Os principais materiais de liga para fundição sob pressão são o estanho, liderar, zinco, alumínio, magnésio, cobre, aço inoxidável, etc.. As ligas de zinco e alumínio são as mais utilizadas, seguido por ligas de magnésio e cobre. Atualmente, zinco, ligas de alumínio e magnésio são usadas principalmente na indústria eletrônica.
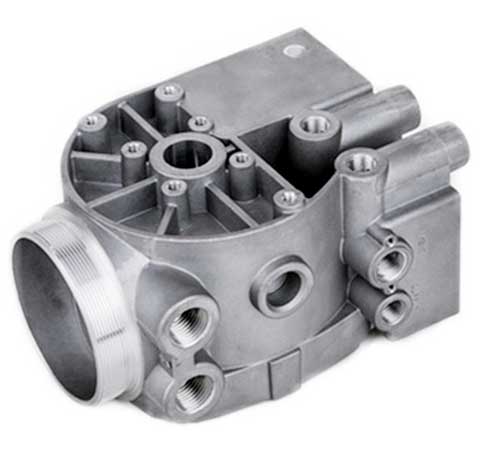
fundição de carcaça de motor
Die-cast zinc alloy
The molten state of zinc alloy is very fluid, with a low melting point of only 365 graus. Various post-processing treatments such as electroplating can be performed, so it is widely used. It was also used a lot in the mobile phone industry before, but because of its large specific weight and poor corrosion resistance, it was gradually eliminated by aluminum alloys. The most used is the bathroom industry. Commonly used are 2, 3, 4, 5, 7 zinc alloys, and the most widely used is 3 zinc alloys.
Die-cast aluminum alloy
Aluminum alloy has low density, but relatively high strength, close to or surpassing high-quality steel, good plasticity, and can be processed into various profiles. It has excellent electrical conductivity, thermal conductivity and corrosion resistance, and is widely used in industry, second only to steel. The specific weight of aluminum alloy is only about 1/3 of that of iron, so it is very important in all walks of life, especially in the lightweight process of aircraft, ships, automóveis, and electronic instruments.
Commonly used are Al-Si-Cu system, common ADC12 (A383), ADC10 (A380) e assim por diante. Além disso, there are Al-Si series, Al-Si-Mg series, and Al-Mg series. Also known as aluminum-titanium alloy, it is improved by adding titanium metal to the above-mentioned materials. Adding titanium metal can significantly improve the mechanical properties of the product.
Die-cast magnesium alloy
Magnesium alloys are alloys composed of magnesium-based and other elements. Its characteristics are:
Low density, high specific strength, large specific elastic modulus, good heat dissipation, good shock absorption, higher impact load capacity than aluminum alloy, and good corrosion resistance to organic substances and alkalis. The specific gravity of magnesium is about 2/3 that of aluminum and 1/4 of that of iron. Portanto, it is widely used in electronic equipment such as mobile phones, communication equipment, peças automotivas, and medical equipment.
The most widely used are magnesium-aluminum alloys, followed by magnesium-manganese alloys and magnesium-zinc-zirconium alloys. The commonly used grades are AZ91D, AM60B, AM50A, AS41B and so on.
Die casting mold
Die-casting molds must be made of hot work mold steel. Commonly used steels are: H13, 2344, 8407, 8418, SKD61, DAC, FDAC, etc..
Mold structure: (rear mold, front mold) mold base, mold core, guide post, guide sleeve thimble, cylinder, shunt, gate sleeve, slider, inclined guide post, hydraulic core pulling.
Mold processing equipment: milling machine, Centro de usinagem CNC, corte de fio (slow wire), (mirror) spark machine, grinding machine, lathe, welding repair equipment.