이상적인 CNC 가공 프로그램은 도면에 맞는 적격 공작물이 가공되도록 보장할 뿐만 아니라, 뿐만 아니라 CNC 공작기계의 기능을 합리적으로 적용하고 최대한 활용할 수 있도록 해야 합니다.. CNC 공작기계는 매우 효율적인 자동화 장비입니다.. 그 효율성은 2 에게 3 일반 공작기계보다 몇 배 더 높은 성능. 그러므로, CNC 공작기계의 이러한 기능을 최대한 활용하기 위해, 성능을 마스터해야합니다, 형질, 및 운영 방법. 동시에, 프로그래밍하기 전에 가공 계획을 올바르게 결정해야 합니다..
생산 규모의 차이로 인해, 동일한 부품에 대한 가공 계획이 다릅니다.. 특정 조건에 따르면, 경제적이고 합리적인 공정 계획을 선택해야 합니다..
(1) 처리절차 구분
CNC 공작 기계의 가공 부품을 공정에 더욱 집중시킬 수 있습니다., 모든 프로세스는 가능한 한 한 번의 설정으로 완료되어야 합니다.. 일반 공작기계 가공에 비해, 처리 절차의 구분에는 고유한 특성이 있습니다., 절차 분할에는 일반적으로 사용되는 두 가지 원칙이 있습니다..
1. 정확성 보장의 원칙
수치제어 처리는 최대한 프로세스를 집중시켜야 합니다., 거친 가공과 미세한 가공이 한 번의 클램핑으로 완료되는 경우가 많습니다.. 열변형과 절삭력 변형이 형상에 미치는 영향을 줄이기 위해, 위치 정확도, 공작물의 치수 정확도 및 표면 거칠기, 황삭 및 정삭 가공은 별도로 수행해야 합니다.. 샤프트 또는 디스크 부품용, 거친 가공이 먼저 수행됩니다, 표면 품질 요구 사항을 보장하기 위해 마무리를 위해 약간의 여백을 남겨 둡니다.. 동시에, 일부 박스 공작물의 경우, 홀 가공의 정확성을 보장하기 위해, 표면을 먼저 처리한 후 구멍을 처리해야 합니다..
2. 생산 효율성 향상 원칙
CNC 가공에서, 공구 교환 횟수를 줄이고 공구 교환 시간을 절약하기 위해, 동일한 도구로 가공해야 하는 부품이 모두 완성된 후, 다른 부품을 처리하려면 다른 도구를 사용해야 합니다.. 동시에, 공회전 스트로크를 최소화해야 합니다.. 동일한 공구로 공작물의 여러 부분을 가공하는 경우, 각 처리 부분에 도달하려면 최단 경로를 사용해야 합니다..
실제로, CNC 가공 공정은 특정 부품의 구조적 특성과 기술 요구 사항에 따라 종합적으로 고려해야 합니다..
(2) 처리 경로 결정
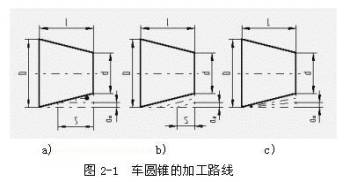
터닝 콘 부품의 가공 경로
CNC 가공에서, 도구의 이동 경로 및 방향 (엄밀히 말하자면, 도구 위치 점) 공작물과 관련된 가공 경로를 가공 경로라고 합니다.. 그건, 공구 설정 지점에서 가공 프로그램 끝까지 공구가 이동하는 경로, 절삭 경로와 공구 투입 및 복귀 등 비절삭 유휴 스트로크 포함. 처리 경로를 결정하려면 먼저 처리된 부품의 치수 정확도와 표면 품질을 보장해야 합니다., 두 번째로 간단한 수치 계산을 고려하십시오., 가능한 가장 짧은 공구 경로, 그리고 더 높은 효율성.
다음 예에서는 CNC 공작 기계로 부품을 가공할 때 일반적으로 사용되는 가공 경로를 분석합니다..
1. 터닝콘의 가공경로 분석
CNC 선반의 외부 원추 회전용, 원뿔의 장경이 D라고 가정, 작은 직경은 d입니다, 원뿔의 길이는 L, 터닝 콘의 가공 경로는 그림에 나와 있습니다. 2-1.
그림 2-1a의 계단식 절단 경로에 따르면, 2절삭 황삭 터닝, 그리고 마지막 원컷 미세 터닝; 2회 황삭 터닝의 최종 공구 거리 S를 정확하게 계산해야 합니다., 비슷한 삼각형을 가질 수 있는 것:
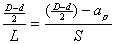
계단형 부품의 절단 경로 설계
이런 종류의 처리 경로에 대해서는, 터닝 두께는 황삭 터닝과 동일합니다., 하지만 미세가공의 경우 터닝 두께가 다릅니다.; 동시에, 공구의 절단 경로가 가장 짧습니다..
그림 2-1b의 유사한 경사 절단 경로에 따르면, 황삭 선삭 중에 최종 공구 거리 S를 계산하는 것도 필요합니다., 이는 유사한 삼각형에서도 계산할 수 있습니다.:

공구 절삭 동작의 최단 경로 설계
이 처리 경로에 따르면, 공구의 절단 거리가 상대적으로 짧습니다..
그림 2-1c의 사선 처리 경로에 따르면, 매번 백툴 AP의 양만 결정됩니다, 최종 공구 거리를 계산하는 대신, 프로그래밍이 편리하다. 하지만, 각 절단의 두께가 변경됩니다., 공구의 절단 경로가 더 길어집니다..
2. 터닝아크의 가공경로 분석
G02 사용 (또는 G03) 호를 돌리는 명령. 1회 회전하여 원호를 가공하면, 칼의 양이 너무 많아 칼에 찔리기 쉽다. 그러므로, 호의 실제 회전에서, 다중 절단이 필요합니다, 다량의 초과분을 먼저 제거합니다., 그런 다음 필요한 호가 회전됩니다..
다음은 호 회전의 일반적인 가공 경로를 설명합니다..
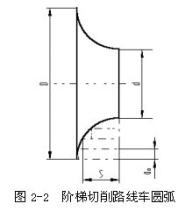
스텝 절삭 경로 설계를 위한 터닝 아크
수치 2-2 터닝 아크의 스텝 절단 경로를 보여줍니다.. 그건, 첫 번째 거친 터닝은 단계로 이루어집니다., 호는 최종 절단으로 절단됩니다.. 이 방법에서는, 터닝 두께 ap가 결정된 후, 황삭의 최종 공구 거리 S를 정확하게 계산해야 합니다., 그건, 호와 직선의 교차점이 계산됩니다.. 이 방법에서는, 공구의 절단 이동 거리가 더 짧습니다., 하지만 수치 계산은 더 복잡합니다.
수치 2-3 터닝 아크의 동심 아크 절단 경로를 보여줍니다.. 그건, 다른 반경의 원으로 회전, 마지막으로 필요한 호를 처리합니다.. 이 방법은 각 공구의 ap량을 결정한 후 90° 호의 시작점과 끝점 좌표를 결정하는 것이 더 쉽습니다.. 수치계산은 간단하다, 그리고 프로그래밍이 편리해요, 그래서 자주 쓰인다. 그러나 그림 2-3b에 따라 처리하는 경우, 유휴 스트로크 시간이 길어집니다..
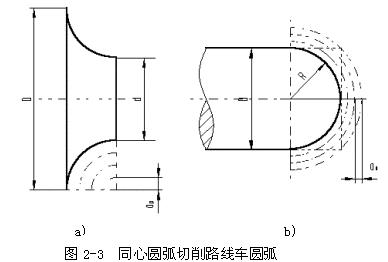
동심 호의 절단 경로 호를 설계합니다.
수치 2-4 원호를 회전시키기 위한 터닝콘 방식의 절단 경로를 보여줍니다.. 그건, 먼저 원뿔을 돌립니다, 그런 다음 호를 돌립니다.. 하지만, 원뿔의 시작점과 끝점이 잘 결정되지 않은 경우 주의해야 합니다., 콘 표면이 손상될 수 있습니다., 또는 여백이 너무 크게 남아 있을 수 있습니다.. 결정 방법은 그림에 나와 있습니다. 2-4. OC를 연결하여 D의 호와 교차합니다., 점 D를 통과하는 호의 접선 AB를 만듭니다..
기하학적 관계로부터 CD=OC-OD= -R=0.414R, 이것은 테이퍼를 돌릴 때의 최대 절삭 여유입니다., 그건, 테이퍼를 돌릴 때, 처리 경로는 AB 라인을 초과할 수 없습니다.. 그림에 표시된 관계에 따르면, AC=BC=0.586R 을 얻을 수 있습니다., 원뿔의 시작점과 끝점을 결정할 수 있습니다.. R이 너무 크지 않은 경우, AC=BC=0.5R을 사용할 수 있습니다.. 이 방법의 수치 계산은 복잡합니다., 공구의 절단 경로가 짧습니다..
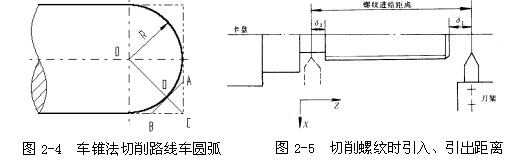
Turning the arc with the cutting path of the turning cone method
3. Analysis of Axial Feeding Distance When Turning Thread
When turning the thread, the feed of the tool along the thread direction should maintain a strict speed ratio relationship with the rotation of the workpiece spindle. Considering that the tool reaches the specified feed rate from the stopped state or drops from the specified feed rate to zero, the drive system must have a transition process. The length of the processing route along the axial feed, in addition to ensuring the thread length, should also increase the tool lead-in distance of δ1 (2~5mm) and the tool cutting distance of δ2 (1~2mm), 그림과 같이 2-5 . This is to ensure that when cutting threads, the tool will contact the workpiece after the speed increase is completed, 공작물을 떠난 후 공구 속도가 느려집니다..
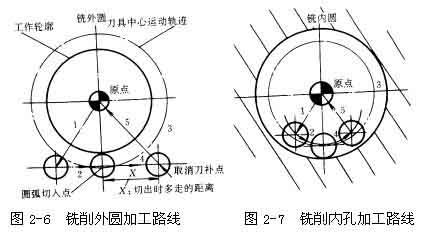
밀링 부품의 외부 원 가공 경로
4. Contour Milling 가공경로 분석
연속 밀링 윤곽용, 특히 호를 처리할 때, 도구 절단 및 절단 배열에 주의하십시오., 교차점에서 반복되는 처리를 피하려고 노력하십시오., 그렇지 않으면 명백한 경계 밀링 마크가 있을 것입니다.. 그림과 같이 2-6, 외부 원을 밀링하기 위해 원호 보간을 사용할 때, 접선 방향에서 원주 밀링 공정에 들어가도록 커터를 배열합니다.. 전체 원이 처리된 후, 접선 지점에서 공구를 직접 후퇴시키지 마십시오., 하지만 도구를 특정 거리만큼 움직이게 하세요.. 공구 보정이 취소될 때 공구와 공작물 표면 사이의 충돌을 피하기 위해 접선 방향을 따르는 것이 가장 좋습니다., 공작물이 폐기되는 원인. 내부 호를 밀링할 때, 접선 방향에서 절단하는 원리도 준수해야 합니다., 전환 호는 잘라내고 잘라내도록 배열되어야 합니다., 그림과 같이 3-7. 공구가 공작물 좌표의 원점에서 시작하는 경우, 처리 경로는 1→2→3→4→5입니다., 내부 구멍 표면의 가공 정확도와 품질을 향상시키기 위해.
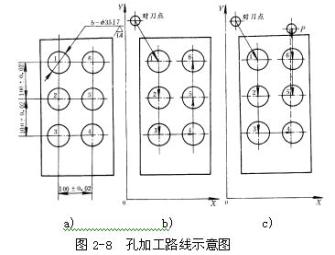
부품 구멍 가공 경로 설계
5. 높은 위치 정확도로 구멍 가공 경로 분석
높은 위치 정밀도가 요구되는 홀 가공용, 구멍 처리 순서 배열에 특별한 주의를 기울여야 합니다.. 잘못 배치하면 좌표축을 따라 백래시가 발생하여 위치 정확도에 직접적인 영향을 미칠 수 있습니다.. 그림과 같이 2-8, 그림 a는 부품도이다. 이 부품에서 처리된 동일한 크기의 구멍 6개에 대해 두 가지 처리 경로가 있습니다.. 그림 b에 표시된 경로에 따라 가공하는 경우, 구멍의 위치 방향 5 그리고 6 구멍과는 반대 1, 2, 3 그리고 4. Y 방향의 역 클리어런스는 위치 오류를 증가시키고 구멍의 위치 정확도에 영향을 미칩니다. 5 그리고 6 그리고 다른 구멍. 그림 c에 표시된 경로에 따르면, 처리 후 4 구멍, P 지점까지 이동, 그런 다음 다시 프로세스로 돌아갑니다. 5 그리고 6 구멍. 이런 식으로, 방향은 일관적이다, 백래시 발생을 방지하고 구멍의 위치 정확도를 향상시킬 수 있습니다. 5 그리고 6 그리고 다른 구멍.
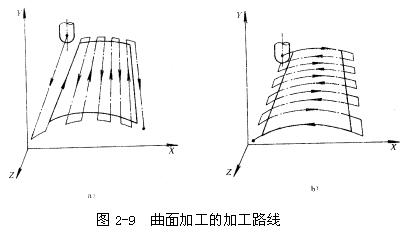
부품 표면의 가공 경로 설계
6. 밀링 표면 가공 경로 분석
곡면을 밀링할 때, 볼 엔드 나이프는 일반적으로 다음과 같은 가공에 사용됩니다. “와이어 절단 방법”. 소위 와이어 절단 방법은 공구의 접선 트랙과 부품 윤곽이 한 줄씩 이어짐을 의미합니다., 선 사이의 거리는 부품의 가공 정확도 요구 사항에 따라 결정됩니다.. 열린 경계가 있는 표면 가공용, 두 가지 가공 경로를 사용할 수 있습니다.. 그림과 같이 2-9, 대형 엔진 블레이드용, 그림 2-9a의 처리 방식을 사용하는 경우. 직선으로 처리될 때마다, 도구 위치 점 계산은 간단합니다., 프로그램이 적다, 가공 공정은 괘선 표면의 형성을 따릅니다., 버스의 직진성을 정확하게 보장할 수 있습니다.. 그림 2-9b에 표시된 처리 계획을 사용하는 경우, 이 유형의 부품에 대한 데이터는 처리 후 쉽게 검사할 수 있도록 제공된 정보와 일치합니다.. 임펠러 형상의 정밀도가 높다, 근데 절차가 너무 많아서. 표면부분의 경계가 열려있기 때문에, 다른 표면 제한은 없습니다, 표면의 경계를 확장할 수 있습니다., 볼 엔드 나이프는 경계 외부에서 처리를 시작해야 합니다..
위는 몇 가지 예를 통해 CNC 가공에서 일반적으로 사용되는 가공 경로를 분석했습니다.. 실제 생산 중, 처리 경로의 결정은 부품의 특정 구조적 특성을 기반으로 해야 합니다., 포괄적인 고려와 유연한 사용. 처리 경로를 결정하는 일반 원칙은 다음과 같습니다.: 부품의 가공 정밀도 및 표면 품질을 보장하는 조건, 생산성 향상을 위해 가공 경로를 최대한 단축.