Product Categories
Product Tags
Choose the right tool for CNC machining parts
When finishing large parts, in order to ensure that at least one pass is completed and to avoid changing the tool in the middle of cutting, the tool life should be determined according to the accuracy of the part and the surface roughness. Compared with ordinary machine tool processing methods, CNC machining puts forward higher requirements on cutting tools. It not only requires good steel and high precision, but also requires stable dimensions, high durability, and easy installation and adjustment for breaking and discharging performance, so as to meet the high efficiency requirements of CNC machine tools.
The principle of choosing CNC tools
Tool life is closely related to cutting volume. When formulating cutting parameters, a reasonable tool life should be selected first, and the reasonable tool life should be determined according to the optimization goal. Generally divided into the highest productivity tool life and the lowest cost tool life, the former is determined according to the goal of the least single-piece labor hours, and the latter is determined according to the goal of the lowest process cost.
The following points can be considered when choosing the tool life according to the complexity of the tool, manufacturing and sharpening costs. The life of complex and high-precision tools should be higher than that of single-edge tools. For machine clamp indexable tools, due to the short tool change time, in order to give full play to its cutting performance and improve production efficiency, the tool life can be selected to be lower, generally 15-30min. For multi-tool machine tools, modular machine tools, and automated machining tools that are more complicated in tool installation, tool change, and tool adjustment, the tool life should be selected to be higher, especially to ensure the reliability of the tool. When the productivity of a certain machining process in the workshop limits the increase in the productivity of the entire workshop, the CNC tool life of this process should be selected lower. When the cost of the whole plant shared by a certain processing procedure per unit time is relatively large, the CNC tool life should also be selected lower.
When finishing large parts, in order to ensure that at least one pass is completed and to avoid changing the tool in the middle of cutting, the tool life should be determined according to the accuracy of the part and the surface roughness. Compared with ordinary machine tool processing methods, CNC machining puts forward higher requirements on cutting tools. It not only requires good steel and high precision, but also requires stable dimensions, high durability, and easy installation and adjustment for breaking and discharging performance, so as to meet the high efficiency requirements of CNC machine tools. The selected tools on CNC machine tools often use tool materials suitable for high-speed cutting (such as high-speed steel, ultra-fine-grained carbide) and use indexable inserts.
Control tool position
From where does the tool start to move to the specified position?
Therefore, at the beginning of the program execution, it is necessary to determine the starting position of the tool in the workpiece coordinate system. This position is the starting point of the movement of the tool relative to the workpiece when the program is executed, so it is called the starting point of the program or the starting point of the tool. This starting point is generally determined by tool setting, so this point is also called tool setting point. When compiling the program, choose the position of the tool setting point correctly. The principle of tool setting point is: Facilitate numerical processing and simplify programming. Easy to align and easy to check during processing; The processing error caused is small. The tool setting point can be set on the machined part, or on the fixture or on the machine tool. In order to improve the machining accuracy of the parts, the tool setting point should be set as far as possible on the design basis or process base of the part.
In actual operation of the machine tool, the tool position point of the tool can be placed on the tool setting point by manual tool setting operation, that is, the coincidence of “tool position point” and “tool setting point”. The so-called “tool location point” refers to the positioning datum point of the tool. The tool location point of the turning tool is the tool tip or the center of the tool tip arc. The flat-bottomed end mill is the intersection of the tool axis and the bottom of the tool; The ball end mill is the center of the ball end, and the drill bit is the drill tip. Manual tool setting operation has low precision and low efficiency. Some factories use optical tool setting mirrors, tool setting instruments, automatic tool setting devices, etc. In order to reduce tool setting time and improve tool setting accuracy. When the tool needs to be changed during processing, the tool change point should be specified. The so-called “tool change point” refers to the position of the tool post when it rotates to change the tool. The tool change point should be located outside the workpiece or fixture, and the workpiece and other parts should not be touched during tool change.
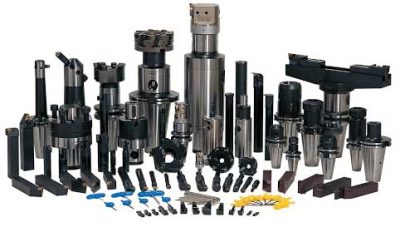
Classification and application of CNC machining tools
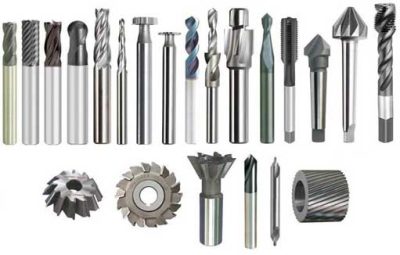
Machining high-speed steel tools

Machining titanium alloy tools
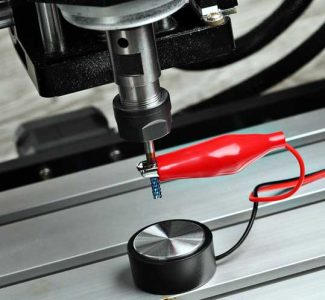
CNC machining tool setting
Contact Us
Waiting for your email, we will reply you within 12 hours with valuable information you needed.