5-as CNC-bewerkingsmethode en werktuigmachine. Al in de jaren zestig, de buitenlandse luchtvaartindustrie was het gaan gebruiken om enkele grote werkstukken met doorlopende gladde en complexe vrije-vormoppervlakken te verwerken, maar het is niet op grote schaal gebruikt in meer industrieën. Alleen in het verleden 10 jaren heeft er een snelle ontwikkeling plaatsgevonden. De belangrijkste reden is dat er veel problemen zijn bij vijfassige bewerking, zoals:
1. Programming is complicated and difficult.
Because five-axis machining is different from three-axis, in addition to three linear motions, it also has two rotary motions. The resulting spatial trajectory of the synthetic motion is very complex and abstract, and it is generally difficult to imagine and understand. Bijvoorbeeld, in order to process the required free-form surfaces in space, multiple coordinate transformations and complex spatial geometric operations are often required. Tegelijkertijd, the coordination of the movement of each axis should be considered, to avoid interference, botsing, and the interpolation movement should be timely and appropriate. To ensure the required machining accuracy and surface quality, programming is even more difficult.
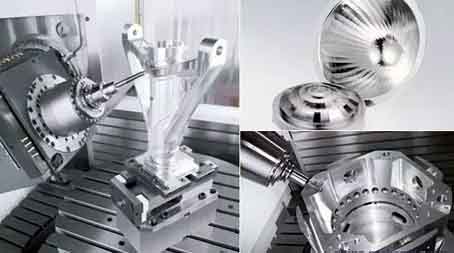
5-as CNC-bewerking van complexe vrije-vormoppervlakken
2. High requirements for CNC and servo control systems.
Since 5-axis machining requires five-axis coordinated motion at the same time, this requires the CNC system to have at least five-axis linkage control function;
In aanvulling, due to the addition of rotary motion in the synthetic motion, this not only increases the workload of the interpolation operation, but also may be amplified due to the small error of the rotary motion, which greatly affects the processing accuracy. Daarom, the CNC system is required to have higher calculation speed (ie shorter processing time of a single block) and accuracy. All of this means that the numerical control system must increase the processor of the RISC chip for processing (dat is, the use of multiple high-bit CPU structures).
In aanvulling, as mentioned earlier, the mechanical configuration of the five-axis machining machine tool has a tool rotation mode, a workpiece rotation mode and a hybrid of the two, and the numerical control system must also meet the requirements of different configurations. Eindelijk, in order to achieve high-speed, high-precision five-axis machining, the CNC system also needs to have a look-ahead function and a large buffer storage capacity. In order to perform calculation, processing and multi-segment buffer storage of the motion data before the program is executed. This ensures that the error is still small when the tool is running at high speed. All these requirements will undoubtedly increase the complexity of the CNC system structure and the difficulty of development.
3. The mechanical structure design and manufacture of five-axis machine tools are also more complicated and difficult than three-axis machine tools.
Because the machine tool needs to add two rotation axis coordinates, it must use a worktable that can tilt and rotate or a spindle head that can rotate and swing. For these two additional components, it is required not only to have a compact structure, but also to have a large enough torque and movement sensitivity and accuracy, which is obviously much more difficult than the design and manufacture of ordinary three-axis processing machine tools.