Schuine CNC-onderdelen kom je vaak tegen in het productieproces. Moet slaan, saai, en freesvormen op het hellende oppervlak. Of het is noodzakelijk om meerdere hellende oppervlakken met verschillende richtingen en verschillende hellingen in dezelfde klemming te verwerken, en elk hellend oppervlak heeft een hogere geometrische tolerantievereiste.
Het numerieke besturingssysteem van het krachtige 5-assige freesbewerkingscentrum heeft de functie van het roteren van het ruimtecoördinatensysteem en de compensatiefunctie van het hellende bewerkingsgereedschap. Dit maakt het mogelijk om sommige onderdelen te verwerken die schuine CNC-bewerking vereisen en een relatief hoge bewerkingsnauwkeurigheid hebben. Bij bewerking op een hellend vlak, het is moeilijk om een bewerkingsprogramma samen te stellen omdat het coördinatensysteem in de ruimte verandert. Noodzaak om de conventionele programmeer-denkmodus voor programmeren te doorbreken, en speciale verwerking van het programma. In dit artikel wordt dit probleem besproken in samenhang met de daadwerkelijke bewerking van hellende CNC-producten.
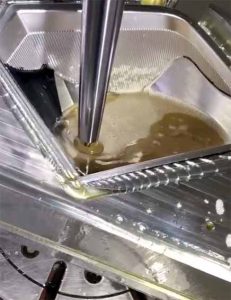
CNC frezen van schuine delen
De conventionele methode voor het bewerken van dergelijke hellende delen is het trekken aan de machinekop, draai het werkblad of gebruik een modulair armatuur. Als de verwerkingsrichting of verwerkingspositie anders is, een tweede klemming en heruitlijning zijn vereist, en het verwerkingsproces is uiterst omslachtig. Vanwege de beperking van de klempositionering en de werktuigmachine zelf, de bewerkingsnauwkeurigheid van de onderdelen kan niet worden gegarandeerd. Er zijn veel gaten in de hellende oppervlaktedelen, en het speciaal gevormde oppervlak is niet gemakkelijk vast te klemmen, en het positioneringsgegeven is niet goed. Meerdere klemmingen veroorzaken een opeenstapeling van fouten, en soms is de margefout van het gat groter dan 1 mm.
Om de verwerkingsproblemen van dit soort onderdelen op te lossen, door voortdurende verkenning en voortdurende verbetering van procesmethoden. Gecombineerd met de bestaande werktuigmachines in de fabriek, Om dit probleem op te lossen werd gekozen voor een 5-assig CNC-freesbewerkingscentrum. De geselecteerde werktuigmachine is een 5-assige koppeling, in aanvulling op 3 lineaire assen, het heeft ook twee roterende assen (C-as: -360°~360°) en zwenkkop (B-as: 0°~110°) . Het besturingssysteem is FANUC160i, die de functie heeft van het roteren van het ruimtecoördinatensysteem en de compensatiefunctie van het gereedschap voor het bewerken van hellende oppervlakken.
Vanuit het perspectief van het realiseren van de bewerking van afgeschuinde onderdelen, na één klemming, meerdere verwerkingsbehoeften zoals saai, tikken, en het frezen van meerdere afschuiningen in verschillende richtingen en verschillende hoeken kan worden voltooid. Het vermindert het aantal klemtijden, vermindert de arbeidsintensiteit, verkort de productiecyclus van producten, en nog belangrijker, verbetert de verwerkingsnauwkeurigheid van onderdelen en zorgt voor de consistentie van de productkwaliteit.
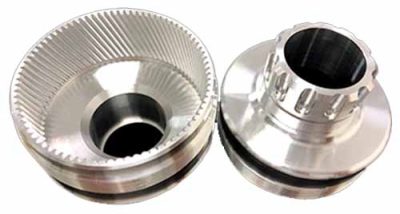
Afgeschuinde draad van 5-assige bewerkte onderdelen
De onderdelen worden weergegeven in de onderstaande afbeelding:
Om dit venster te bewerken, het is duidelijk dat de werktuigmachine een 2-assige koppelingsinterpolatie op de XZ- en YZ-vlakken en een spilkopzwaaibeweging moet voltooien. Omdat om het gereedschap loodrecht op het bewerkte oppervlak te maken, de spil moet een kopzwaaibeweging maken. De spindel is voorzien van een zwenkkop, waarbij sprake is van een reeks bewerkingsproblemen met meerdere assen, zoals de zwenklengte. Daarom, Om dit te voltooien is het noodzakelijk om meerassige programmeermethoden te gebruiken, Programmeren en debuggen van werktuigmachines zijn moeilijk, wat hogere eisen stelt aan programmeurs en machinisten. Bij praktische toepassingen, rekening houdend met factoren zoals het garanderen van de veiligheid van de werktuigmachine, het is noodzakelijk om het bewerkingsproces te simuleren en meerdere luchtsnedes uit te voeren om ervoor te zorgen dat het programma correct is voordat de formele bewerking kan worden uitgevoerd. In aanvulling, het meerassige programma-algoritme is behoorlijk ingewikkeld, en er moet rekening worden gehouden met de invloed van factoren zoals de slingerlengte. Er moet voor een bepaalde werktuigmachine een specifieke nabewerking plaatsvinden, maar de nabewerking is vaak te wijten aan de invloed van het algoritme en de besturingspositie, evenals de stabiliteit van de berekening. Het programma dat wordt verkregen via softwarematige nabewerking is vaak moeilijk om te voldoen aan de eisen van de nauwkeurigheid van onderdeeltekeningen in termen van besturingsnauwkeurigheid.
De directe oorzaak van de toename van de programmeerproblemen is het verschijnen van hellende vlakken. Daarom, als het bewerkingsvlak samen kan vallen met het hellende vlak, dan zal dit soort probleem worden omgezet in een semi-verwerkingsprogrammeringsprobleem met twee assen, en de programmeerproblemen zullen aanzienlijk worden verminderd. Daarom, Gebruik eerst de coördinatensysteemconversiefunctie van de werktuigmachine (G68-opdracht) om het bewerkingsvlak te laten samenvallen met het hellende vlak. Seconde, gebruik het commando gereedschapslengtecompensatie (G432) om de gereedschapslengte in de verticale richting van het hellende vlak toe te voegen. Na bovenstaande verwerking, het probleem van schuine verwerking wordt omgezet in vlakverwerking om op te lossen, zodat de programmeermoeilijkheid aanzienlijk wordt verminderd. Als u meerdere hellende vlakken tegelijkertijd moet bewerken, je hoeft alleen maar de C-as naar C0 te draaien (de nulpositie van de werktafel, de richting van de nulpositie is hetzelfde als de zwenkrichting van de spil), en realiseer vervolgens de verwerking door het coördinatensysteem te roteren en de gereedschapslengte te vergroten. Als de verwerkingsvorm relatief eenvoudig is, het programmeerwerk kan handmatig worden uitgevoerd. Hierdoor is het mogelijk om bewerkingen op meerdere schuine vlakken te realiseren, meerdere werkstations, en meerdere gereedschapswissels in één enkele opspanning van de CNC-bewerkingsmachine.