Product Categories
Product Tags
Milling Machine and Milling Technology
Milling refers to the use of rotating multi-edge tools to cut workpieces, and is a highly efficient processing method. When working, the tool rotates (does the main movement), and the workpiece moves (the feed movement). The workpiece can also be fixed, but the rotating tool must also move (to complete the main movement and the feed movement at the same time). The machine tools used for milling are horizontal milling machines or vertical milling machines, as well as large portal milling machines. These machine tools can be ordinary machine tools or CNC machine tools. Use a rotating milling cutter as a cutting tool. Milling is generally performed on a milling machine or a boring machine. Suitable for processing plane, grooves, various molding surface (flower key, gear and thread) and special shaped surface of the mold and the like.
Milling is a machining method in which a milling cutter is used as a tool and the surface of an object is processed by CNC. Milling machines include horizontal milling machines, vertical milling machines, portal milling machines, profiling milling machines, universal milling machines, and bar milling machines.
What is milling?
Milling refers to the use of rotating multi-edge tools to cut workpieces, and is a highly efficient processing method. When working, the tool rotates (does the main movement), and the workpiece moves (the feed movement). The workpiece can also be fixed, but the rotating tool must also move (to complete the main movement and the feed movement at the same time). The machine tools used for milling are horizontal milling machines or vertical milling machines, as well as large portal milling machines. These machine tools can be ordinary machine tools or CNC machine tools. Use a rotating milling cutter as a cutting tool. Milling is generally performed on a milling machine or a boring machine. Suitable for processing plane, grooves, various molding surface (flower key, gear and thread) and special shaped surface of the mold and the like.
Features of milling tools
① Each tooth of the milling tool periodically participates in intermittent cutting.
② The cutting thickness of each milling cutter tooth changes during the cutting process.
③ The feed per tooth αf (mm/tooth) indicates the relative displacement of the workpiece within the time that the milling cutter rotates one tooth.
Common milled parts
(1) Flat parts
The characteristics of plane parts: the machined surface can be parallel to the horizontal plane, perpendicular to the horizontal plane, or a fixed angle with the horizontal plane;
Most of the parts processed on the CNC milling machine are flat parts, and the flat parts are the simplest type of parts in CNC milling. Generally, only two-axis linkage or 3-axis linkage of a three-axis CNC milling machine can be used for processing. In the processing process, the processing surface and the tool are in surface contact, and end milling cutter or ball end milling cutter can be used for rough and finishing processing.
(2) Special-shaped parts with curved surfaces
The characteristic of curved parts is that the machined surface is arc-shaped space curved surface. During the machining process, the machining surface and the milling cutter are always in point contact. Surface finishing is mostly carried out with ball-end milling tools.
Precision correction of milling machine
X-axis correction of milling machine
Slightly loosen the 4 bolts, but make sure that there is still some friction resistance on the 4 bolts. At this time, use the rotating bolt of the head to adjust the left and right angle. During the process, a dial indicator must be placed on the end of the spindle to measure the correct position of the worktable.
Y-axis correction of milling machine
Slightly loosen the 3 bolts, but make sure that the 3 bolts are not too loose to facilitate fine-tuning. At this time, by the arm rotating bolt, a dial indicator placed on the spindle end in order to measure the correct position of the table.
Horizontal correction of milling machine
Place the spirit level on the work surface.
Check point A and B of the level, the allowable value is 0.06mm/m.
If necessary, shims can be placed under the machine.
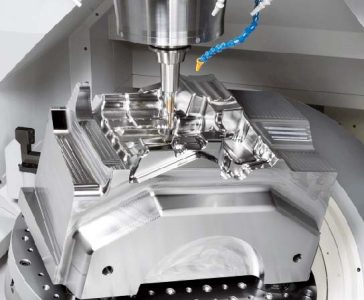
Horizontal milling machine milling large aluminum alloy parts

Features of milling cutter and feed amount αf
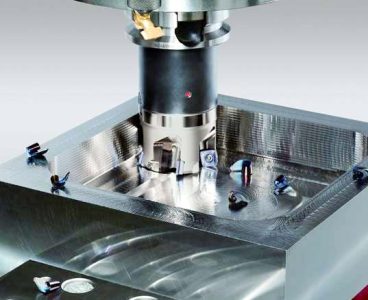
Milling curved parts and flat parts price calculation
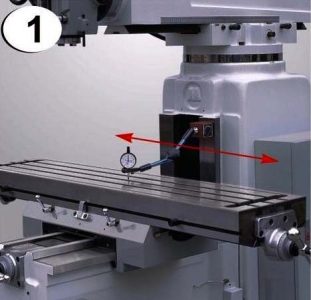
X, Y axis and horizontal correction of milling machine
Contact Us
Waiting for your email, we will reply you within 12 hours with valuable information you needed.