가공된 알루미늄 부품의 변형에는 여러 가지 이유가 있습니다., 알루미늄 소재와 관련된, 부품의 모양, CNC 기계 및 장비. 주로 다음과 같은 측면이 있습니다: 공백 내부 응력, 절삭력, 절단열로 인한 변형, 체결력에 의한 변형 및 변형.
가공 변형을 줄이기 위한 가공 조치
1. 블랭크의 내부 응력을 줄입니다.. 자연적 또는 인공적 노화 및 진동 처리를 통해 블랭크의 내부 응력을 부분적으로 제거할 수 있습니다.. 전처리도 효과적인 가공 방법입니다.. 대형 블랭크의 경우, 마진이 커서 가공 후 변형도 크다. 대형 블랭크의 여유 부분을 사전 밀링하는 경우. 후속 공정에서 가공 변형을 줄일 수 있을 뿐만 아니라, 전처리 후에 내부 응력의 일부를 방출할 수도 있습니다..
2. 공구의 절삭능력과 공구의 재질을 향상시킵니다.. 기하학적 매개변수는 절삭력과 절삭열에 중요한 영향을 미칩니다.. 부품의 변형을 줄이려면 올바른 도구 선택이 필수적입니다..
1) 밀링 공구의 기하학적 매개변수를 합리적으로 선택하십시오..
① 경사각: 블레이드의 강도를 유지하는 조건에서, 경사각은 적절하게 커야 합니다.. 한편으로는, 날카로운 절삭날을 연마할 수 있습니다., 그리고 다른 한편으로는, 절단 변형을 줄일 수 있습니다, 칩 제거를 원활하게 하십시오, 절삭력과 절삭 온도를 낮추십시오.. 네거티브 경사각 도구를 사용하지 마십시오..
② 여유각: 릴리프 각도의 크기는 측면 표면의 마모와 가공 표면의 품질에 직접적인 영향을 미칩니다.. 여유각 선택 시 절단 두께는 중요한 조건입니다.. 거친 밀링 중, 큰 공급 속도로 인해, 절삭부하가 크고 발열량이 크다, 공구의 좋은 방열 조건이 필요합니다.. 그러므로, 여유각은 더 작아야합니다. 밀링을 마무리할 때, 절삭날은 측면과 가공면 사이의 마찰을 줄이고 탄성 변형을 줄이기 위해 날카로워야 합니다.. 그러므로, 릴리프 각도는 더 커야합니다.
③ 나선 각도: 밀링을 원활하게 하고 밀링 힘을 줄이기 위해, 나선 각도는 가능한 한 크게 선택해야 합니다..
④ 진입각도: 절입각을 적절하게 줄이면 방열 조건이 개선되고 가공 영역의 평균 온도가 낮아질 수 있습니다..
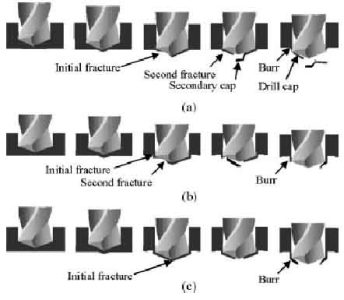
가공된 알루미늄 부품의 변형을 방지하는 방법
2) 밀링 공구 구조 개선.
① 밀링 커터 날 수를 줄이고 칩 공간을 늘립니다.. 알루미늄 소재의 큰 가소성으로 인해, 가공 중 큰 절단 변형, 더 큰 칩 용량 공간이 필요합니다., 따라서 칩 수용 플루트의 하단 반경은 더 커야 하고 밀링 커터 톱니 수는 더 작아야 합니다..
② 밀링 커터 날의 미세 연삭. 치아 절삭날의 거칠기 값은 Ra=0.4um보다 작아야 합니다.. 새 칼을 사용하기 전에, 치아를 갈 때 잔여 버와 약간의 톱니를 제거하기 위해 치아의 앞면과 뒷면을 고운 오일스톤으로 가볍게 갈아야 합니다.. 이런 식으로, 절삭열을 줄일 수 있을 뿐만 아니라, 절단 변형도 상대적으로 작습니다..
③ 밀링 공구의 마모 기준을 엄격하게 관리합니다.. 도구를 착용한 후, 공작물의 표면 거칠기 값이 증가합니다., 절삭온도가 올라간다, 공작물의 변형이 증가합니다.. 그러므로, 내마모성이 우수한 공구 재료 선택 외에도, 공구 마모 표준은 0.2mm보다 커서는 안 됩니다., 그렇지 않으면 구성인선이 생기기 쉽습니다.. 절단시, 변형을 방지하기 위해 공작물의 온도는 일반적으로 100°C를 초과해서는 안 됩니다..
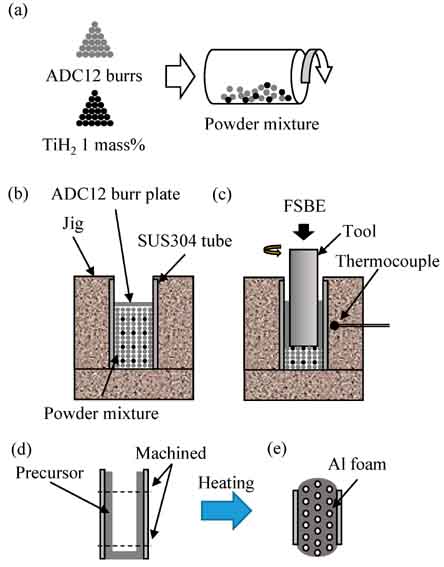
가공된 대형 알루미늄 부품의 변형을 방지하기 위한 충진 방식
3. 공작물의 클램핑 방법을 개선하십시오.. 강성이 좋지 않은 얇은 벽의 알루미늄 가공물용, 변형을 줄이기 위해 다음과 같은 클램핑 방법을 사용할 수 있습니다.:
① 얇은 벽의 알루미늄 부싱 부품용. 3조 셀프 센터링 척 또는 스프링 척을 사용하여 반경 방향에서 클램핑하는 경우, 처리 후 출시되면, 공작물은 필연적으로 변형됩니다. 이때, 강성이 더 좋은 축 끝면의 클램핑 방법을 사용해야 합니다.. 부품의 내부 구멍을 찾으려면, 맨드릴을 통해 자체 제작한 스레드 만들기, 부품의 내부 구멍에 슬리브를 넣습니다., 덮개판으로 단면을 누른 후 너트로 조여줍니다.. 외부 원을 가공할 때 클램핑 변형을 피할 수 있습니다., 이를 통해 만족스러운 가공 정확도를 얻습니다..
② 박육, 박판 알루미늄 가공물 가공 시, 균일하게 분산된 조임력을 얻으려면 진공 흡입 컵을 사용하는 것이 가장 좋습니다., 그런 다음 더 작은 절단 두께로 가공합니다. (수량), 공작물 변형을 잘 방지할 수 있는. 게다가, 내부 충전 방법도 사용할 수 있습니다.. 벽이 얇은 공작물의 공정 강성을 높이기 위해, 클램핑 및 절단 중에 공작물의 변형을 줄이기 위해 공작물 내부에 매체를 채울 수 있습니다.. 예를 들어, 요소가 함유된 용융물을 붓는다 3% 에게 6% 질산 칼륨을 공작물에 넣습니다.. 처리 후, 공작물을 물이나 알코올에 담가서 충전물을 녹인 후 부어주세요..
4. 절차를 합리적으로 정리하라. 고속 절단 중, 큰 가공 여유와 지속적인 절삭으로 인해, 밀링 공정에서 종종 진동이 발생합니다., 이는 가공 정확도와 표면 거칠기에 영향을 미칩니다..
그러므로, CNC 고속 절단의 가공 공정은 일반적으로 다음과 같이 나눌 수 있습니다.: 황삭 – 준마무리 – 클리어 코너 가공 – 마무리 및 기타 공정. 높은 정밀도가 요구되는 부품용, 때로는 두 번째 반정삭 가공을 수행한 후 가공을 마무리해야 하는 경우도 있습니다.. 거친 가공 후, 거친 가공으로 인한 내부 응력을 제거하고 변형을 줄이기 위해 부품을 자연적으로 냉각시킬 수 있습니다.. 거친 가공 후 남는 여백은 변형량보다 커야 합니다., 일반적으로 1 에게 2 mm. 마무리하는 동안, 부품의 마감 표면은 균일한 가공 여유를 유지해야 합니다., 일반적으로 0.2-0.5mm가 적절합니다., 가공 공정 중에 공구가 안정적인 상태에 있도록. 절단 변형을 크게 줄일 수 있습니다., 좋은 표면 처리 품질을 얻으십시오, 제품의 정확성을 보장합니다.
위에서 언급한 이유 외에도, 실제 작동에서는 알루미늄 부품의 작동 방법도 매우 중요합니다..