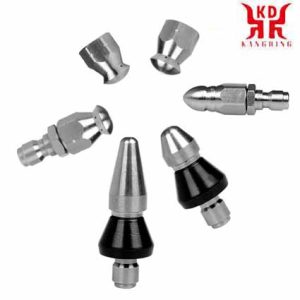
Custom non-standard special nozzleshat is a nozzle? 노즐의 CNC 가공 기술
노즐이란 무엇입니까?? 노즐의 CNC 가공 기술
노즐은 다양한 스프레이 조건에서 작동하도록 설계되었습니다., 따라서 사용 중 최고의 스프레이 성능을 얻으려면 필요에 맞는 노즐을 선택하십시오.. 노즐의 특성은 주로 노즐의 스프레이 형태에 반영됩니다., 그건, 액체가 노즐 입구를 떠날 때 형성되는 형상과 그 주행 성능. 노즐의 명칭은 팬(Fan)으로 나누어진 스프레이 형태에 따라 붙여진 이름입니다., 원뿔, 액체 기둥 흐름 (즉 제트기), 공기 원자화, 플랫 노즐. 그 중, 콘 노즐은 두 가지 범주로 나뉩니다: 속이 빈 원뿔과 단단한 원뿔; 노즐은 다양한 종류의 스프레이에서 매우 중요한 구성 요소입니다., 기름 살포, 샌드블라스팅 및 기타 장비, 그리고 중요한 역할을 하죠.
Selection of nozzle
Since the nozzle is designed to work under a variety of different spray conditions, the nozzle suitable for the needs is selected to achieve the best spray performance in use. 노즐의 특성은 주로 노즐의 스프레이 형태에 반영됩니다., 그건, 액체가 노즐 입구를 떠날 때 형성되는 형상과 그 주행 성능. The name of the nozzle is that the spray shape is divided into fan, 원뿔, 액체 기둥 흐름 (즉 제트기), 공기 원자화, 플랫 노즐. The cone nozzle is divided into two categories: 속이 빈 원뿔과 단단한 원뿔;
The factors for selecting nozzles include flow rate, pressure, spray angle, coverage, impact force, temperature, 재료, application, 등., and these factors are often interrelated and restrict each other. Flow rate and pressure, spray angle and coverage are all proportional to each other. The purpose of any nozzle jet is to maintain continuous contact between the bath liquid and the workpiece, and the factor of flow rate is more important than pressure. The temperature of the liquid does not affect the spray performance of the nozzle, but it affects the viscosity and specific gravity, and also affects the choice of materials.
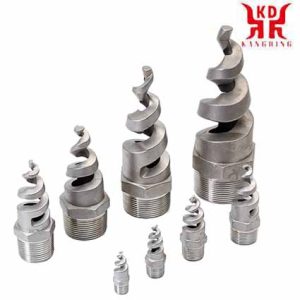
나선형 스테인레스 스틸 노즐
Nozzle material selection
The material of the nozzle should also be determined according to the chemical characteristics of the bath:
1. For non-corrosive baths, bronze casting or plastic die casting can be used according to the difficulty of processing;
2. To prevent corrosion, non-metallic materials can be used;
3. Nylon plastics can be used for strong corrosive baths such as sulfuric acid and hydrochloric acid;
4. The nozzle material used for the phosphating bath is generally acid-resistant stainless steel;
5. The nozzle to prevent corrosion can also be made of stainless steel or nylon.
Nozzle selection method
For nozzles with a certain impact force, small-angle nozzles should be selected, and liquid column flow (ie jet flow) is the best;
Fan-shaped nozzles are suitable for cleaning, degreasing, 냉각, 등., cone-shaped nozzles are suitable for rinsing, surface layer, 인산염 처리, humidification, dust removal, 등.;
For the nozzles of degreasing and washing processes, the jet nozzles with stronger impact force can be selected: Take the “V”-type or fan-shaped nozzle as an example, the spray angle of 60° is the best, which has a large impact force;
For the nozzle of the phosphating process, a centrifugal nozzle with good atomization, fine and uniform water particles, and weak impact force can be selected: Take the “지” type or cone nozzle as an example, the best distance between the nozzle and the workpiece is 40cm-50cm, It has the spray effect of dispersing and atomizing the liquid.
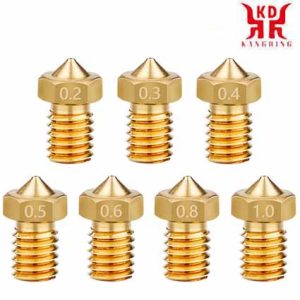
Conical copper nozzle structure
Quality inspection of nozzles
The nozzle needs to be repaired, regularly inspected, cleaned and even replaced in order to ensure the quality of the final product and maintain the economic benefits of the production process. The method and frequency of maintenance procedures depend on the application. The maintenance plan can be arranged according to the purpose, liquid and nozzle material.
There are seven common causes that affect nozzle spray problems:
a) Corrosion and wear: The material on the surface of the nozzle orifice and the internal flow channel gradually becomes larger or deformed, which in turn affects the flow rate, pressure and spray shape.
b) Corrosion: The chemical action of the spray liquid or the environment causes corrosion and damages the nozzle material.
c) Blocking: Dirt or other impurities in the liquid block the nozzle mouth, thus restricting the flow rate of the nozzle and disturbing the spray shape and its uniformity.
d) Bonding: The spray, mist or chemical accumulation on the material inside or outside the edge of the nozzle caused by the evaporation of the liquid can leave a dry solidified layer and block the nozzle or internal flow channel.
e) Temperature damage: Overheating will have certain damaging effects on nozzle materials designed for non-high temperature applications.
에프) Incorrect installation: Washers that deviate from the axis, over-tightening, or other changes in position can have adverse effects.
g) Accidental damage: During installation and cleaning, the nozzle may be accidentally damaged due to the use of incorrect tools.
The structure of the nozzle
Different nozzle structures will lead to differences in processing efficiency and nozzle life. Reasonable nozzle structure enables the abrasive to obtain high speed, which is a necessary condition for improving the processing efficiency and reducing the cost. From the advent of the nozzle to a long period afterwards, the cylindrical nozzle structure was adopted. 지금까지, there are various nozzle structures developed at home and abroad. The fuel nozzle is equipped with an electromagnetic coil, an iron core and a needle valve integrated with the iron core. The structure types and characteristics of commonly used nozzles are shown in the following table
1. Cylindrical straight hole nozzle structure
Schematic diagram of cylindrical straight hole nozzle structure. It has both functions of spray gun and nozzle, and has a simple structure. It can be directly replaced by seamless steel pipe, or it can be obtained by drilling in the material, but the nozzle life is short, and it is mostly used in occasions where sandblasting is not required.
2. Conical nozzle structure
A schematic diagram of the structure of a cone-shaped nozzle. This nozzle structure has a cone-shaped inlet with a diversion function and a straight section that serves as a bundling function. It is relatively easy for the abrasive to enter the nozzle, and the distribution of the abrasive on the nozzle section is more uniform than that of a cylindrical nozzle.
3. Special nozzle
Double outlet special sandblasting nozzle, complex structure, generally used in special occasions, such as sandblasting of the inner wall of the pipeline
4. Combined nozzle structure
Design materials with different properties at the nozzle inlet, outlet and middle part, and assemble each part of the material into the nozzle by mechanical combination. The combined nozzle is designed with high-hardness ceramics or other wear-resistant materials at the nozzle inlet and outlet. The middle section of the nozzle can be designed with high toughness-based metal or other materials. The combined nozzle can meet the different requirements of the nozzle inlet, outlet and middle parts of anti-erosion and wear performance. 어느 정도, the erosion resistance of the nozzle is improved, but compared with the monolithic nozzle, two or more materials need to be prepared, and related processes such as assembly are increased.
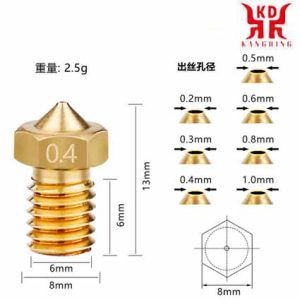
Micro nozzle
Application areas of nozzles
1. Vehicles, container companies: clip nozzles, 등.
(1) In the pre-treatment of the spraying line, dephosphorization, degreasing and rust removal;
(2) The rain line is mainly to detect whether the product is well-sealed
2. Paper mill
(1) Defoaming nozzles, to remove foam in the pulp, hollow cone nozzles and spiral nozzles are used;
(2) Coating nozzle, which is the surface coating of paper, is used on the coating machine to atomize the nozzle;
(3) The water needle nozzle used for cutting paper, 그건, the needle nozzle, requires high pressure to work, and must be inlaid with ceramics or high alloys;
(4) Needle nozzles and fan nozzles are generally used to clean the nozzles of the net cage cloth, and the nozzles are self-cleaning;
(5) Slurry drawing nozzle, narrow-angle nozzle is used:
3. Textile industry: atomized nozzle
(1) Humidification of workshops, especially under the conditions of high dust in textile mills, cotton spinning, weaving, wool tops, towels;
(2) Add a kind of pine flower oil to the wool yarn to prevent the wool yarn from drying and breaking;
4. Electronics
(1) The large space of a large electronic factory is humidified and cooled, using atomized nozzles;
(2) Cleaning nozzles for electronic boards, fan-shaped, wide-angle, and quick-release nozzles;
(3) The application of the rosin nozzle after the circuit board is formed, spraying the rosin to protect the circuit board;
(4) The circuit board is useful for the nozzle of Saigang;
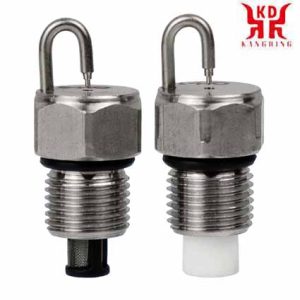
Spray nozzle of humidifier
5. Pharmaceutical factory: atomizing nozzle
(1) Granulation nozzle,
(2) Coating nozzle, 그건, the sugar coating on the surface of the medicine;
6. Food industry:
(1) Cleaning of mustard tuber;
(2) Washing of fruits, vegetables, 등., such as washing and hair removal of strawberries;
(3) The purification workshop has an air shower room and air shower nozzles are used;
7. Thermal power plant
(1) Large-flow nozzles, such as silicon carbide nozzles and spiral nozzles, are used for desulfurization and dust removal;
(2) Used in the cooling system before the boiler;
8. Garbage disposal
(1) Use an atomizing nozzle to spray a spice on the garbage to get rid of the peculiar smell;
(2) Use nozzles such as solid cones to reduce dust;
9. Radiator: because of the spraying treatment, it is useful for clip nozzles;
10. Steel pipe factory: wide-angle and multi-component paint nozzles made of titanium;
(1) High-pressure derusting nozzles used in steel pipe factories;
(2) Coated nozzles inside and outside the steel pipe;
11. For pressure vessel factories, solid cone nozzles are used.
12. Winery
(1) Beauty nozzles and mist nozzles on beauty machines such as beer and wine
(2) Multi-nozzle or rotating nozzle for cleaning bottles;
13. Petroleum and chemical industry
(1) Cleaning nozzles for bottles and cans, multi-head or rotating nozzles;
(2) Cooling nozzles for bottles and cans;
(3) In order to fully reflect the chemical substances, a nozzle composed of a shell and an inner core is used
14. Cooling tower: use large flow nozzles, such as clip nozzles, spiral nozzles, 등.;
15. Drying equipment: spray or atomization drying equipment uses air atomizing nozzles or metal micro atomizing nozzles.
16. Wood drying: nozzles are used to prevent the wood from cracking;
17. Dust removal, smoke removal, waste gas treatment;
(1) Used in wet hair dust collector or equipment;
(2) For the purification of waste smoke and waste gas of some enterprises, large flow nozzles are generally used;
18. Lubrication:
(1) Gear lubrication;
(2) Spraying of release agent on spray equipment;
(3) Steel cable lubrication;
(4) Lubrication of the die on the large forging press;