전통적인 밀링은 주로 윤곽선 및 홈과 같은 단순한 형상/특징을 밀링하는 데 사용됩니다.. CNC 밀링 머신은 복잡한 윤곽 형상과 특징을 처리할 수 있습니다.. 밀링 및 보링 머시닝 센터는 가공을 위해 3축 또는 다축 밀링 및 보링을 수행할 수 있습니다., 금형, 검사 도구, 벽이 얇고 복잡한 곡면, 임펠러 블레이드, 등. CNC 밀링 내용 선택 시, CNC 밀링 머신의 장점과 핵심 역할을 최대한 활용해야 합니다..
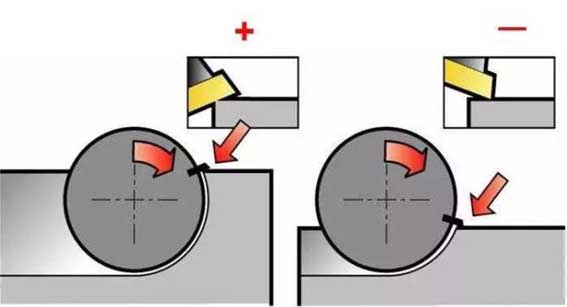
Cutter position setting for down milling
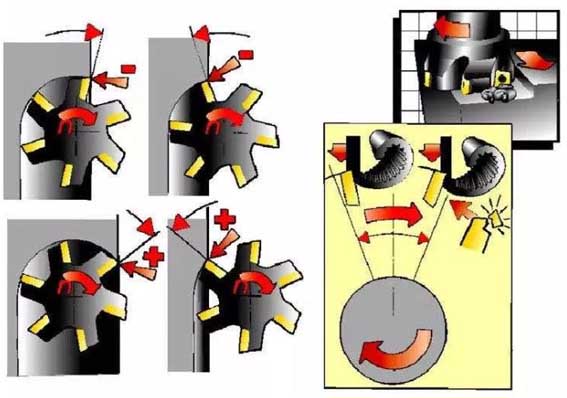
Cutter position setting for up milling
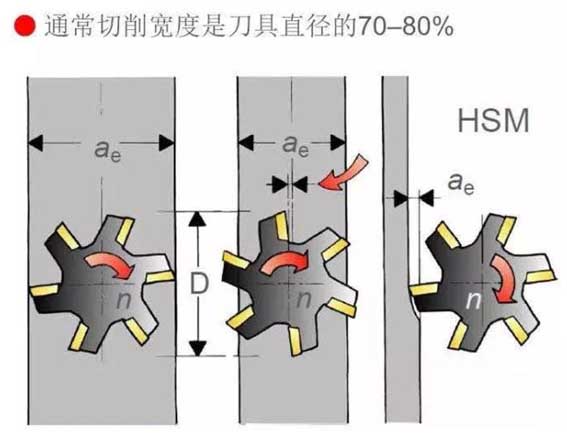
The center offset of the milling tool when the tool diameter is larger than the width of the workpiece
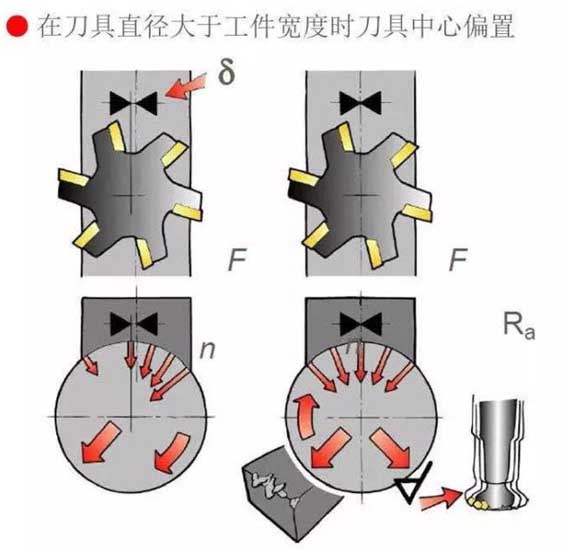
The cutting width is 70%~80% of the tool diameter
▲Milling processing case
In the actual production of milling processing, it includes many application skills such as machine tool setting, workpiece clamping and tool selection. The following is a brief summary of 4 complete solutions of milling and 17 main points of milling. Each point is worthy of your in-depth grasp.
Please resend the email again
1. Power capacity
Check the power capacity and machine rigidity to ensure that the machine tool can use the required milling cutter diameter.
2. The stability of the workpiece
Workpiece clamping conditions and considerations.
3. Tool overhang
Make the tool overhang on the spindle as short as possible during processing.
4. Choose the right milling cutter tooth pitch
Use the correct tooth pitch of the milling cutter suitable for the process to ensure that there are not too many blades involved in the cutting, otherwise it will cause vibration.
5. The thickness of the milled workpiece
For narrow workpieces or when milling with gaps, ensure that there is sufficient thickness of the blade to take the knife.
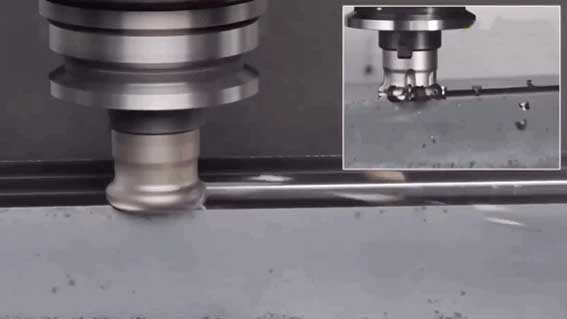
Use positive rake geometry indexable milling inserts
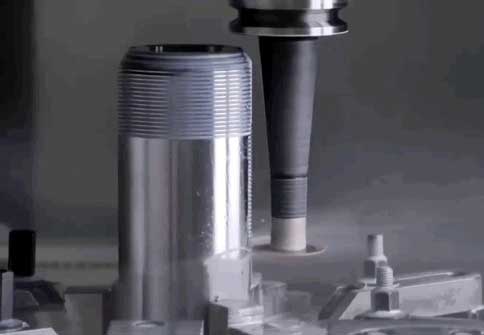
적절한 커터 톱니 피치를 선택하십시오.
6. Groove selection of milling inserts
Use positive rake geometry indexable milling inserts as much as possible to ensure smooth cutting action and lowest power consumption.
7. Use the correct feed
By using the recommended maximum chip thickness, ensure the correct feed of the milling insert used to achieve the correct cutting effect.
8. Cutting direction
Use down milling as much as possible.
9. Part considerations
The material and configuration of the workpiece, and the quality requirements of the surface to be processed.
10. Material selection of milling inserts
Select the geometry and material according to the type of workpiece material and application type.
11. Vibration-damped milling tools
For longer overhangs that are more than 4 times the tool diameter, the vibration tendency becomes more obvious, and the use of vibration-damped milling tools can significantly increase productivity.
12. Entering angle
Choose the most suitable entering angle.
13. Milling cutter diameter
Choose the correct diameter of the milling cutter according to the width of the workpiece.
14. Positioning of milling tools
Position the milling cutter correctly.
15. Cutting in and out of milling tools
It can be seen that through the arc cutting, the chip thickness when the tool is retracted is always zero, which can achieve higher feed and longer tool life.
16. Coolant
Use coolant only when deemed necessary. 일반적으로, milling can be performed better when no coolant is used.
17. Maintenance
Follow tool maintenance recommendations and monitor tool wear.