제품 카테고리
- CNC 밀링 서비스 31
- CNC 스탬핑 서비스 0
- CNC 판금 0
- 신속한 프로토 타입 12
- 스탬핑 다이 0
- 티타늄 합금 부품 4
- 스테인레스 스틸 부품 5
- 알루미늄 밀링 부품 14
- CNC 터닝 서비스 16
What is aluminum die casting?
Aluminum die-casting refers to aluminum parts of pure aluminum or aluminum alloy obtained by casting. 일반적으로, a sand mold or a metal mold is used to pour the heated liquid aluminum or aluminum alloy into the mold cavity, 얻은 다양한 모양과 크기의 알루미늄 부품 또는 알루미늄 합금 부품을 일반적으로 알루미늄 다이캐스팅이라고합니다..
Aluminum die-casting refers to aluminum parts of pure aluminum or aluminum alloy obtained by casting. 일반적으로, a sand mold or a metal mold is used to pour the heated liquid aluminum or aluminum alloy into the mold cavity, 얻은 다양한 모양과 크기의 알루미늄 부품 또는 알루미늄 합금 부품을 일반적으로 알루미늄 다이캐스팅이라고합니다..
Aluminum die casting technology
Aluminum casting is a modern molding technology
The complex casting of aluminum castings is a kind of low pressure casting technology with electromagnetic pump as the core. The composite purification technology of aluminum smelting and molding is a new technology at the core of the aluminum die-casting industry, a modern technology for producing high-quality aluminum castings. The electromagnetic pump low pressure casting molten metal transmission system has a stable flow and convenient flow control. The advantage of alleviating the suction process of molten alumina and easy realization is the automation of the use process, which not only improves the casting quality of aluminum castings, but also improves the working environment. Reduce labor intensity, realize automation and modern casting production.
An important part of the purification of molten enamel alloy castings is the aluminum smelting and composite purification facilities in addition to gas injection and spin foam ceramic filters with high degassing, unless the performance of metal inclusions. 게다가, it uses a new long-life lining material and has an independent heat preservation/heating system that can be used for a large number of continuous production, as well as intermittent production. The molten aluminum purification technology of this technology is high in efficiency, long life, 저렴한 비용, effective, easy to install, use and flexible. Casting experience tells us that the quality of aluminum castings to solve complex problems is in three main aspects:
(1) Melting and melting of molten aluminum,
(2) Smooth transition of molten aluminum metal halide lamp
(3) The size and stability of the mold and sand core process.
Core manufacturing process modeling can see that casting quality and output have a direct impact. Casting porosity, sticky sand, scars, thermal cracking, surface quality, dimensional accuracy, and sand performance have a very good relationship. The new technology for modeling and manufacturing is PEPSET. The core resin binder used in the original zirconium sand sand has an independent, non-hardening chemical reaction mechanism initially from hard sand to hard sand. It's time to start hardening, once the curing reaction starts fast. In a tough, 고강도, gas fat collapse small, good performance is the complexity of the casting surface, dimensional accuracy and quality stability.
Performance and application of aluminum die casting
Cast aluminum alloy has some advantages that other castings cannot match, such as beautiful appearance, light weight, 내식성, 등., making it widely favored by users. Especially since the lightweight of automobiles, cast aluminum alloy castings have been widely used in the automobile industry.
The density of cast aluminum alloy is lower than that of cast iron and cast steel, but its specific strength is higher. 그러므로, the use of aluminum alloy castings under the same load conditions can reduce the weight of the structure. 그러므로, aluminum alloy castings are widely used in the aviation industry, power machinery and transportation machinery manufacturing. Aluminum alloy has good surface gloss and good corrosion resistance in the atmosphere and fresh water, so it has a wide range of uses in the manufacture of civil utensils. Pure aluminum has good corrosion resistance in oxidizing acid media such as nitric acid and acetic acid, so aluminum castings also have certain uses in the chemical industry. Pure aluminum and aluminum alloys have good thermal conductivity. They are used in heat exchange devices used in chemical production, and parts that require good thermal conductivity on power machinery. 예를 들어, cylinder heads and pistons of internal combustion engines are also suitable for manufacturing of aluminum alloy.
Aluminum alloy has good casting properties. Due to the low melting point (the melting point of pure aluminum is 660.230C, the casting temperature of aluminum alloy is generally about 730-750C). It can be widely used type of metal casting and pressure casting and other methods to increase the intrinsic quality of the casting, the degree of dimensional accuracy and surface finish and productivity. Due to the high latent heat of solidification of aluminum alloy, the solidification process of molten aluminum lasts much longer than cast steel and cast iron under the same weight. It has good liquidity and is conducive to casting thin-walled and complex-structured castings.
Cast aluminum alloy castings have many advantages, making it one of the most popular casting products for the development direction of the casting industry and purchasing customers. In the future, with the advancement of aluminum alloy casting technology, it will show its style on a larger stage.
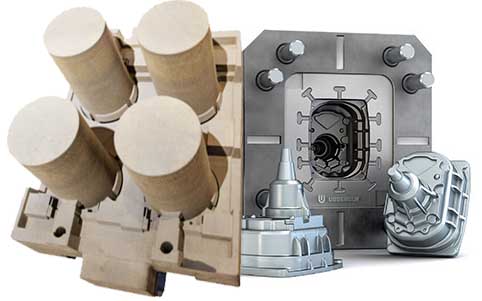
Sand mold or metal mold for aluminum die casting
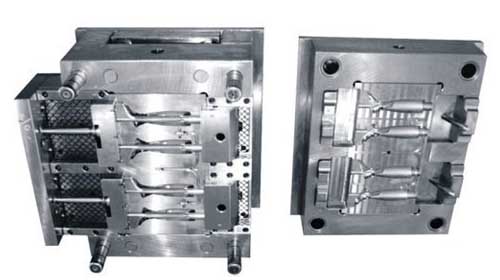
Pressure aluminum die casting mold
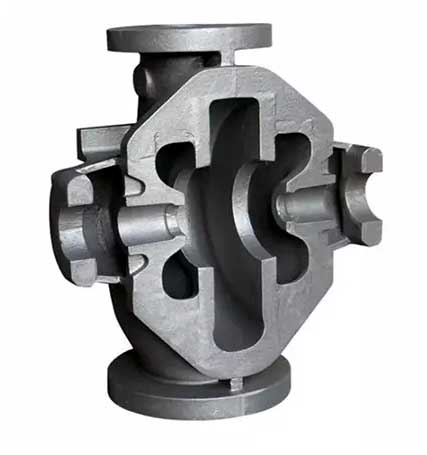
Magnesium alloy casting parts
Analysis of urgent problems to be solved in the future development of domestic aluminum alloy casting industry
Reducing energy consumption, reducing environmental pollution and saving limited resources is a very important and urgent task facing all countries today. Driven by the general trend of lightweight products such as automobiles, it can be predicted that my country's light metal casting market will have a substantial development in the next 10 years. The proportion of aluminum and magnesium alloy castings in the major casting production countries is between 13% 그리고 19%, and some countries (such as Italy) are as high as 30% 에게 40%. The proportion of aluminum and magnesium alloy castings in my country is less than 10%. More than 90% of aluminum castings in developed countries are used in automobile parts manufacturing. In my country, there are still many problems to be solved for aluminum alloy castings to form large-scale production and meet the requirements of automobile lightweight:
첫 번째, automotive requirements for aluminum castings are developing towards thin-walled, 복잡한 모양, 고강도, and high quality. To meet this requirement, the casting process should be further optimized and new alloy materials should be developed.
두번째, the production cost should be reduced from the perspective of design and process. 예를 들어, use one-mold multi-part technology and automation technology to improve productivity, extend mold life, and use integrated design to reduce the number of parts.
Third, use computer simulation technology to shorten the development cycle of the process plan.
Fourth, increase the recovery of aluminum. Recycled aluminum is the main raw material for aluminum casting. While developing the foundry industry, our country should pay attention to the utilization of recycled aluminum resources, develop technologies to effectively separate aluminum from composite and dissimilar materials, and establish a wide range of waste recycling systems.
문의하기
이메일을 기다리는 중, 이내에 답변해 드리겠습니다. 12 필요한 귀중한 정보를 몇 시간 동안.