CNC 가공 부품, PCB 보드 밀링 포지셔닝 설계
CNC 밀링의 소위 포지셔닝은 포지셔닝 핀을 사용하여 밀링 기계의 작업대에서 처리할 인쇄 회로 기판을 위치시키는 것입니다., 부품의 형상을 편리하고 정확하게 CNC가공할 수 있도록. 간단하고 안정적인 포지셔닝이 필요합니다, 칩을 제거하는 동안 부품을 빠르게 로드 및 언로드할 수 있습니다.. 위치결정 방법은 다양하다: 일부 밀링 머신이 왕복 작업대로 설계된 경우, 하나의 워크벤치가 처리 중일 때, 다른 작업대는 부품을 로드 및 언로드합니다.. 두 세트의 밀링 플레이트 위치 지정 방법이 사용됩니다.. CNC 밀링 테이블에서 밀링 포지셔닝 패드 1개를 가공할 때, 다른 밀링 포지셔닝 패드는 플랫폼에 로드 및 언로드됩니다.. 두 사람의 교환에는 몇 초 밖에 걸리지 않습니다..
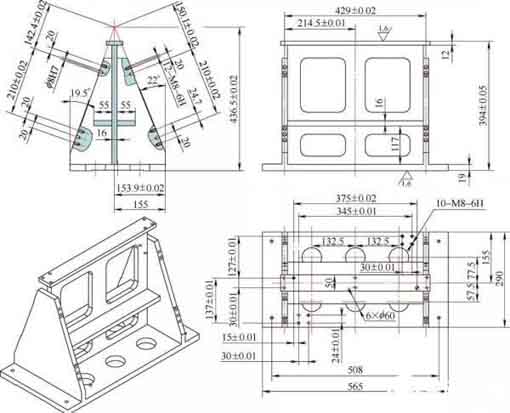
CNC 밀링 부품의 위치 결정 설계
CNC 밀링 테이블 자체는 부품 가공 중 포지셔닝 플레이트입니다.. 핀으로 위치를 지정하고 나사로 고정하는 알루미늄 합금판입니다.. 각 CNC 밀링 스핀들 아래 작업대에는 구멍 슬롯 위치 지정 시스템이 있습니다.. 밀링 패드는 실제로 중간 위치 고정 장치입니다., 가끔 불린다 “소프트 포지셔닝”. 부품을 안정적으로 찾고 신속하게 언로드할 수 있어야 합니다., 보조 시간을 줄이고 생산 효율성을 향상시킵니다.. 윤곽을 밀링하기 전, 부품의 형상과 동일한 치수의 홈이 밀링 패드에 사전 밀링되어 있습니다.. 일반적으로, 홈 폭의 치수는 실제 밀링 커터의 직경에 더한 값입니다. 0.5 mm. 홈 깊이는 2.5mm입니다.. 가공과정에서, 밀링 커터 모션 트랙의 경로입니다.. 청소기가 먼지를 빨아들이기 때문에, 칩을 제거하기 위해 홈에 공기 흐름이 생성됩니다., 처리를 더 매끄럽게 만드십시오, 칩이 밀링 커터의 칩 홈을 막는 것을 방지합니다., 그리고 가장자리를 줄이세요. 처리할 때, 밀링 커터가 홈 안으로 1.5-2mm 확장되도록 만듭니다.. 이는 밀링 커터가 지속적으로 부품을 절단하여 최종 마모가 마모되는 것을 방지합니다.. 밀링 커터 제조에 따른 직경 감소 및 끝 직경 감소로 인해 부품 가공 크기의 편차가 발생합니다..
부품이 대량생산되기 전, 밀링 백킹 플레이트가 CNC 밀링 테이블에 설치되고 새 나일론 스레드 플러그가 나사로 고정됩니다.. 나사산 플러그에 구멍을 뚫고 위치 결정 핀을 설치하여 사용합니다.. 밀링 패드의 칩 홈이 더 깊고 넓어졌습니다., 공기 흐름을 원활하게 하는 데 더 도움이 됩니다., 칩 제거, 처리할 표면이 더 매끄러워집니다.. 하지만, 지지면이 약해짐, 특히 칩 플루트가 포지셔닝 핀에 가까울 때, 위치가 불안정해질 수 있습니다..
하드웨어 부품 설계에 사용되는 대부분의 밀링 패드는 비금속 라미네이트를 사용합니다.. 재질은 비교적 부드럽습니다. 핀을 반복적으로 로드하고 언로드하는 경우, 위치 지정 구멍이 마모되고 확대되었습니다.. 예를 들어, 반특정 및 소모성 밀링 패드는 이러한 조건에서 작동합니다..
대개, 핀이 밀링 패드에 압입됩니다., 간섭은 0.005~0.01mm입니다.. 밀링패드로 특수밀링패드나 고밀도 섬유판인 경우, 더 타이트한 핏이 더 좋아요. 그러나 준특수 밀링 패드 또는 소모성 밀링 패드의 경우, 간섭이 0.007mm보다 큽니다.. 핀을 압입한 경우, 핀홀의 모재 일부를 잘라내어 깊은 홈이나 틈을 형성하는 것이 가능합니다.. 핀을 반복적으로 로드하고 언로드하는 경우, 라미네이트의 핀 구멍에도 박리 또는 치핑이 있습니다.. 부품을 밀링할 때, 대부분의 절단력은 포지셔닝 핀에 의해 전달됩니다.. 이 측면압력이 핀홀을 압박하게 되고 홀의 결함으로 인해 핀이 헐거워지고 하나씩 어긋나게 됩니다.. 인쇄 기판의 외부 치수에 직접적인 영향을 미치며 엄격한 공차를 보장할 수 없습니다..
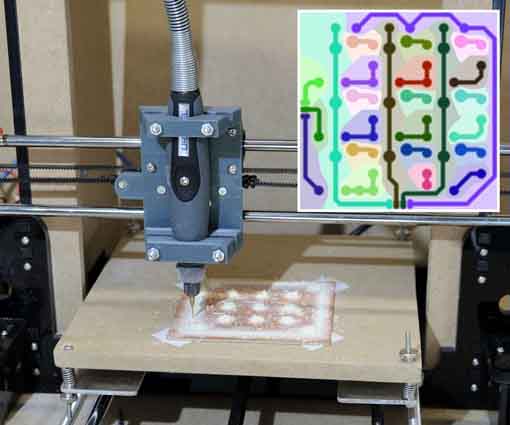
CNC 밀링 PCB 보드의 포지셔닝 설계
포지셔닝 핀의 직경이 작을수록, 상대적 편향이 클수록. 그러므로, 직경이 큰 구멍은 가능한 한 위치 결정 구멍으로 사용해야 합니다.. 포지셔닝 핀의 직경과 처짐도 생산성에 직접적인 영향을 미칩니다.. 예를 들어, 4개의 PCB 보드 스택은 원래 한 번에 밀링되도록 설계되었습니다.. 핀의 직경이 작고 처짐량이 크기 때문에, 효율을 줄이기 위해 PCB 보드 3개를 밀링해야 했습니다. 25%.
PCB 프로토타입 가공 과정에서, 프로세싱 보드의 안정적인 위치를 보장하려면 위치 핀이 밀접하게 일치해야 합니다.. 접착 테이프나 접착제의 도움에 의존하는 대신, 결합하고 치료하는 데 시간이 걸립니다.. 꼭 맞는 핏은 엄격한 공차를 의미합니다., 다층 기판이나 고품질 양면 기판을 밀링하여 정밀도를 보장할 수도 있습니다..
일반적으로, 드릴 직경은 더 낮은 편차입니다, 일반적으로 0~0.005mm입니다., 일부는 0~0.01mm입니다.. 대부분의 비금속 라미네이트는 드릴링 후 일정량의 수축이 발생합니다., 대개 0.005 0.007mm까지. 표준 핀과의 편차가 0.005~0.01mm 더 낮은 구멍은 0.005mm의 간섭을 일으킬 수 있습니다.. 그러므로, 특별한 가공 기술을 고려할 필요가 없습니다., 드릴 비트의 직경을 하나씩 측정하지도 않습니다., 압입 요건을 충족하고 시간을 절약하려면 작은 직경의 드릴 비트를 선택하세요..
예를 들어, 특정 1.6mm 두께의 인쇄 회로 기판, 공차 ±0.013mm, 매번 4개의 PCB 보드 스택을 밀링합니다.. 구멍 위치 공차는 +/-0.025mm입니다., 구멍 직경 차이는 ±0.025mm입니다., 표준 핀을 사용하여. 그런 다음 PCB 보드를 로드하고 언로드하는 것은 어렵고 시간이 많이 걸립니다.. 밀링된 플레이트에 핀을 잠글 수 있기 때문에. 이 예는 핀과 퀼트가 더 느슨한 슬립 핏으로 맞춰져야 함을 나타냅니다.. 물론, 간격이 너무 큰 경우, 가공 정확도와 모서리 부드러움에 영향을 미칩니다..