The reason is that extruded plastic sheets have internal stresses. If one side is now milled over, the tensions are released and the plate arches.
This can be avoided by prior tempering or by a sufficient allowance before machining and a subsequent finishing process to compensate for the curvature.
In the case of panels, reciprocal processing often helps.
Semi-finished panes made from round material are generally less prone to warping than whole plastic panels.
The panels should also be processed at room temperature, ou seja. after they have been brought out of the cold store in winter, allow them to warm up first.
Bless you:
When machining fiber-reinforced plastics, the finest fibers can get into the lungs and lead to permanent health problems. Please take suitable safety measures (suction, encapsulation …).
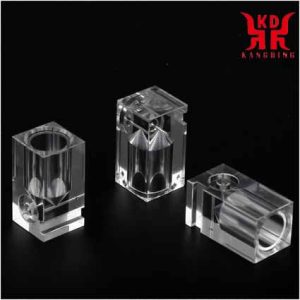
Usinagem de peças acrílicas
Which plastics can be milled?
Plastic is not just plastic. There are major differences in the density of the material that affect the machining of plastic.
Common plastics that are milled are POM, PA, PP, PS, PET, PTFE and the high-performance plastic PEEK. Fiber-reinforced plastics are also often processed in model making.
The higher the melting temperature or the heat capacity of the plastic, the better it will tend to be processable.
PEEK has the lowest temperature influence of the plastics I know. With its high melting temperature and low thermal expansion compared to other thermoplastics, PEEK can be processed comparatively well.
Example video for the machining of acrylic (Plexiglas or PMMA)
A sharp milling cutter is the be-all and end-all when milling plastics! If you have problems with melted cutting edges, try to adjust your cutting speed and use a drilling emulsion for cooling. You can counteract warpage by tempering beforehand or by purchasing round material. The clamping of your workpiece should also be as tension-free as possible.
And again: use a new sharp cutter!