Omdat het bewerkingscentrum over het algemeen wordt ontwikkeld op basis van een freesmachine, het kan een bewerkingscentrum voor portaalfreesmachines worden genoemd, en het wordt gewoonlijk kortweg een portaalbewerkingscentrum genoemd. Het portaalbewerkingscentrum is momenteel een van de meest gebruikte CNC-bewerkingsmachines ter wereld. De belangrijkste kenmerken zijn:
(1) On the basis of CNC boring machine or CNC machine tool, a self-internal tool changer is added, so that after one-time clamping of the workpiece, continuous processing of the workpiece surface can be completed continuously, and the process is highly concentrated.
(2) Over het algemeen, it is equipped with an automatic indexing rotary table or headstock, which can automatically rotate the angle. Dus, after the workpiece is clamped once, the multi-process processing of multiple planes or multiple angular positions is automatically completed.
(3) The gantry machining center can automatically change the spindle speed, feed rate and the motion path of the tool relative to the workpiece and other auxiliary functions.
(4) If the gantry machining center has an exchange table, the workpiece is being processed on the table while the other workpieces are loaded and unloaded on the table in the loading and unloading position without affecting the normal processing of the workpiece.
The above are the common features of gantry CNC machining centers. Taking this opportunity, starting from the characteristics of the CNC gantry machining center, I will give you a detailed introduction to the processing procedures for large parts.
(1) The use of equipment implements a fixed-person-specific mechanism, requiring the operator to operate the equipment with an operating certificate. When large-scale equipment is operated by multiple people, a special person must be instructed.
(2) The operator should be familiar with the main technical performance, structuur, maintenance content and finishing standards of the equipment used.
(3) Preparation before work:
A. Check the equipment’s transmission system, operating system, lubrication system, pneumatic system, various switch starting positions, safety brake protection device, electric power stabilizing system and electrical instructions. The above-mentioned systems must be uniform, correct, sensitive, reliable and complete. The tight peripheral parts and connecting parts should not be loosened.
B. Lubricate according to the equipment lubrication chart.
c. Manually run the main shaft and each servo axis at low speed.
D. According to the part processing program sheet, check whether the tool compensation value and the key point offset position in the memory table of the CNC system are wrong. The tool compensation value and zero offset value should be called out to check whether they are correct.
E. When using paper tape to input, always check whether the paper tape used is not damaged and whether the photoelectric reader is normal.
F. The specifications of T-bolts used for tight-circumferential parts should be consistent with the specifications of the T-slot of the equipment table. The tightening force should be moderate. It is forbidden to add force to correct parts in all parts of the equipment.
G, Check whether the precautions specified in the “Machine Tool Manual” are followed.
(4) After the power is turned on, the inspection items before work:
Press the NC device power start key “ON”, the initial position coordinates of the machine tool will appear on the CRT display. Check the total pressure gauge installed on the upper part of the machine tool. If the gauge reads “4MPa”, it indicates that the system pressure is normal and formal operation can be performed.
(5) The correct operation steps at work are as follows:
A. Use it reasonably and operate it correctly according to the equipment manual. It is forbidden to use over load, over performance and over standard.
B. During the first programming trial processing, the operator must cooperate closely with the programmer. After confirming that the program is correct, it can be transferred to formal processing.
C, When installing the tool, wipe clean the handle and spindle taper hole and positioning.
D. Workpieces and tools must be installed securely. Prevent collisions with the machine when loading and unloading workpieces. Heavier parts and fixtures should be loaded and unloaded by crane or with the assistance of others.
E. During the processing, the operator is not allowed to leave the post or entrusted to take care of it, and cannot do anything irrelevant to the work. To leave the job temporarily, druk de “Pause” button. To use the “emergency stop switch” correctly, it is strictly forbidden to switch off the power at will during work.
F. It is forbidden to place tooling, measuring tools, stacking parts and irrelevant objects on the guide rail surface and work surface of the equipment. Lin is forbidden to step on the protective cover, and shoes with metal nails are not allowed to step on the work surface.
G, Pay attention to abnormal phenomena during the operation of the equipment, stop in time when a failure occurs, take measures, and record and display the content of the failure. In the event of an accident, stop and cut off the power immediately, protect the scene, report to it in time, and not cover it up, and cooperate with the competent authority to conduct analysis and investigation.
(6) Maintenance after work.
A. The operator should clean up the chips and debris on the equipment in time, organize the work site, and do a good job of maintenance.
B. After the equipment has been maintained, the operator should move the switches and parts of the equipment back to their original positions. Each workbench is protected by oil, and the power supply is cut off in the prescribed order.
c. Exchange in accordance with the regulations on shifts and keep records.
Because the machining center has the above-mentioned functions and strict operating procedures, it greatly reduces the workpiece clamping measurement and the high-speed adjustment time of the machine tool and the turnover, handling and storage time of the workpiece, making the cutting time utilization rate of the machine tool 3-4 times higher than that of the ordinary machine tool. Thereby improving productivity, especially when processing workpieces with complex shapes, high precision requirements, and a complicated variety of replacement periods, it is more economical.
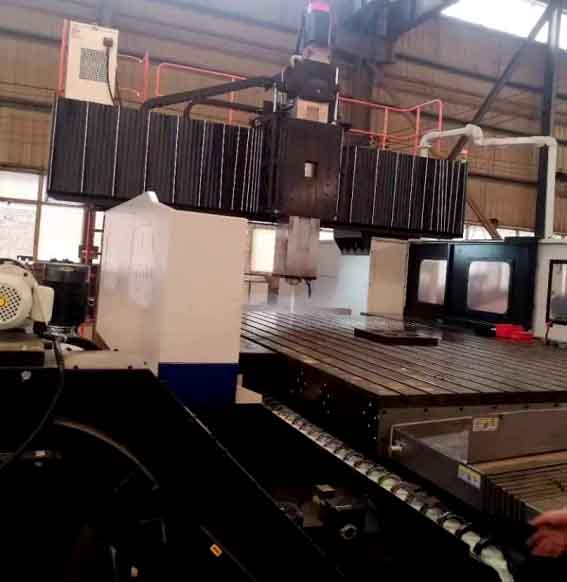
Verwerkingskenmerken van CNC-portaalbewerkingscentrum