O programa de usinagem CNC ideal não deve apenas garantir que peças qualificadas em conformidade com os desenhos sejam processadas, mas também deve permitir que as funções da máquina-ferramenta CNC sejam razoavelmente aplicadas e totalmente utilizadas. A máquina-ferramenta CNC é um equipamento de automação altamente eficiente. Sua eficiência é 2 para 3 vezes superior ao das máquinas-ferramentas comuns. Portanto, para aproveitar ao máximo esse recurso das máquinas-ferramentas CNC, é preciso dominar seu desempenho, características, e métodos operacionais. Ao mesmo tempo, o plano de usinagem deve ser determinado corretamente antes da programação.
Devido à diferença na escala de produção, o plano de processamento para a mesma peça é diferente. De acordo com condições específicas, um plano de processo econômico e razoável deve ser selecionado.
(1) Divisão de procedimentos de processamento
O processamento de peças em máquinas-ferramentas CNC pode ser mais concentrado no processo, e todos os processos devem ser concluídos tanto quanto possível em uma configuração. Comparado com o processamento de máquinas-ferramenta comuns, a divisão dos procedimentos de processamento tem características próprias, e existem dois princípios comumente usados para divisão de procedimentos.
1. O princípio de garantir a precisão
O processamento de controle numérico exige que o processo seja concentrado tanto quanto possível, e muitas vezes o processamento bruto e fino é concluído em uma única fixação. A fim de reduzir a influência da deformação térmica e da deformação da força de corte na forma, precisão de posição, precisão dimensional e rugosidade da superfície da peça, usinagem de desbaste e acabamento devem ser realizadas separadamente. Para peças de eixo ou disco, a usinagem de desbaste será executada primeiro, deixando uma pequena margem para acabamento para garantir os requisitos de qualidade da superfície. Ao mesmo tempo, para algumas peças de caixa, a fim de garantir a precisão da usinagem do furo, a superfície deve ser processada primeiro e depois o furo deve ser processado.
2. Princípios para melhorar a eficiência da produção
Na usinagem CNC, a fim de reduzir o número de trocas de ferramentas e economizar tempo de troca de ferramentas, depois que todas as peças que precisam ser processadas com a mesma ferramenta forem concluídas, outra ferramenta deve ser usada para processar outras peças. Ao mesmo tempo, o curso ocioso deve ser minimizado. Ao processar múltiplas peças da peça de trabalho com a mesma ferramenta, a rota mais curta deve ser usada para chegar a cada parte do processamento.
Na prática, o processo de usinagem CNC deve ser considerado de forma abrangente de acordo com as características estruturais e requisitos técnicos de peças específicas.
(2) Determinação da rota de processamento
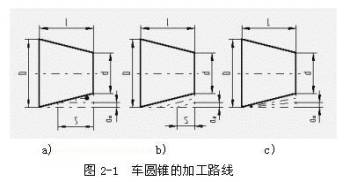
Rota de usinagem para torneamento de peças cônicas
Na usinagem CNC, o caminho do movimento e a direção da ferramenta (estritamente falando, o ponto de posição da ferramenta) em relação à peça é chamada de rota de usinagem. Aquilo é, o caminho que a ferramenta percorre desde o ponto de ajuste da ferramenta até o final do programa de usinagem, incluindo o caminho de corte e os cursos ociosos não cortantes, como introdução e retorno da ferramenta. The determination of the processing route must first ensure the dimensional accuracy and surface quality of the processed parts, and secondly consider the simple numerical calculation, the shortest possible tool path, and the higher efficiency.
The following examples analyze the commonly used machining routes when machining parts with CNC machine tools.
1. Analysis of machining route for turning cone
For turning the outer cone on the CNC lathe, assuming that the major diameter of the cone is D, the minor diameter is d, and the length of the cone is L, the machining route of the turning cone is shown in Figure 2-1.
According to the stepped cutting route in Figure 2-1a, two-cut rough turning, and the last one-cut fine turning; The final tool distance S of the two-cut rough turning must be accurately calculated, que pode ter triângulos semelhantes:
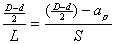
Projetar a rota de corte de peças escalonadas
Para este tipo de rota de processamento, a espessura do torneamento é a mesma para torneamento em desbaste, mas a espessura do torneamento é diferente para torneamento fino; Ao mesmo tempo, o caminho de corte da ferramenta é o mais curto.
De acordo com a rota de corte oblíqua semelhante na Figura 2-1b, também é necessário calcular a distância final da ferramenta S durante o torneamento em desbaste, que também pode ser calculado a partir de triângulos semelhantes:

O projeto do caminho mais curto do movimento de corte da ferramenta
De acordo com esta rota de processamento, a distância de corte da ferramenta é relativamente curta.
De acordo com a rota de processamento de linha oblíqua na Figura 2-1c, apenas a quantidade de ferramenta traseira ap é determinada a cada vez, em vez de calcular a distância final da ferramenta, a programação é conveniente. No entanto, the thickness of each cutting changes, and the cutting path of the tool is longer.
2. Analysis of machining route of turning arc
Use G02 (or G03) command to turn arc. If the arc is processed by turning once, the amount of knife is too large and it is easy to hit the knife. Portanto, in the actual turning of arcs, multi-cutting is required, and a large amount of excess is removed first, and then the required arc is turned.
The following describes the common machining routes of turning arcs.
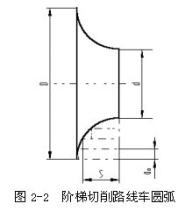
Turning arc for designing step cutting route
Figura 2-2 shows the step cutting route of turning arc. Aquilo é, first rough turning is made into steps, and the arc is cut out with the final cut. In this method, after the turning thickness ap is determined, the final tool distance S of rough turning must be calculated accurately, aquilo é, o ponto de intersecção do arco e a linha reta é calculado. In this method, a distância do movimento de corte da ferramenta é menor, mas o cálculo numérico é mais complicado.
Figura 2-3 mostra a rota de corte do arco concêntrico do arco de giro. Aquilo é, girando com círculos de raios diferentes, e finalmente processando o arco necessário. Este método é mais fácil de determinar as coordenadas do ponto inicial e final do arco de 90° após determinar a quantidade ap de cada ferramenta. O cálculo numérico é simples, e a programação é conveniente, então é frequentemente usado. Mas ao processar de acordo com a Figura 2-3b, o tempo de curso ocioso é maior.
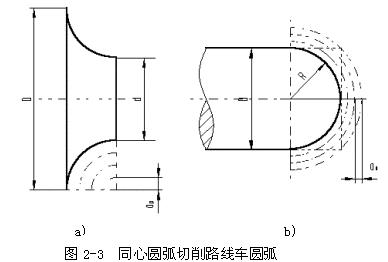
Projetar um arco de trajetória de corte de arcos concêntricos
Figura 2-4 mostra a rota de corte do método do cone de torneamento para arcos de torneamento. Aquilo é, primeiro girando um cone, e então girando o arco. No entanto, deve-se notar que se o ponto inicial e o ponto final do cone não forem bem determinados, a superfície do cone pode ser danificada, ou a margem pode ficar muito grande. O método de determinação é mostrado na Figura 2-4. Conecte OC para cruzar o arco em D, e faça a tangente AB do arco que passa pelo ponto D.
Da relação geométrica CD=OC-OD= -R=0,414R, esta é a tolerância máxima de corte ao tornear cônico, aquilo é, ao virar cônico, a rota de processamento não pode exceder a linha AB. De acordo com a relação mostrada na figura, AC = BC = 0,586R pode ser obtido, para que o ponto inicial e o ponto final do cone possam ser determinados. Quando R não é muito grande, AC=BC=0,5R pode ser tomado. O cálculo numérico deste método é complicado, e o caminho de corte da ferramenta é curto.
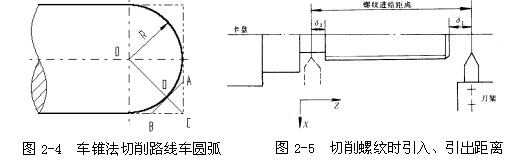
Turning the arc with the cutting path of the turning cone method
3. Analysis of Axial Feeding Distance When Turning Thread
When turning the thread, the feed of the tool along the thread direction should maintain a strict speed ratio relationship with the rotation of the workpiece spindle. Considering that the tool reaches the specified feed rate from the stopped state or drops from the specified feed rate to zero, the drive system must have a transition process. The length of the processing route along the axial feed, in addition to ensuring the thread length, should also increase the tool lead-in distance of δ1 (2~5mm) and the tool cutting distance of δ2 (1~2mm), como mostrado na figura 2-5 . This is to ensure that when cutting threads, the tool will contact the workpiece after the speed increase is completed, e a ferramenta irá desacelerar depois de sair da peça de trabalho.
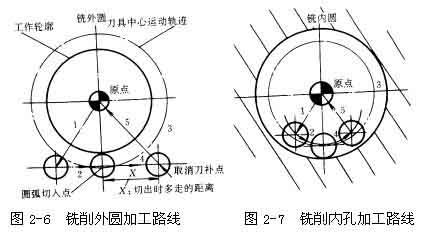
A rota de usinagem do círculo externo da peça fresada
4. Análise da rota de processamento de fresamento de contorno
Para contornos de fresamento contínuo, especialmente ao processar arcos, preste atenção à disposição de entrada e saída da ferramenta, e tente evitar processamento repetido na junção, caso contrário, haverá marcas de fresagem limite óbvias. Como mostrado na figura 2-6, ao usar interpolação circular para fresar um círculo externo, organize a fresa para entrar no processo de fresamento circunferencial a partir da direção tangencial. Depois que todo o círculo for processado, não retraia a ferramenta diretamente no ponto tangente, mas deixe a ferramenta se mover por uma certa distância. É melhor seguir a direção tangencial para evitar colisão entre a ferramenta e a superfície da peça quando a compensação da ferramenta for cancelada, fazendo com que a peça de trabalho seja descartada. Ao fresar arcos internos, o princípio de corte na direção tangencial também deve ser observado, e os arcos de transição devem ser organizados para cortar e cortar, como mostrado na figura 3-7. Se a ferramenta partir da origem da coordenada da peça, sua rota de processamento é 1→2→3→4→5, de modo a melhorar a precisão e a qualidade da usinagem da superfície interna do furo.
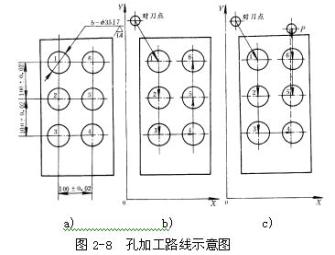
Projetar a rota de usinagem do furo da peça
5. Análise da rota de usinagem de furos com alta precisão de posição
Para usinagem de furos que requer alta precisão na exatidão da posição, special attention should be paid to the arrangement of the hole processing sequence. Improper arrangement may bring in the backlash along the coordinate axis and directly affect the position accuracy. Como mostrado na figura 2-8, Figure a is a part drawing. There are two processing routes for six holes of the same size processed on this part. When machining according to the route shown in figure b, the positioning direction of holes 5 e 6 is opposite to that of holes 1, 2, 3 e 4. The reverse clearance in the Y direction will increase the positioning error and affect the position accuracy of holes 5 e 6 and other holes. According to the route shown in Figure c, after processing 4 holes, move up a distance to point P, and then turn back to process 5 e 6 holes. Desta maneira, the direction is consistent, which can avoid the introduction of backlash and improve the position accuracy of holes 5 e 6 and other holes.
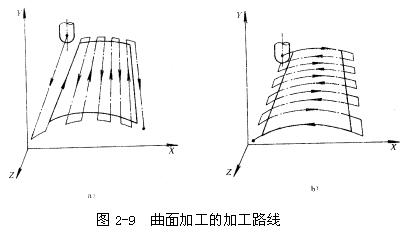
Design the processing route of the part surface
6. Analysis of the processing route of milling surface
When milling a curved surface, a ball-end knife is commonly used for processing with the “wire cutting method”. The so-called wire cutting method means that the tangent track of the tool and the part contour is line by line, and the distance between the lines is determined according to the requirements of the machining accuracy of the part. For surface machining with open boundaries, two machining routes can be used. Como mostrado na figura 2-9, for large engine blades, when the processing scheme of Figure 2-9a is used. Each time it is processed along a straight line, the calculation of the tool position point is simple, the program is few, the processing process conforms to the formation of the ruled surface, and the straightness of the bus can be accurately guaranteed. When the processing plan shown in Figure 2-9b is used, the data of this type of part is in accordance with the information given for easy inspection after processing. The accuracy of the impeller shape is high, but there are many procedures. Because the boundary of the surface part is open, there are no other surface restrictions, so the boundary of the surface can be extended, and the ball-end knife should start processing from outside the boundary.
The above has analyzed the commonly used processing routes in CNC machining through several examples. In actual production, a determinação da rota de processamento deve ser baseada nas características estruturais específicas das peças, consideração abrangente e uso flexível. Os princípios gerais para determinar a rota de processamento são: Sob a condição de garantir a precisão da usinagem e a qualidade superficial das peças, encurte a rota de usinagem tanto quanto possível para melhorar a produtividade.