Product Categories
Product Tags
Operational safety of CNC machining metal parts
CNC machine tools are advanced processing equipment with a high degree of automation and a more complex structure. In order to give full play to the superiority of machine tools, improve production efficiency, manage, use, and repair CNC machine tools, the quality of technical personnel and civilized production are particularly important. In addition to being familiar with the performance of CNC machine tools, operators must also cultivate good working habits and rigorous work styles in civilized production, and have good professional qualities, sense of responsibility and spirit of cooperation. The following should be done during operation:
Civilized production of CNC machining hardware parts
CNC machine tools are advanced processing equipment with a high degree of automation and a more complex structure. In order to give full play to the superiority of machine tools, improve production efficiency, manage, use, and repair CNC machine tools, the quality of technical personnel and civilized production are particularly important. In addition to being familiar with the performance of CNC machine tools, operators must also cultivate good working habits and rigorous work styles in civilized production, and have good professional qualities, sense of responsibility and spirit of cooperation. The following should be done during operation:
⑴ Strictly abide by the safe operation regulations of CNC machine tools. Do not operate the machine without professional training.
⑵ Strictly abide by the commuting and shifting system.
⑶ Use and manage the machine well, and have a strong sense of work responsibility.
⑷ Keep the environment around the CNC machine tool clean and tidy.
⑸ Operators should wear work clothes, work shoes, and no dangerous decorations.
Operating Regulations of CNC Machining Hardware Parts
In order to use CNC machine tools correctly and rationally, reduce the incidence of failures, and the operation methods. The machine tool can only be operated with the consent of the machine tool manager.
⑴ Precautions before turning on the CNC machine tool
1) The operator must be familiar with the performance and operation methods of the CNC machine tool. The machine tool can only be operated with the consent of the machine tool manager.
2) Before turning on the machine, check whether the voltage, air pressure, and oil pressure meet the working requirements.
3) Check whether the movable part of the machine tool is in a normal working state.
4) Check whether the workbench has an offside or limit state.
5) Check whether the electrical components are firm, and whether there is any wire off.
6) Check whether the ground wire of the machine tool is reliably connected to the ground wire of the workshop (especially important for the first startup).
7) Turn on the main power switch only after the preparations before starting the machine have been completed.
⑵ Precautions during the startup process of CNC machine tools
1) Operate strictly in accordance with the startup sequence in the machine tool manual.
2) Under normal circumstances, you must first return to the machine reference point during the startup process to establish a machine tool as a standard system.
3) After starting the machine, let the machine run dry for more than 15 minutes to make the machine reach a balanced state.
4) After shutting down, you must wait for more than 5 minutes before starting up again. If there is no special situation, do not start or shut down frequently.
⑶ Precautions for the debugging process of CNC machine tools
1) Edit, modify and debug the program. If it is the first piece of trial cut, dry run must be performed to ensure that the program is correct.
2) Install and debug the fixture according to the process requirements, and remove the iron filings and debris on each positioning surface.
3) Clamp the workpiece according to the positioning requirements to ensure correct and reliable positioning. Do not loosen the workpiece during processing.
4) Install the tool to be used. If it is a machining center, the tool position number on the tool magazine must be strictly consistent with the tool number in the program.
5) Perform tool setting according to the programmed origin on the workpiece to establish the workpiece coordinate system. If multiple tools are used, the remaining tools will be compensated for length or tip position respectively.
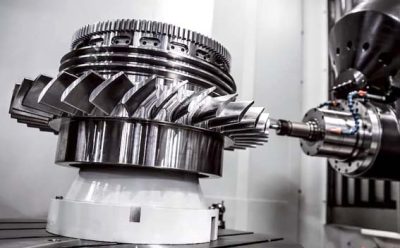
precision auto lathe machining hardware parts
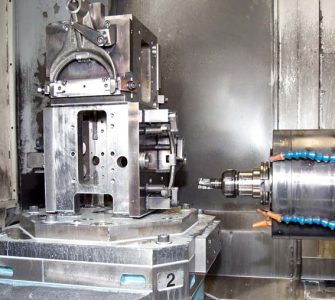
customized cnc turning milling hardware parts
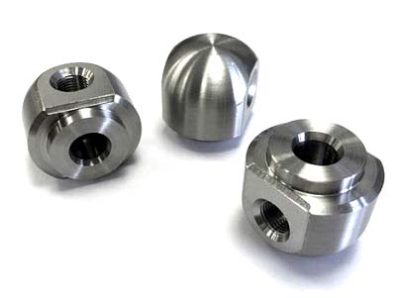
machining customization hardware parts
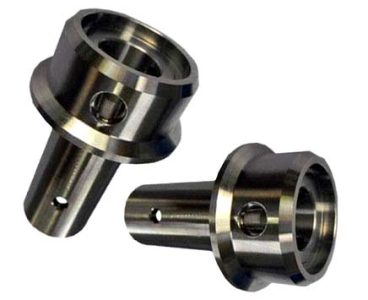
Understanding CNC Milling hardware Components
Contact Us
Waiting for your email, we will reply you within 12 hours with valuable information you needed.