티타늄 합금 부품의 제품 품질을 향상시키기 위해 티타늄 공구 선삭 및 밀링의 기하학적 매개변수 설정. 제품은 신속하고 정시에 배송됩니다..
(1) 공구의 경사각 γ0: 티타늄 합금 칩과 경사면의 접촉 길이가 짧습니다.. 경사각이 작은 경우, 칩의 접촉 면적을 늘릴 수 있습니다, 절삭열과 절삭력이 절삭날 근처에 과도하게 집중되지 않도록. 방열 조건 개선, 인선 강화 및 치핑 가능성 감소. 티타늄을 터닝하는 데는 일반적으로 γ0=5°~15°가 소요됩니다..
(2) The clearance angle α0 of the tool: The processed surface of titanium alloy has large elastic recovery and serious cold hardening. The use of a large relief angle can reduce the friction, 부착, 부착, tearing and other phenomena caused to the flank surface, so as to reduce the wear of the flank surface. The relief angle of various cutting titanium alloy tools is basically greater than or equal to 15°.
(3) The leading deflection angle κr and the secondary deflection angle κ´r of the milling tool: 티타늄 합금을 밀링할 때, the cutting temperature is high and the elastic deformation tends to be large. When the rigidity of the process system allows, the entering angle should be reduced as much as possible to increase the heat dissipation area of the cutting part and reduce the load per unit length of the cutting edge. 일반적으로, κr=30° is used, and κr=45° for rough machining. Reducing the secondary deflection angle can strengthen the tool tip, which is beneficial to heat dissipation and reduces the surface roughness value of the machined surface. Generally take κ´r =10°~15°.
(4) The blade inclination angle of the tool λs: Due to the rough surface and uneven surface structure of the blank, the cutting edge is prone to chipping during rough turning. In order to increase the strength and sharpness of the cutting edge, the sliding speed of the chip should be increased. 일반적으로, λs = -3°~-5° is used for rough turning, and λs = O° for fine turning.
(5) The radius of the nose arc of the tool rε: When turning titanium alloy, the tool tip is the weakest part, which is easy to chip and wear, so it needs to grind the tool tip arc. Generally rε=0.5~1.5mm.
Negative chamfering (bγ=0.03~0.05 mm, γ01=-10°~0°) is used during turning, and the arc radius of the bottom of the chip flute is Rn=6~8 mm.
게다가, the quality of tool sharpening is also very important to improve its durability. Carbide cutting tools should be sharpened with diamond grinding wheels. The cutting edge must be sharp when cutting, the surface roughness Ra value of the front and rear cutting faces should be less than 0.4um, and the cutting edge is not allowed to have tiny gaps. After the tool is sharpened and ground, its durability can be increased by 30%.
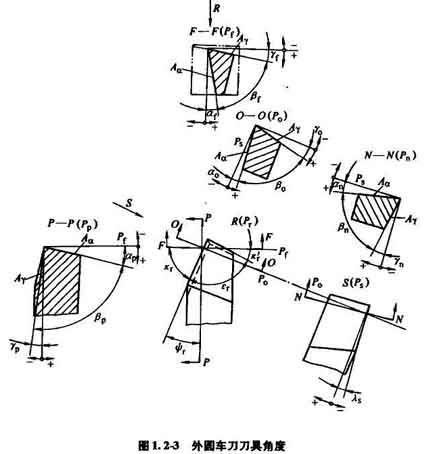
Design of cutting edge angle for turning and milling titanium