Wat is 5-assig frezen? Toepassing van 5-assig frezen.
Er zijn veel productietaken waarvoor 3 + 2 positioneren van asfrezen is voldoende en heeft zelfs voordelen. Maar op zijn laatst als het om vrijevormoppervlakken gaat, er is geen manier om 5-assig simultaan frezen te omzeilen.
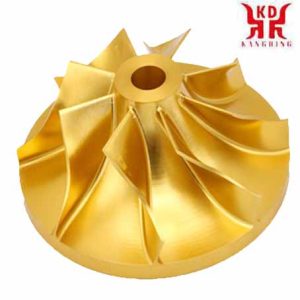
5-as frezen
The decision as to whether it is better to mill in 3 axes with a 4 En 5 as, or simultaneously with 5 bijlen, always depends on the machining task and the machine used and must therefore be made again and again. With the high-end product Powermill, KANGDING has a CAM software in its range that is one of the best systems on the market for technologically demanding 5-axis simultaneous milling.
Powermill supports the user in deciding whether 3-axis milling with additional positioning axes or 5-axis simultaneous milling is the better method for the workpiece to be manufactured. This is done with the help of the component analysis from Powermill, the graphic analysis functions for radii, for the undercut and the flat area as well as the various measuring functions.
Wat is 5-assig frezen?
With 5-axis milling, the machine has – as you can probably imagine – 5 processing axes.
As with the conventional milling machine, there are axes X, Y and Z for linear movement in one of the spatial directions. In aanvulling, the machine has two swivel or rotation axes for 5-axis machining. Often it is a swiveling machine table and a rotation axis for the machining spindle.
Due to the large number of axes, correct 3D processing around the workpiece is possible.
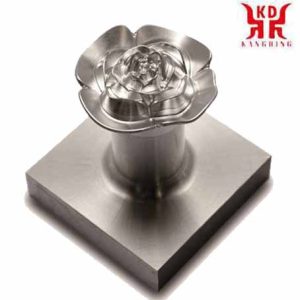
5-asfrezen van roestvrij staal
Advantages of a milling machine with more than 3 bijlen
Due to the large number of axes, the milling machine can approach the milling tool at almost any angle to the workpiece. This makes it possible to manufacture highly complex 3D contours. In het bijzonder, undercuts and cross bores that would otherwise only be possible by repeatedly reclamping the workpiece are made easy with a 5-axis milling machine.
Difficulties in 3D milling with 5 bijlen
A high level of accuracy can only be achieved with a 5-axis CNC milling machine through a sophisticated design and appropriate control strategies.
So that 3D milling with 5 axes is possible, you not only need a machine with the right hardware but also CNC software that supports 5 as frezen. In het bijzonder, path planning for the simultaneous movement of the axes requires powerful computers and efficiently programmed algorithms.
Due to the higher complexity and the greater programming effort, software for 5-axis milling machines is understandably much more expensive.
Advantages of 3 + 2 positioning axis milling
The basic feature of 3 + 2 positioning axis milling is that the use of the CAM software and the milling strategies correspond to those of normal 3-axis programming. Although this does not always lead to shorter programming times, it does reduce the need for training, not least in the case of a software upgrade. By manually assigning the 4th and 5th axes, their positioning always remains under the control of the CAM user, which can be advantageous in some cases.
By activating control cycles via the NC code, the machine operator does not have to convert positioning coordinates. With some machines, 3 + 2 positioning axis machining can achieve a higher rigidity of the moving axes, which leads to a longer tool life and surface quality of the milled surfaces.
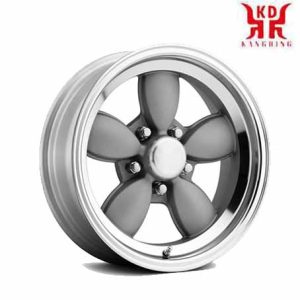
5-axis milling of magnesium alloy
Advantages of 5-axis simultaneous milling
In principle, with 5-axis simultaneous milling, the angle of the tool can be changed at any point on the milling path. The angle is always optimal in terms of chip removal and cutting speed, the cutting conditions at the tool cutting edge remain constant and the strategies for calculating the milling path can be flexibly adapted to the geometry requirements. Due to the larger line spacing compared to 3-axis milling, the machining time is also reduced.
Since CAM systems such as Powermill automatically calculate the ideal pitch axis and automatic evasive movement – for example at undercuts – tools can be clamped shorter and more compact. Even small radii at surface transitions to domes and in cavities can be milled with small, short-clamped tools.
There are also clear advantages of 5-axis simultaneous machining in hobbing. By using the cutting edge on the outside diameter of the tool, an optimal surface is achieved with optimal cutting edge utilization and, at the same time, shorter machining times.
Another plus of 5-axis simultaneous milling is the lower programming effort for curved surfaces and surface transitions. In contrast to 3 + 2 positioning axis milling, it is not necessary to program with different setting positions. The following applies here: the fewer the number of adjustment positions, the shorter the programming and machine runtimes.
And last but not least: the control of the programmed milling paths in connection with a simulation model of the machine tool is possible in advance without having to “run in” de machine.